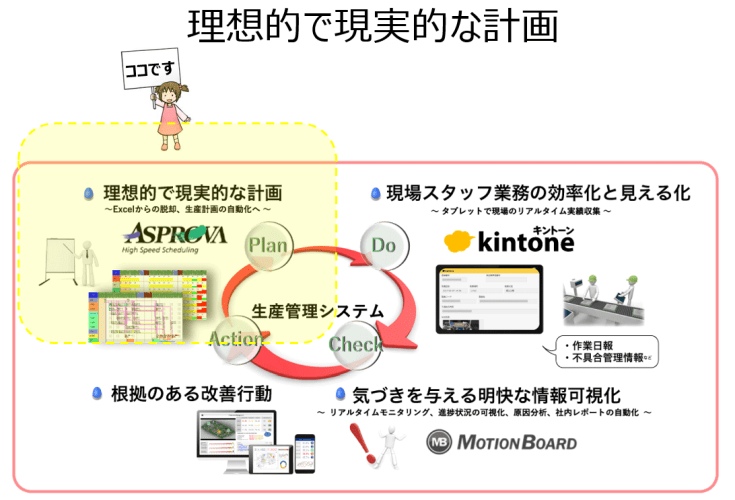
本日はシステムで生産計画を作成し、タブレットで製造実績を記録し、BIツールで予定と実績のデータを可視化するというPDCAを回すという設定での、最初のPlanの部分を担当させていただきます。
私のパートは主に製造業様に関係する内容ですが、この後にご説明されるサイボウズキントーンとウイングアークMotion Boardについては、特に製造業様限定というわけではなく、業務全般に応用できる内容かと思います。
今回は資料の配布なしになっておりますが、資料が必要な場合はアンケートの選択肢に「資料希望」をチェックしていただければ、後程メールにて配信させていただきます。
-
-
インドネシアの生産管理システム
インドネシアの市場環境は製品寿命の短命化による多品種少量生産、需要変動、人件費上昇、非日系企業との競争など益々厳しくなっており、生産管理システムの導入やIoTによる設備の稼働管理など、生産性向上によるコスト削減を目標としたDX化が推進されています。
