インドネシアに限った話ではないですが、製造業の至上命題は「生産性向上によるコスト削減」と「納期遅れせずきっちりと納品する」の2つであるとはよく言われることです。
経営側は市場の需給調整に基づいて事業の発展を最大化する事業計画を作成しますが、安売りで売上が増えたとしても売上総利益が小さくなるだけで販売管理費・営業外費用で赤が出る、かといって販売単価は市場価格を考慮する必要があるため簡単には上げられないので、材料の購入から製品となるまでの生産性向上によるコスト削減を目的とした生産計画に基づく工程管理が重要になるのです。
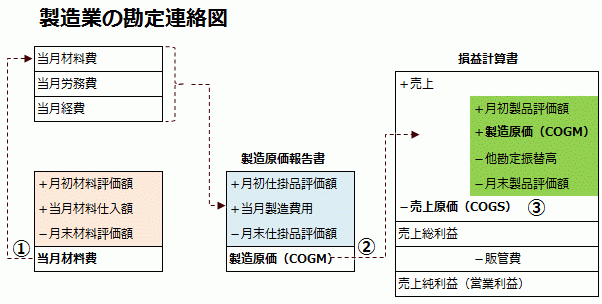
製造業の勘定連絡図
- 月初材料在庫+当月購入材料-月末材料在庫=当月材料費
- 月初仕掛品在庫+当月材料費+当月加工費-月末仕掛品原価=製造原価
- 月初製品在庫+製造原価-月末製品在庫=売上原価
- 売上-売上原価=売上総利益
- 売上総利益-販管費=営業利益
- 営業利益-営業外費用=経常利益
一方で製造現場は生産計画に基づいて生産を行うものの、最終的には顧客からの受注を納期遅れ無く生産することを最優先とします。
インドネシアの日系製造業が置かれる環境のように需要変動が大きい場合には効率の良い生産が難しく、しかも分業化された部署ごとの効率化では全体最適になっていない面もあり、複合的な要素の検証をどのように行って効率の良い生産をするかという難しい課題があります。
DX化とは本来はこの至上命題を同時に達成し、生産性向上を実現することと言えるわけです。
日本の製造業システムでは高いコストをかけてでも自社の業務に合うような機能追加を行いがちですが、インドネシアの場合は限られた予算の中で現場の作業者の入力のしやすさとか、作業負荷の軽減のための画面修正や外部データ取り込み機能の追加に対する要望が多くなる傾向があります。
当ブログではインドネシアの製造業者様で生産管理業務のシステム化の必要性を感じているものの、具体的に何から手を付けたらいいのか分からないという方にとって、インドネシアに合った製造業システムとは何かをイメージするための一助となるような生産管理システムについての記事を書いています。
インドネシアの製造業における計画生産の製造指図とかんばんの違い
「製造指図」も「かんばん」も内示に基づき所要量展開するところは同じですが、製造指図が生産計画に基づく作業単位の実体(演繹的なプッシュ方式)で生産管理部から現場に対する生産指示であるのに対し、かんばんは使った分だけ後工程が前工程から引き取った結果としての実体(帰納的なプル方式)で現場で需要と供給の関係によって自律的に流動します。
かんばん方式対応システムではMRPによって、製造の視点からの製造指図の発行、または工程内かんばん枚数の計算、購買の視点からの材料発注のための所要量計算または材料かんばん枚数計算、設備の視点からのラインや機械の負荷計算ができます。
かんばんは前工程に対するBOX単位の生産指示であり、製造指図合計数量(総所要量-現状在庫+安全在庫)は当月の「かんばん枚数x箱の収容数」とほぼ同数です。
かんばん方式の場合、部品置き場のBOXの数が0で、次に来る引取かんばん分を加工現場の工程内かんばん(仕掛かんばん)でまかなうのが、在庫0かつ工程在庫のみ存在という究極の運用と言えます。
必要な品種を必要な量だけ製造するのはOKだとしても、現場の生産設備で毎日後工程から要求される品種と量がコロコロ変わったらコスト高になってとても対応できないので、かんばん方式運用では品種と量を日ごとに平準化する必要があります。
ロット生産では専門工が段取り回数を減らすために同じものをまとめて生産しますが、平準化生産では色々な種類の製品を均等にばらして生産する必要があるので、実現するには内段取り(主資源段取)の外段取り化(副資源段取)や段取りの標準化によるシングル段取りの実現と多能工化が必要となり、平準化を突き詰めると1個流しに行きつきます。
