In the context of IoT in manufacturing, "connecting things to the internet" refers to collecting data on the actual quantities and times of production goods like products, as well as maintenance information for capital goods such as machinery. However, conducting operational and trend management for predictive maintenance, and using that data to prevent machine downtime or analyze the causes of performance degradation, directly contributes to productivity improvements. Production Control System in Indonesia It’s not limited to Indonesia, but it’s often said that the ultimate goals of the manufacturing industry are twofold: "cost reduction through productivity improvement" and "delivering products on time without delays." From a management perspective, business plans are crafted to maximize growth based on market supply and demand adjustments. However, even if sales increase due to low pricing, it only reduces gross profit, leading to losses from selling and administrative expenses or non-operating costs. On the other hand, raising unit prices isn’t straightforward due to market price considerations. Therefore, process management based on production plans aimed at reducing costs through ... 続きを見る
Paperless Solutions to Minimize Physical Contact Between Personnel
At our company, we have long asserted through this blog and regular seminars at industrial parks that paperless solutions should be the first challenge tackled to improve operations for Japanese companies in Indonesia. This is not only for cost savings through reduced paper use but primarily to prevent errors in transcribing performance data onto paper.
The typical customer response at the time was, "We can’t do it right away, but we’d like to tackle it when the next budget is available," which was positive but not seen as an urgent issue. However, with the spread of COVID-19, paperless solutions have become an urgent matter.
Handing over production instructions or daily reports to personnel requires physically approaching their workstation. If a cluster of infections via droplets or contact occurs in a factory, it could lead to line stoppages or, in the worst case, a temporary suspension of operations. Thus, the priority of measures to minimize physical contact has inevitably increased.
Currently, cluster infections of COVID-19 in Indonesia are most common during group worship at religious facilities like mosques or through hospital-acquired infections. Despite the PSBB (large-scale social restrictions) and the ban on Mudik (homecoming), some contact with relatives or acquaintances is still likely. As a result, concerns about the spread of infection when factories resume operations after the Lebaran holiday have not been fully alleviated.
IoT Solutions to Minimize Indirect Contact via Objects like Paper or PCs
Even if physical contact with others is minimized in a factory, the coronavirus can survive for hours on objects like paper or steel. If the virus lingers on paper or shared PCs touched by others, the risk of indirect contact infection remains. Ultimately, this calls for a system that minimizes physical tasks and machine operations, automating processes instead.
Specifically, collecting production performance data for inventory management in a production management system can be automated by linking information from machine counters through a sequencer. Meanwhile, machine operation management—previously handled outside the production system—can be digitized by attaching IoT gateways and sensors to patlights (andon), capturing uptime and downtime data. These are examples of advancing IoT adoption.
However, due to reduced production and sales from the COVID-19 impact, IT investment is likely the first area to face budget cuts next year. Even if IoT investment isn’t approved, focusing solely on reducing indirect contact through objects can still be achieved by introducing a system where data input is done via individual Android smartphones, mitigating the risk of indirect contact infection.
Unexpectedly, the COVID-19 crisis is likely to accelerate paperless and IoT adoption in Indonesia’s manufacturing sector. Moving forward, integrating and automating the entire production process—from production planning and scheduling to manufacturing, labor management, quality control, and operational management—through Manufacturing Operations Management (MOM) will gain increasing attention. This will be driven not only by productivity improvements but also by the need to reduce virus infection risks.
Why IoT in Manufacturing Is Necessary in Indonesia
When visiting customers in industrial parks for system sales in Indonesia, a common remark from personnel has been, "Our president (or chairman) is eager to invest in machinery but reluctant to invest in systems."
This is a frequent sentiment among small and medium-sized owner-operated companies that have survived in Indonesia by focusing solely on boosting production capacity. This approach worked in an era of steady, growing orders from specific customer clusters, such as exports to Japan or Japanese firms in Indonesia.
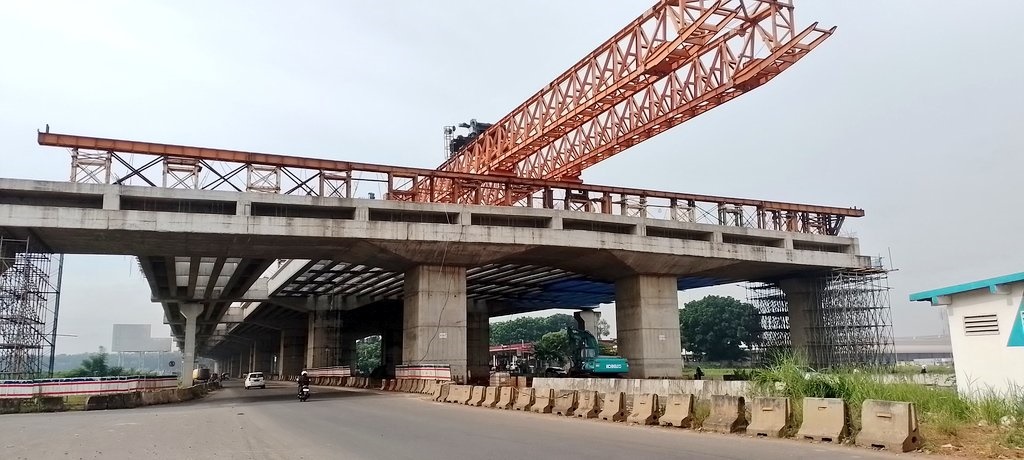
However, in an era where large, stable orders from major clients are no longer guaranteed, and companies must accumulate smaller orders from multiple clients to maintain performance, efforts to enhance competitiveness through productivity-driven cost reductions—the ultimate goal of manufacturing—become essential.