続きを見る
会社紹介
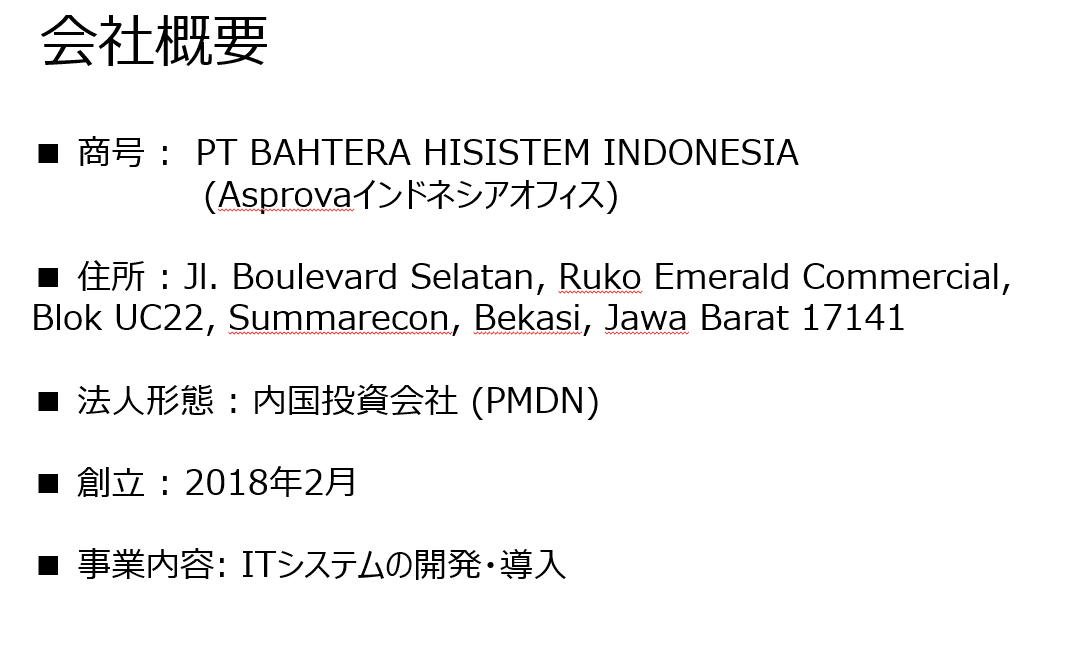 |
簡単に会社紹介をさせていただきます。弊社ですがバテラハイシステムと言いまして西ブカシのスマレコンにオフィスがあります。
設立したのはまだ去年なんですが、私自身はシステムの仕事を20年ほどやっております。 |
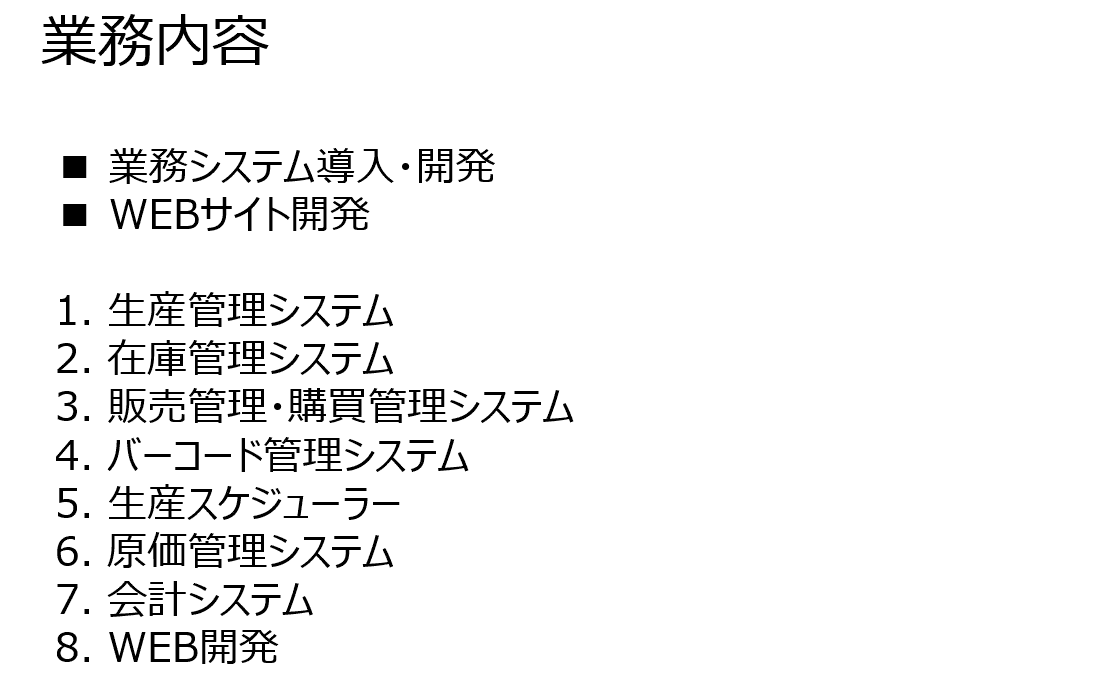 |
業務内容は主に製造業システム全般で、生産管理、在庫管理、販購買、生産計画、原価計算、会計などのシステム化を行っております。 |
近年のインドネシア日系製造業が直面する課題
それでは、さっそく本題に入りますが、まずは「見える化による全体最適化」が必要だと言われるインドネシアにおいて、日系製造業様がおかれている厳しい環境について、少し見ていきたいと思います。