かんばん方式が急な需要変動に対応できるものでない以上、内示情報から所要量計算をして原材料・外注の手配したり、内示情報から工場資源の予測ベースの能力計画を立てるなど、適切な生産準備(Production preparation)のために生産スケジューラを併用が考えられます。
-
-
インドネシアの製造業における計画生産の製造指図とかんばんの違い
インドネシアの日系製造業で導入される生産管理システムでは、内示情報と確定受注からMRPの所要量展開機能によって製造オーダを生成しますが、トヨタ系自動車部品メーカーではかんばん枚数を計算し、現場に流通しているかんばん枚数に対する過不足を調整します。
続きを見る
スケジューラを使ったインドネシアにおける現場主導型システム
インドネシアではトヨタ車が多く、トヨタ生産方式である「かんばん」が運用されている日系製造業社が多くありますが、コロナ禍後は需要変動ありきの生産を強いられるケースが多く、製造工程の平準化が難しく、欠品及び過剰在庫に対しての要求が高まっています。
需要変動が大きいと月単位の平準化が難しく、プル型の「かんばん」だけでは運用できない面があり、需要変動に合わせたプッシュ型の生産指示の必要性が高くなり、需要変動に合わせた工程毎の生産量をフレキシブルに指示できる計画と、運用として作りすぎを防ぐ「かんばん」による生産調整のハイブリットな生産方式が有効です。 スケジューラを使ったインドネシアにおける現場主導型システム インドネシアの製造現場での自律的な生産調整を得意とするプル型のかんばん方式と、需要変動に合わせて生産指示を発行するプッシュ生産スケジューラ―を併用した生産管理のあり方をご提案させていただきます。 続きを見る
時間基準の稼働率とストローク基準の負荷率の計算方法
タクトタイム(T/T)はトヨタが下請工場に対して、オーダを消化するために1個あたり何秒で加工しなさいと指導する目標値であり、『一日の稼動可能時間÷日当たりオーダ数量』で算出されます。
サイクルタイム(C/T)はトヨタの下請工場の生産管理部が立案した来年度の予定稼働時間と目標生産数から、自社の生産設備の標準能力を『一日の予定稼働時間÷目標生産数』で算出したものです。
トヨタ生産方式TPS(Toyota Production System)では、下請工場に対してシングル段取りにより段取り時間を減らし、サイクルタイムをタクトタイムに近づけるよう指導されます。
タクトタイムやサイクルタイムは稼働時間当たりの生産能力の指標ですが、プレス加工製造の場合は、オーダーを消化するために必要なストローク数の、『GSPHx一日の稼働時間』に対する割合で負荷率を計算します。
代表的な左右セット品として車のドア部品がありますが、2個取り品とは違って左右に分かれた直後の品目(親)の品目コードが異なり、客先からは左右別々にオーダが入るのが普通です。
生産管理システムのMRP(資材所要量計画)機能によって正確な所要量を計算できるものの、負荷率計算で必ずズレが生じるのはラインの生産能力を考慮せず、無限能力で負荷を積み上げていき、負荷オーバ分はマニュアル調整で平準化することを前提としているからです。
一方で生産スケジューラの場合、資源能力100%を超えないようにオーダ数量に応じて所要量を展開し作業をラインに割り付けるという基本思想に基づいているため、左右セット取り品の製造についても正確な負荷計算が可能です。
-
-
時間基準の稼働率とストローク基準の負荷率の計算方法
負荷率は機械の供給能力に対する需要の割合であり、プレス加工でいう1時間あたりのストローク数GSPHに対するオーダを消化するために必要なストローク数の割合です。一方で稼働率は機械の運用時間に対する稼働時間の割合であり、1日の運用時間に対するオーダを消化するために必要な稼働時間の割合です。
続きを見る
ビールゲームで在庫コストと機会損失コストを最小化し全体最適化を実現
生産管理システムは、部門や工程ごとに管理を分けることで部分最適化しますが、部門や工程間を隔てる壁がモノの流れと情報の流れを滞留させ、リードタイムが緩くなり仕掛在庫が増える要因となります。