This also applies to the export competitiveness of Indonesia’s domestic industries. Despite a production capacity of over 3 million vehicles, Indonesia’s automotive production has stagnated at under 1 million due to a lack of export competitiveness.
Increasing national wealth requires boosting export competitiveness, and to achieve this through IT-driven productivity gains, the Indonesian government has promoted Making Indonesia 4.0, its version of Industry 4.0. However, concrete guidelines remain absent.
As of February 2020, the mindset is shifting from "we’ll invest in machines but not systems" to "we need this to compete globally." The purpose of introducing IoT in manufacturing is to collect data on capital goods (machinery and people) to efficiently manage the flow of production goods like materials, work-in-progress, and finished products.
What IoT in Manufacturing Entails
In manufacturing IoT, "things connected to the internet" refer to "production goods (industry goods)" and "capital goods." Production goods include materials, work-in-progress, and products, while capital goods include machinery and people.
The information collected about production goods includes inputs, outputs, yield, and defects ("results"), while data on capital goods includes direct time (operation or work hours), indirect time (downtime), and conditions like temperature or RPM ("status").
- Results: Performance data on production goods ⇒ Inputs, outputs, yield, defects
- Results: Quality control data on production goods ⇒ Defect reasons, defect images
- Status: Maintenance data on machinery ⇒ Direct time (operation hours), indirect time (downtime), temperature, RPM, stroke count
- Status: Maintenance data on people ⇒ Direct time (work hours), indirect time (break time)
This is the information collected from production and capital goods in manufacturing IoT. Items 1 and 2 were traditionally managed in ERP systems, while 3 and 4 fall under Manufacturing Execution Systems (MES), with the goal of providing data to improve production efficiency.
Equipment Maintenance Management
Maintenance involves daily upkeep to prevent machine breakdowns. The maintenance department’s tasks include "preventive maintenance" (e.g.,定期的にスペアパーツを交換する based on press shot counts or operation hours) and "predictive maintenance" (forecasting signs of potential issues).
Our company offers an IoT system that converts existing patlights or analog meters into numerical data, performs data analysis for predictive maintenance, and visualizes machine uptime and performance changes to enable operational and trend management.
- Operational management ⇒ Collect uptime data by capturing light signals from patlights with optical sensors.
- Trend management ⇒ Convert analog meters (e.g., thermometers, ammeters) into numerical data via image analysis.
Using this data to prevent future machine downtime or analyze the causes and correlations of performance degradation directly enhances productivity.
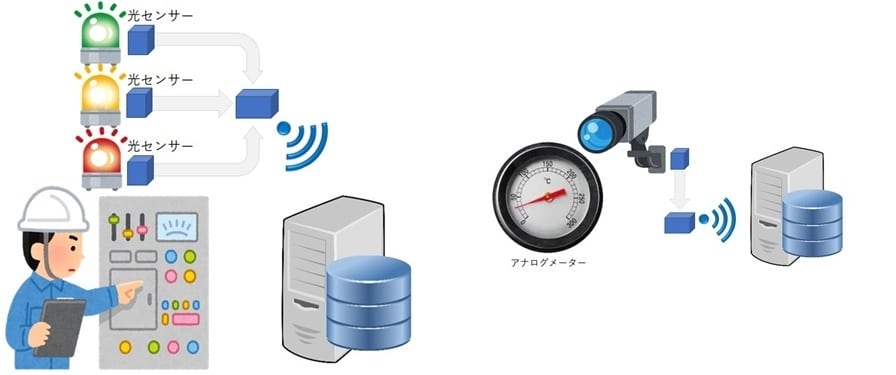
The left image shows an IoT system detecting patlight signal colors with optical sensors to convert machine uptime/downtime into numerical data. The right image shows an analog meter monitored by a camera, converting readings into numerical data.
The key is enabling a small-scale, affordable IoT rollout without replacing existing analog equipment with IoT-ready devices, bridging the gap until a full equipment upgrade becomes feasible. SIGNAL CHAIN Machine Operation Management IoT technology that accurately and automatically acquires the operating status of manufacturing equipment from various devices, enabling real-time monitoring of operating history from PCs and monitors. 続きを見る
Overall Equipment Effectiveness (OEE)
OEE (Overall Equipment Effectiveness) is a metric calculated from production management systems to measure machine uptime. It evaluates production efficiency across three dimensions: availability factor, performance factor, and yield.
- OEE = Availability factor × Performance factor × Yield
- Availability factor = Net operating time ÷ Gross operating time
The proportion of scheduled time that equipment is actually operating. - Performance factor = (Cycle time × Output) ÷ Net operating time
The ratio of actual production speed to the machine’s inherent capacity. - Yield = Good units ÷ Total production
The proportion of good units to total production.
In essence, OEE measures a machine’s contribution to production by assessing how consistently it runs (time), how well it performs relative to its capacity (speed), and how accurately it produces (yield).