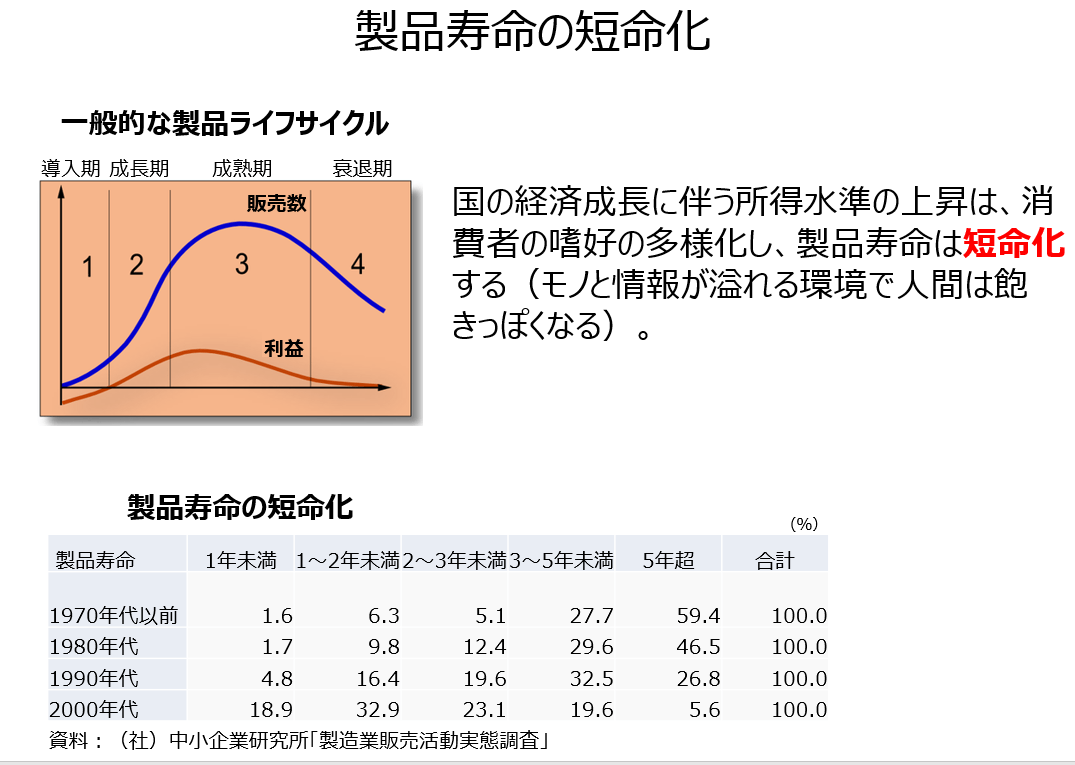 |
製品寿命の短命化は、インドネシアが経済成長して消費者の所得水準が上がってくれば、消費意欲も高まりますし好みが多様化して飽きっぽくなりますので必然的に起こる事象だと思います。
最近はインドネシアの方の給料が上がり、ショッピングモールのレストランに入って、隣のテーブルのインドネシア人家族が美味そうな料理をテーブル一杯に注文しているのを見ると、ああみんなお金持っているなあと感じることがよくあります。
マクロ経済的に見た場合、インドネシアの経済は「緩やかな成長」と言われることが多いのですが、これは国内の加工技術が低くて付加価値をつけて輸出することが出来ないので貿易赤字が続いています。
基本は国内資産の流出になるのですが、それを補って余りある消費者人口の増加が緩やかに成長の原動力になっていると思います。 |
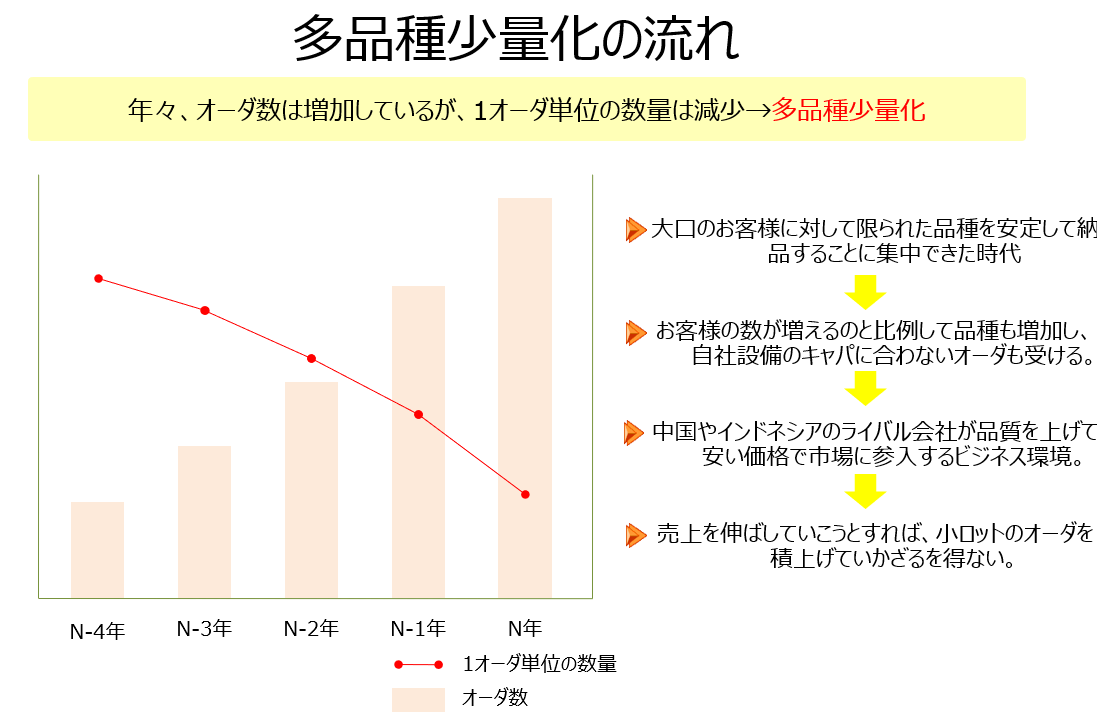 |