ビールゲームから学べることは、サプライチェーン間を動く情報とモノの流れの中で、購買発注(購買計画)と製造指図(生産計画)という意思決定の場面で、在庫コスト削減と機会損失低減の重要性を認識した上での意思決定の重要性であり、生産工程を串刺し状につなげ生産に流れを作ることで生産拠点の全体最適化を行うことを目標とする生産スケジューラの導入効果の理解に繋がります。
-
-
ビールゲームで在庫コストと機会損失コストを最小化し全体最適化を実現
ビールゲームの目的は、購買リードタイム4週間、製造リードタイム4週間のサプライチェーンの中で、発注と製造指示という意思決定を行う上で、在庫コストと機会損失コスト(受注残)の削減の重要性を認識することです。
続きを見る
インドネシアで考えるサプライチェーン上での適正在庫
総合商社は扱う商材の幅広さから「よろず屋」的な調達と販売機能を持ち、サプライチェーンの川下から川上までを調整する物流機能を持ち、さらに投資や資本参加により企業育成を行う金融と育成機能を持っています。
このため過剰在庫による在庫コストと在庫切れによる機会損失のリスクを回避しながらデカップリングポイントに最適在庫をキープさせるというサプライチェーン上での最適在庫を実現させることができます。
インターネット黎明期に個人のネットショップが次々と立ち上げられ、個人が大企業と対等に戦える時代が来る、総合商社の役割が終わる言われましたが、サプライチェーンの川上(原料側)から川下(製品側)の全体の物流と金融機能を果たすことで、20年後の今も人気就職先上位に居るのは凄いことです。 インドネシアで考えるサプライチェーン上での適正在庫 総合商社は代理店業からサプライチェーンの川上から川下の全体で付加価値に見合う利益を上げるビジネスモデルに転換し、サプライチェーン全体の最適化を図る物流戦略を描くことで、時間短縮や規模の経済性による価格値下げという形で消費者利益に寄与します。 続きを見る
インドネシアの日常生活の事例から考える部分最適化と全体最適化
本来渋滞を最小限に抑える方法は、すべての車が車線変更することなしに、完全停止にならない程度に徐行し合うことですが、現実には一刻も早く目的地に到着したいという気持ちと、じっとしていると自分だけが馬鹿を見るという疑念を持つ運転者の集団の中では、個人の最適化を優先するために車線変更が繰り返された結果として渋滞が悪化します。
このように利害関係がバラバラな集団の中では個人の感情に基づく部分最適化された判断が横行し渋滞が悪化するわけですが、運転者全員が他人を思いやる気持ちを持ち、相手の利益を尊重するために自分の欲望に制限をかけることが出来れば、渋滞の早期解消という全体最適化が実現し、全員が早く帰宅できるわけです。
会社や軍隊などの組織体は、利益最大化という同じ目標のために、個人のわがままを抑制させることが出来るという点で、日常生活をおくる社会全体とは大きく異なります。 インドネシアの日常生活の事例から考える部分最適化と全体最適化 最適化の基準は、渋滞の場合はスループット(単位時間あたりの総移動量)、市場原理の中のプレイヤーとしての企業活動の場合は利益増大、製造業の生産活動の中では生産性向上やコスト削減というように立場によって異なります。 続きを見る
インドネシアでの製造業IoTの導入による稼働管理・傾向管理・予知保全
インドネシアの製造業でも、担当者同士の物理的接触を最小限に抑えるペーパレス化と紙やPCなどモノを介した間接的な接触を最小限に抑えるIoT化の重要性は認識されており、生産計画作成から製造管理、工数管理、品質管理、稼働管理など一連の生産プロセスを統合化し、自動化、無人化を進める生産製造オペレーション管理(Manufacturing Operations Management=MOM)を目指すことになります。
機械の稼働管理では、PLCや信号灯から取得される信号から稼働時間と停止時間を取得し、生産効率を時間稼働率(Availability factor)、性能稼働率(Performance factor)、良品率(Yield)という3つの側面から計算される総合設備効率(OEE)を計算するのが目的です。