製品寿命の短命化は、製品を供給する側の製造業にとって多品種少量生産を要求されます。
10年前くらいまでは大口のお客様に大ロットの製品を納期に遅れないようにきちんと納品することが重要だった工場が多かったように思います。
ところが最近は売上に占める大口顧客の比率が下がっており、小ロットのオーダーを積み上げていなかいと、業績の維持が難しい状況になっています。
それは各社が現地調達率を上げる傾向にあり、中国やインドネシアの他国のライバル企業との競争が激しくなっていることが影響しているからかと思います。 |
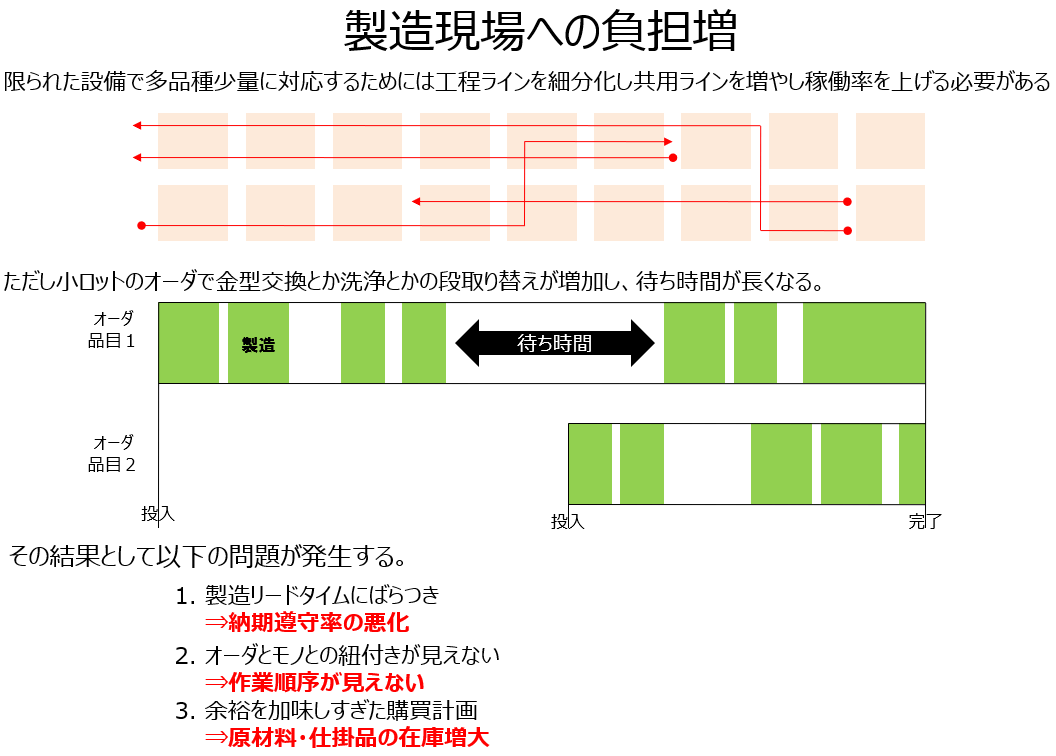 |
多品種少量生産に対応するとき、限られた生産設備の稼働率を上げるために、工程ラインを細分化して共用ラインを増やす必要があります。
ただ小ロット生産になればなるほど金型交換や洗浄などの段取り回数が増え、品目・数量・ラインの込み具合によって工程間の待ち時間が増えがちになります。
その結果、製品ごとの生産リードタイムにバラつきが出て納期遵守率が悪化し、工程間の紐付きが見えにくく作業順序が見えなくなり、材料や資材不足によるライン停止を防ぐため在庫過多の購買計画を作成しがちになります。 |
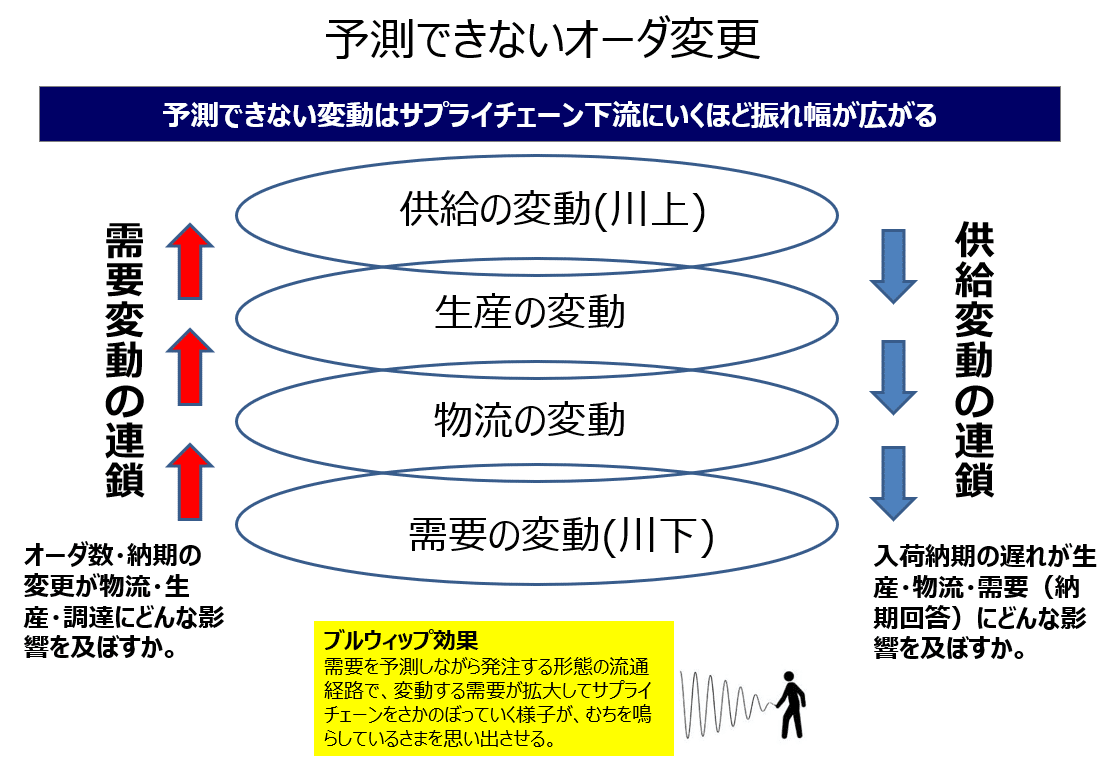 |
お客様が増えればいろんな要求が出てくるのは当然であり、無理なオーダー変更を要求してくる顧客もあれば、納期を守らない仕入先も出てきます。
サプライチェーンの中で原材料の供給側を川上、最終消費者に近いほうを川下と呼びますが、川下の需要変動はサプライチェーン上の川上へ、川上による供給変動は川下へ波及効果を持って流れていきます。
この流れの先に行けばいくほど波及効果が大きくなる現象を鞭のしなりに例えてブルウィップ効果といいます。 |
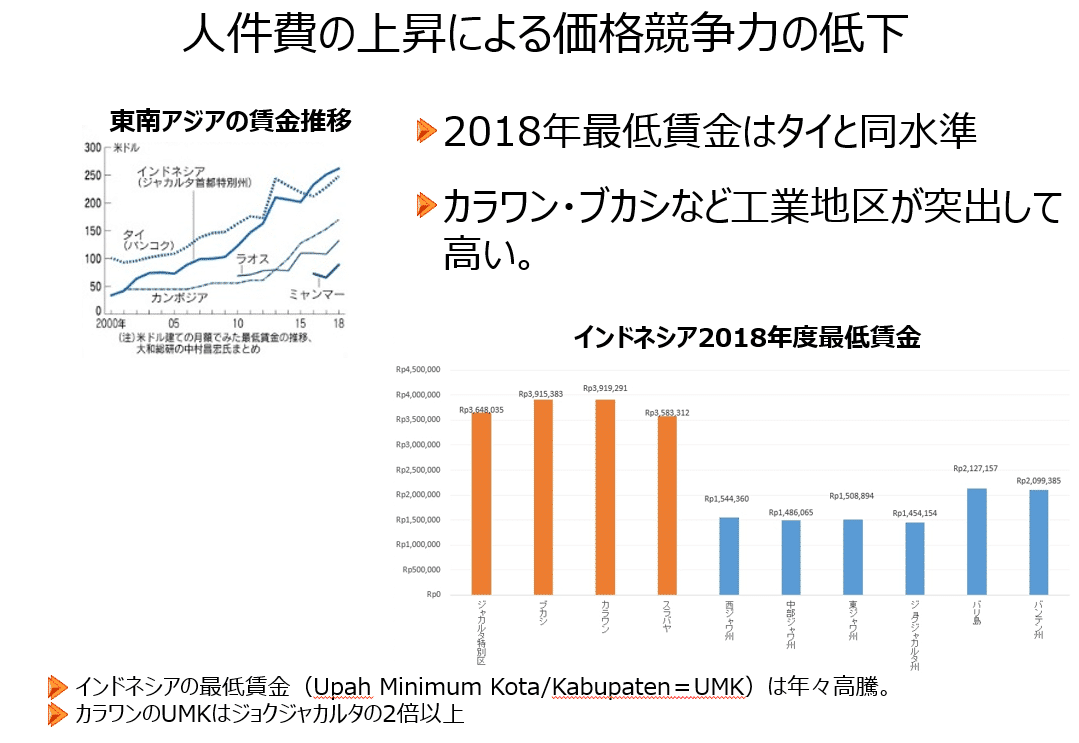 |