保全管理とは機械が壊れないように日頃からメンテナンスすることであり、設備の日々の変化や故障傾向を数値で分析し、設備カルテやトラブル事例を全部門で共有しますが、プレス機のショット数や稼働時間から定期的に部品(スペアパーツ)交換などのメンテナンスを行う「予防保全」と、機械に問題が発生する兆候を予測する「予知保全」に分かれます。
-
-
インドネシアでの製造業IoTの導入による稼働管理・傾向管理・予知保全
製造業IoTで「モノとインターネットが繋がる」とは、製品など生産財の実績数量・時間や、機械など資本財の保全情報の収集を指しますが、予知保全のために稼働管理や傾向管理を行い、データを機械停止の防止や性能劣化の原因分析に役立てることが生産性向上に直結します。
続きを見る
インダストリー4.0を実現するインドネシアのスマートファクトリー
製造業システムは生産管理、生産計画、販売購買管理、在庫管理というビジネス機能によって区分される統合基幹業務システム(Enterprise Resource Planning=ERP)から、人や機械といった製造現場レベルの管理に重点を置いた製造実行システム (Manufacturing Execution System=MES)へとシフトしており、今後は計画・スケジューリング・製造管理・工数管理・品質管理など一連の生産プロセスを統合化し、自動化・無人化を進める生産製造オペレーション管理(Manufacturing Operations Management=MOM)に移行していくことが予測されます。
MESは上位のERP層と下位のPLC層の間に位置し、生産スケジュールに基づいて作業員(ヒト)に作業指示を出し、原材料や仕掛品など(モノ)の動きをリアルタイムで監視し、生産設備(機械)に直結し稼働状況や異常発生を把握し、MESをデジタル化によって自動化を推し進めスマートファクトリー化を実現するスキームがMOMになります。
情報をデジタルネットワークに乗せるまでに発生しうる間違いとして、紙に書いた情報をシステムに入力する際の転記間違い、システムへの入力間違いがありますが、ペーパレス化とIoT化により、最も即効性のある対応が可能な部分です。
インダストリー4.0では、ソフトウェア側中心に実装されたIT技術をハード側に移管し、ハードとネットワークが繋がることで、よりすばやく正確なデータ収集と分析を行い、生産性向上や品質向上に繋げようということです。
-
-
インダストリー4.0を実現するインドネシアのスマートファクトリー
製造業のDX化によってインダストリー4.0が具現化されたものがスマートファクトリーという概念であり、具体的にはMES(製造実行システム)により生産効率の向上と製造コスト削減のために現場レベルの情報を収集・管理を行い、さらにMOM(生産製造オペレーション管理)による自動化を推し進めます。
続きを見る
現場でできる!インドネシア製造業向け工場内の業務効率化&見える化
生産スケジューラAsprovaで生産計画を作成し、サイボウズキントーンでタブレットから製造実績を記録し、ウイングアークMotion Boardで予定と実績のデータを可視化するというPDCAを回すという設定での共催セミナーを開催しました。
近年のインドネシア日系製造業が直面する課題として製品寿命の短命化とそれによる多品種少量生産、需要変動、人件費上昇、非日系企業との競争などが挙げられますが、これに対処するための最大の努力目標は生産効率の向上であり、工場全体の生産資源を最適化し在庫コストと機会損失リスクを減らす必要があります。
生産スケジューラでは受注から生産、購買まで一気通貫で見える化し、設備能力を考慮したサイクルタイムベースの生産計画を作成することにより、リードタイム短縮による単位時間あたり生産性向上と在庫削減による在庫コスト削減を実現します。
-
-
現場でできる!インドネシア製造業向け工場内の業務効率化&見える化
システムで生産計画を作成し、タブレットで製造実績を記録し、BIツールで予定と実績のデータを可視化するというPDCAを回すという設定です。全体最適化とは、生産効率が最大化され、価格コストと在庫による金利が最小化され、利益が最大化されることです。
続きを見る
インドネシア税関が提供する関税・物品税情報自動化システムCEISAの機能
税関が最も知りたいことは、原材料入荷時の入荷伝票(Surat Jalan)に付番されているBC番号と、製品出荷時に作成する出荷伝票(Surat Jalan)に新たに付番するBC番号の紐付きであり、輸入時に免税された原材料が保税工場内で適切に製品に加工され、適切に出荷されていることが問われます。
BC番号を発行するのはモノを出す側で、CEISAに取引を登録して税関からの承認を得ることで取得でき、KB(保税工場)同士の取引ではモノを出す側のKBがBC27を取得し、相手がNon-KB(非保税工場)の場合はCEISAを導入していないので、KB側で出すときにBC41、入るときにBC40を取得します。
-
-
インドネシア税関が提供する関税・物品税情報自動化システムCEISAの機能
2013年に税関は保税工場に材料や仕掛品、製品、スクラップなどの数量の動きを確認するためのIT Inventoryシステムの導入を義務付けましたが、2019年12月より数量の動きと会計上の金額との繋がりを報告するための会計システムの設置を義務付けています。
続きを見る
インドネシアで生産管理システムの仕様が確定して現場で運用されるまで
現場の作業の動きに対してシステムからどのように指示を出し実績を記録していくかというシステムの運用フローを確定する要件定義では、システムの標準機能で足りないギャップの部分をアドオン開発し、完成したシステムの操作説明会やトレーニングの中で、現場スタッフの生の声を聞きながら仕様変更や追加開発などの微調整を加えていき、システム運用の始まりから終わりまで通しで部門担当者ごとにデータ入力する運用リハーサルの中で、実際の運用にあたって必要になってくる部門間の連携の仕方を確認します。
生産管理システムの導入では予測できない工数が発生しがちで、作業工数を気にしすぎると楽な実装に走りがちになり、これは逆に顧客に対する引け目となり、自信をもって顧客と対峙することが難しくなるため、一旦工数と対価の話がまとまり導入が開始されたら、とにかく顧客の利便性第一に考えること。顧客の業務効率を上げて便利にさせてあげたいという気持ちさえ忘れなければ何の気後れもなくプロジェクト期間中に発生する困難も乗り越えることができる、これがITサービス業者としての矜持です。
そして現場での人とモノの動きに合わせてシステムから指示を出し、実績を入力していくインプリメンテーションのフェーズにて、幽体離脱していた魂が肉体の戻るかのように、これまで積み重ねてきた机上の理論が実体化されていく感覚、業務システム導入の仕事にやりがいとか楽しみを見出すとすればまさにこの瞬間だと思います。
在庫と原価という2つの側面から見た場合には、工場は材料倉庫、製造工程、製品倉庫に分けられ、それらの場所(倉庫)を管轄する部門は一般的には異なり、生産管理の受払実績によって製造原価を算出でき、販売管理の受払実績によって売上原価が算出できるという点からすると、材料倉庫と製造工程が生産場所で製品倉庫が販売場所という分け方になります。
業務フローには数量と金額の2つの流れがありますが、数量の流れを管理するのが在庫管理であり、最低限必要な機能は現状在庫一覧、入出庫履歴管理(ストックカード)、入出庫処理という3つの機能です。
-
-
インドネシアで生産管理システムの仕様が確定して現場で運用されるまで
材料が材料倉庫に入荷してから製造工程で加工されるまでの生産活動と、製品倉庫以降の販売活動をカバーするのが生産管理システムであり、材料が製造工程に投入された時点で材料費と加工費という発生費用となり、製品になった時点で製造原価化し、出荷した時点で売上原価化する、一連の原価の流れを管理するのが原価管理システムです。