2014年のジョコウィ政権発足後に労働組合に対して過度な忖度により人件費が高騰し続けましたが、最近はインフレ率が5%以下に落ち着いているので、UMP(最低賃金)上げろというデモも減っている感じがします。
それでもここブカシ県の最低賃金はインドネシア最高レベルで中部ジャワの2倍近くになります。 |
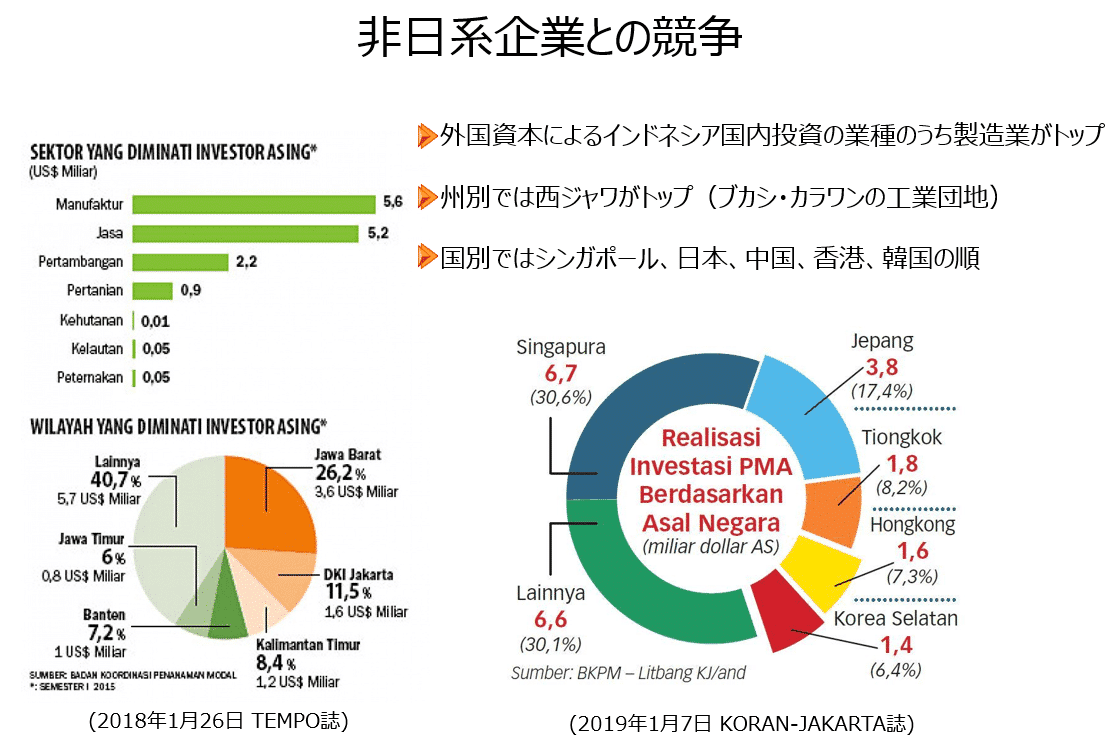 |
インドネシアの日系企業関連の雇用人口は700万人以上と言われており、国別投資額でもシンガポールについて2位です。
スハルト政権下での製造業のGDP寄与率は20%以上あったのが今は16%にまで落ち込んでおり、今年始まった第二期ジョコウィ政権ではこれを25%にまで引き上げることを目標にし、原材料に付加価値をつける川下産業の誘致を推進しています。 |
部分最適から全体最適へシフトし生産性向上