続きを見る
ポジション管理におけるロング(買い持ち)とショート(売り持ち)の違いについて
インドネシアにはコーヒー、パーム油などマーケット価格の変動がドラスティックな商材が多いですが、将来の需要や材料価格高騰を見越したや買い契約(ロング)や、販売価格の下落を見越した売り契約(ショート)を行います。ロングポジションでは価格が下落した場合に損失を被り、ショートポジションでは価格が高騰した場合に損失を被ります。
-
-
ポジション管理におけるロング(買い持ち)とショート(売り持ち)の違いについて
在庫ビジネスでは将来の需要や材料価格高騰を見越したや買い契約や、販売価格の下落を見越した売り契約が発生しますが、この場合相場が逆に動いた場合のリスクが発生します。このポジション管理を行うためには、在庫を販売契約に紐付くものと紐付かないものに区別する必要があります。
続きを見る
インボイスとパッキングリストに基づき船会社が貨物の引き受けを証明する船荷証券(B/L)
インドネシアから日本にコンテナで家具を発送する際には、Invoiceとパッキングリストと原産地証明書COO(Certificate Of Origin)に基づきインドネシアの船会社から貨物の引き受けを証明するBill of Landing(船荷証券)を発行してもらう必要があり、輸出の場合はB/L日付が売上計上日となります。
船会社がB/Lをカーゴに送り、カーゴが日本の荷受人(consignee)に発送しますが、カーゴから船会社へのB/L発行フォローが遅れると、荷受人に日本の船会社代理店からArrival Noticeが到着したのにカーゴからのB/Lが発送済み未着で、貨物の受け取りができません。
この場合、船会社による発行済みB/Lをサレンダード(貨物が間違いなく荷受人の荷物であるという船会社による裏書・テレックスリリースとも言う)にして、郵送ではなくFAXで日本の荷受人に送信するよう、カーゴ会社に依頼します。 インボイスとパッキングリストに基づき船会社が貨物の引き受けを証明する船荷証券(B/L) Bill of Landing(船荷証券)は、Invoiceとパッキングリストと原産地証明書COO(Certificate Of Origin)に基づき、インドネシアの船会社が発行する貨物の引き受けを証明するものであり、輸出の場合B/L日付が売上計上日となります。 続きを見る
生産管理システムにおける返品処理の実装のされ方
インドネシアの自動車部品業界では出荷同時売上が基本なので、出荷完了処理によって自動的に売上処理が完了し、返品時はTukar gulingと呼ばれる代替品発送が多いのですが、システム的に行うためには月締め後の返品受注(Return Sales Order Entry)と出荷返品(Return Shipping Entry)によりマイナスインボイス発行、マイナス出荷(返品入荷)、マイナス売上を計上するという流れになります。 生産管理システムにおける返品処理の実装のされ方 インドネシアでの返品処理は、代替品を送ることでオリジナルの出荷伝票(Delivery Note)やInvoiceを修正しないTukar Gulingという方法が一般的です。 続きを見る
インドネシアの業務にスマホを使ったQRコード管理の仕組みを導入
ロット管理の目的はロットトレースと在庫管理の正確性の維持であり、そのためにはシステムから発行する現品票をロットに貼り、現品が流動するたびにをロット番号をキーにシステムに実績入力することで、現品とシステムの一致が保証されていることが大前提です。
ロット単位ではなく場所(工程)単位に実績を上げる場合は「どこに何が何個あるか」が把握できますが、在庫数量の最小のまとまり単位は「場所」である以上、気軽に「現物を数えて理論値が正しいかどうか確認」するのは困難です。
ロットという現品の流動単位で実績を上げる場合は「このロットに何個あるか」は流動先ごとにチェック可能で、役割分担して在庫全体の理論値を常時チェックしていることと同じになり、ロット数量は後工程の実績数量で上書きされるので、後工程にいくほど正確な数量に収斂していきます。
バーコードリーダーはスキャナーとも呼ばれるとおり、単純にバーコードをスキャンしてデータを取り込むまでが役割であり、キーボードからの手入力による手間の省力化と、誤入力防止という2つの目的が果たせれば十分です。
ハンディターミナルと言った場合には、一般的には取り込んだデータをバッチでPCの業務システムに戻すタイプのものを指すようで、事前に作成した指図に対してハンディターミナルで実績を収集します。
バッチ式のハンディターミナルと区別してAndroidやWindows CEなどのOS搭載モデルを無線ハンディターミナルと呼び、スキャンしたバーコード情報を無線で飛ばしてリアルタイムに処理することを目的としています。
生産管理システムから発行した指図に基づいてハンディターミナルで実績を取得し、現品が指図どおりにスキャンされるかチェックしてから基幹システムの実績として連携するケースと、指図なしで現品をスキャンして取得した実績を基幹システムに計上する方法があります。
■指図に対して実績を計上し基幹システムに反映
- 入荷:未検査エリアから材料倉庫へ
検査合格時に現品票貼り付け - 材料出庫(出庫指図):材料倉庫から製造現場へ
- 材料戻し:製造現場から材料倉庫へ
- 製品入庫:製造現場から製品倉庫へ
検査合格時に現品票貼り付け - 出荷(ピッキングリスト):製品倉庫から出荷エリアへ
- 廃棄:倉庫から廃棄エリアへ
- 棚卸(棚卸表):倉庫
■指図がない実績を基幹システムに反映
- 棚移動:棚から棚へ移動
-
-
インドネシアの業務にスマホを使ったQRコード管理の仕組みを導入
業務システムの開発導入でもバーコードやQRの読み込みによるデータ収集はこれまでも行われておりますが、弊社ではここ数年製造現場や倉庫での現場端末の導入を検討されるお客様に対してスマホによるQRコード管理をお勧めしています。
続きを見る
出荷時に現品ラベルの品目ロット情報と照合するためのピッキングリスト
出荷作業ではその日に出荷するモノは倉庫からまとめて取り出して、出荷エリアに積み上げることが多く、出荷の作業単位で1枚にまとめたピッキングリストと現品が合致しているかを照合します。
この場合販売管理の出荷機能の中で、受注情報に紐づいた出荷指示を入力し、出荷指示の明細を仕分けの単位に束ねたものがピッキングリストになり、例えば複数の出荷指示書の明細に対して、今日の日本向けの輸出のために40フィートコンテナ1個に積み込む製品にピッキングリストNOを付番してピッキングリストを作成し、出荷エリアに置かれた製品をスキャンして照合し、照合結果がOKであれば出荷完了登録を実行します。
受注登録から出荷指示、ピッキングによる出荷実績計上までの明細行は品目(ロット)単位に登録されていますが、実際にトラックやコンテナに積み込む際には、破損防止のための梱包作業により複数品目が梱包単位にまとめられ、梱包一覧をパッキングリストとして船会社に提出する必要があります。
-
-
出荷時に現品ラベルの品目ロット情報と照合するためのピッキングリスト
インドネシアの製造業において、出荷時に登録済み出荷指示書一覧の品目ロット明細行を、出荷単位に束ねたものがピッキングリストであり、現品が受注登録時の品目ロットと一致しているかどうかを照合するために使用されるので、出荷指示番号(ヘッダー)と品目ロット番号(明細)で構成され出荷実績が計上されます。
続きを見る
生産管理システムで困っているインドネシアの日系企業様への提言
インドネシアの日系製造業社様から生産管理業務で困っているという話を聞くとき、業務の流れの中で流動するモノがどの出荷に繋がるのか見えない、業務に合わないシステムに無理やり業務を合わせようとすると結局多くのExcel管理が介在するようになる、部門間・部署間の業務フローが繋がらないためにシステム外の無駄な調整が多い、という『見えない・合わない・繋がらない』の問題に帰結します。