それではこのような厳しい現状を前にして、日系製造業様としてはどう対処していくかという話になりますが、ここでは部分最適から全体最適へのシフトによる生産性向上という視点から対応を考えたいと思います。
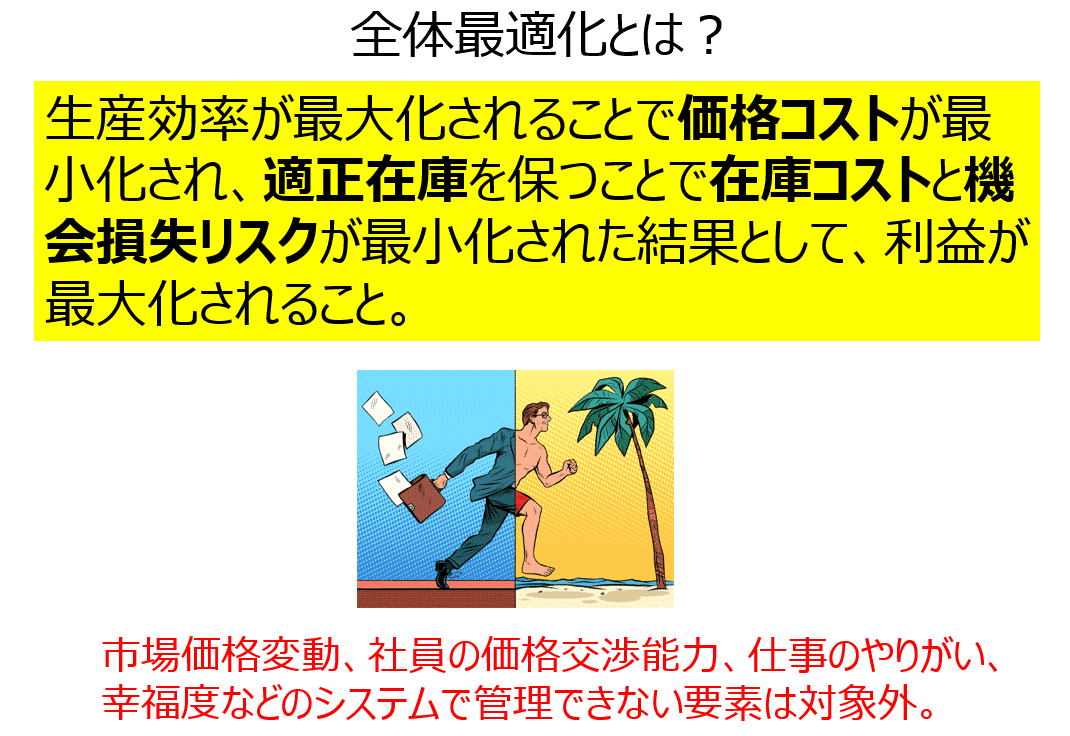 |
全体最適化の定義ですが、生産効率が最大化された結果、単位時間あたりの価格コストが下がり、在庫が削減されることにより在庫コストが最小化され、利益が最大化されることです。
ここでは市場価格の変動や価格交渉による値下げなどシステムで管理できない要素は除外します。 |
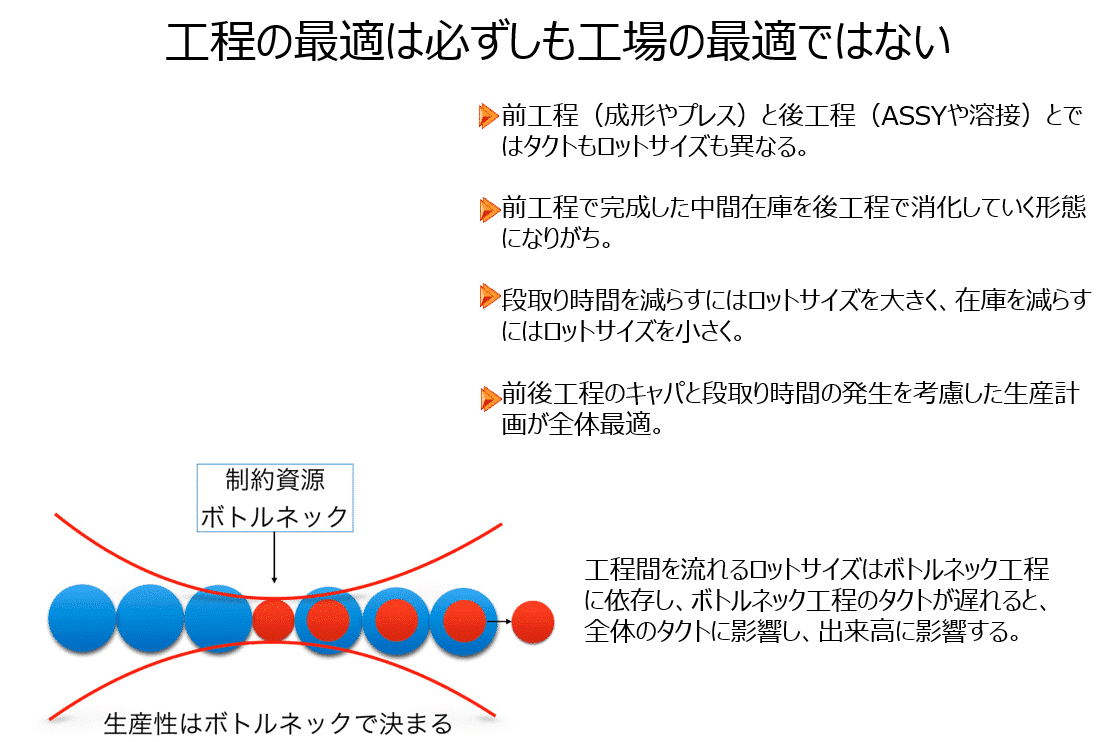 |
インドネシアの場合は前工程が成形またはプレス、後工程がASSYまたは溶接の場合が多いですが、前工程と後工程とではタクトが違うため、基本的には前工程で製造した中間在庫を後工程で消費していくという生産形態になります。