会社の事業は市場のニーズに対して何を提供するかで決まり、その事業のために顧客や仕入先とどう付き合うか、社内のスタッフがどう関係するかで社内業務のやり方が決まり、社内業務のすべては会社のお金の入りの源泉である売上(出荷)とお金の出の源泉である購買に繋がります。
サプライチェーン上でモノやサービスに付加価値を付けて流す行為の集積が経済活動なのであって、付加価値を生み出さずして単にサプライチェーン上のお金を吸い上げるだけの行為は経済活動とは呼べません。
インドネシアのように、社内の意思決定が個人や部署の政治的意図によって押し切られたり、サプライチェーンの制約が原因で顧客・仕入先・外注先との商慣習が複雑化するような環境では、社内業務のやり方は独自の文化に染まっていき、関係者それぞれが一番やりやすいやり方を模索した結果、部分最適の集合体になりやすい。
これらの部分最適同士を繋ぎ合わせるための補修剤としてExcelが重宝されるのであって、独自の社内文化で形成された業務のやりかたの中から重要な要件をとりまとめ、地道に要件をまとめてシステムで実装していくしかないわけで、インドネシア人スタッフの心情に配慮して「システムから出てきた結果がどのようなプロセスを経てきたのか見える」ように配慮します。 生産管理システムで困っているインドネシアの日系企業様への提言 社内業務のすべては会社のお金の流入の源泉である売上とお金の流出の源泉である購買に繋がるわけでで、現状が見えない・数字が合わない・前後が繋がらないという3つの問題により、業務効率が低下するだけでなく、社員の売上コスト意識の低下に繋がります。 続きを見る
インドネシアにおける業務改善を実現するITシステム内製化の可能性
インドネシアの日系製造業社様ででITシステム構築を検討するとき、外製化の弱点は環境の変化に伴う業務の流れに対応しずらい、いざ内製化しようとしても社内にITスキルのある人材はいない、職人的なIT技術者が開発したシステムは属人化しやすいという外製化と内製化の問題に行き当たります。
インドネシアのITシステムによる業務改善の理想とは「Excelのように環境の変化に合わせて柔軟に修正ができ、高度なIT技術が不要で社内の業務担当者の力で構築できるもの」であり、このような都合の良いITツールは存在しなかったため外製化にならざるを得なかったわけですが、KintoneやAppSheetの登場により現実的な提案が出来る時代になりつつあります。 インドネシアにおける業務改善を実現するITシステム内製化の可能性 KintoneやAppSheetが提供する機能が高度化するにつれて、インドネシアでも業務システムの内製化が出来る時代になりつつあります。ITによる本質的な業務改革は外製化よりも内製化のほうが有利であると考えます。 続きを見る
インドネシアで使えるシステムと使いやすいシステム
- 夜勤の実績が翌朝上がりマイナス在庫でDOが発行できない。
- モノ到着Invoice未到着だと仕入登録ができず在庫計上されず出荷できない。
- 出荷指示が在庫引当前提でモノがなく前日に出荷指示が出せない。
- 受注済み未出荷は受注残として把握できるが受注済み未出荷指示が把握できない。
- 入荷即投入され製造原価化した材料のInvoiceが未着で原価計算対象とならない。
- 締処理前に入出荷の修正が終わらないと実地棚卸の反映ができない。
- イレギュラー処理(材料払出・戻入処理・NG・別管理品)の実績入力や現品票発行が追いつかない。
- 実地棚卸で発覚した実績間違いを修正したいが、ロットが客先まで流動している場合にDOやInvoiceをキャンセルするとInvoice番号やDO番号が新たに採番されてしまう。
-
-
インドネシアで使えるシステムと使いやすいシステム
プロジェクトの成功とはスケジュールどおりに完了しシステムが要件どおりに動くことです。その結果インドネシアで使えるシステムが出来たということですが、使いやすいシステムとはやりたい操作がすぐ見て分かる優しい画面構成になっているということです。
続きを見る