工場全体の生産能力はボトルネック工程の能力以上にはならないので、能力が高いからといってじゃんじゃん生産するよりも、前後工程はタクトを合わせることで、在庫滞留させない、待ち時間を増やさないように調整したほうが、滞留在庫が減り在庫コストが下がります。 |
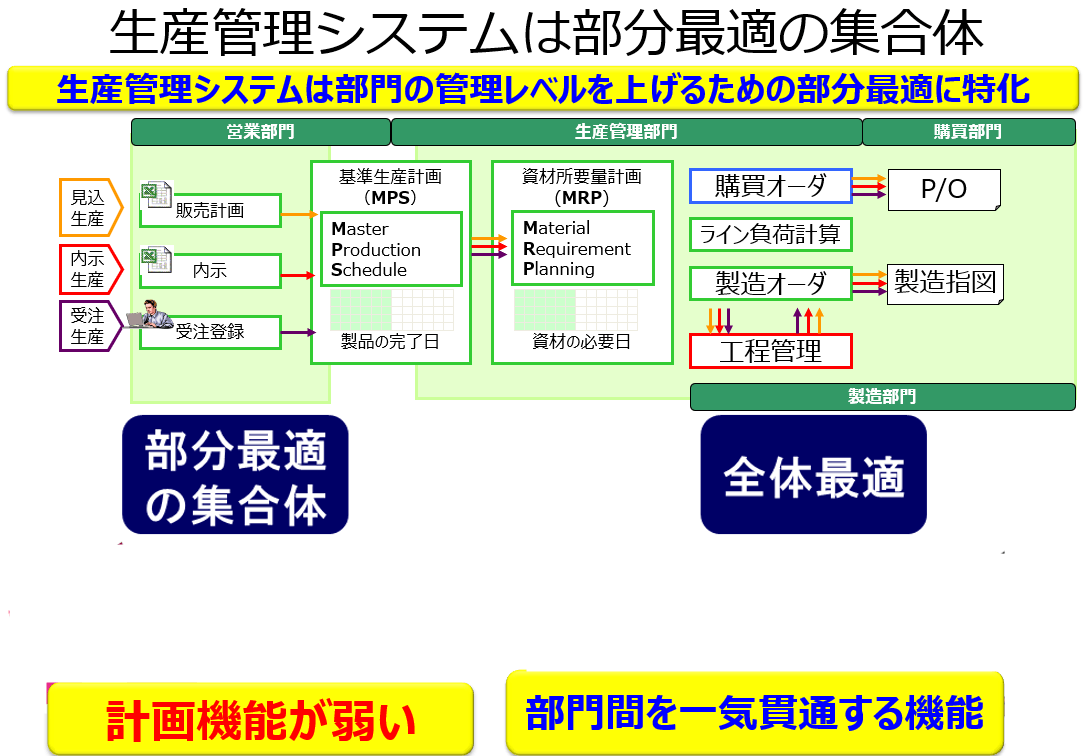 |
一般的な生産管理システムは部門の管理レベルを上げるための部門最適を前提として作られています。
部分最適の集合体である生産管理システムが、全体最適化が必要になる計画機能が弱いのは当然のことです。
全体最適のためには部門間の計画を一気通貫で作る機能が必要になります。 |
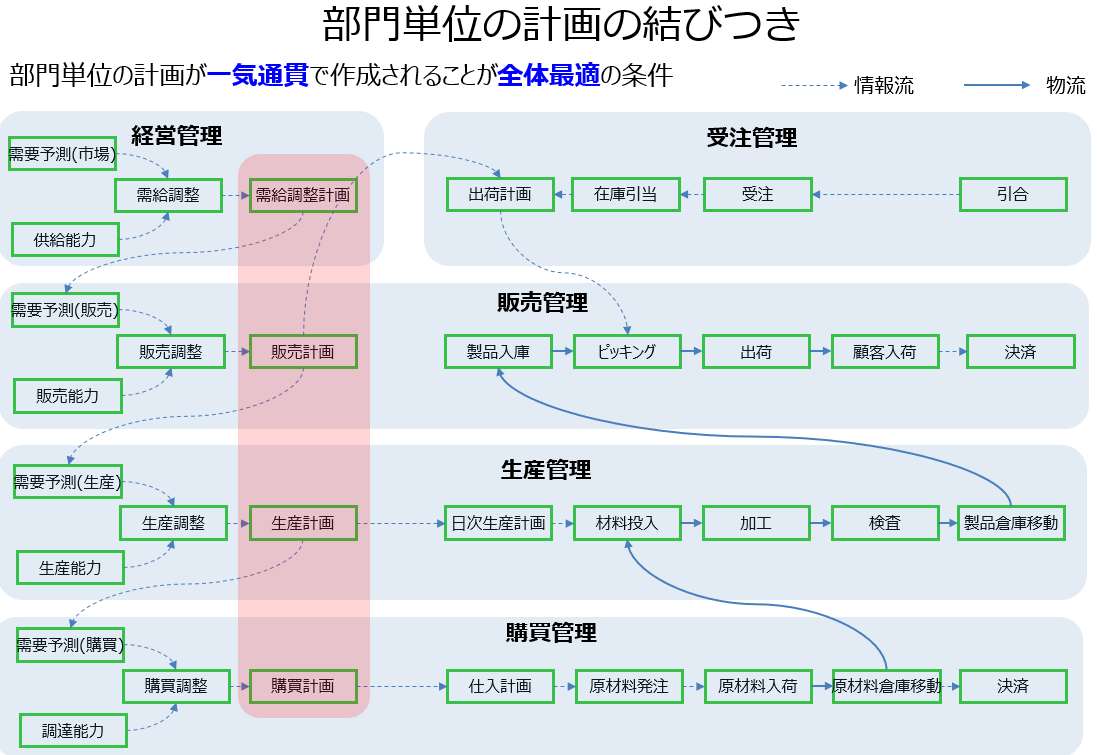 |
自社内には経営の下に販売、生産、購買といった部門がぶら下がっていますが、各部門ごとの需要と供給を元に計画が作成されます。
全体最適化にとって重要なのは、部門ごとの計画が一気通貫で作られることです。 |
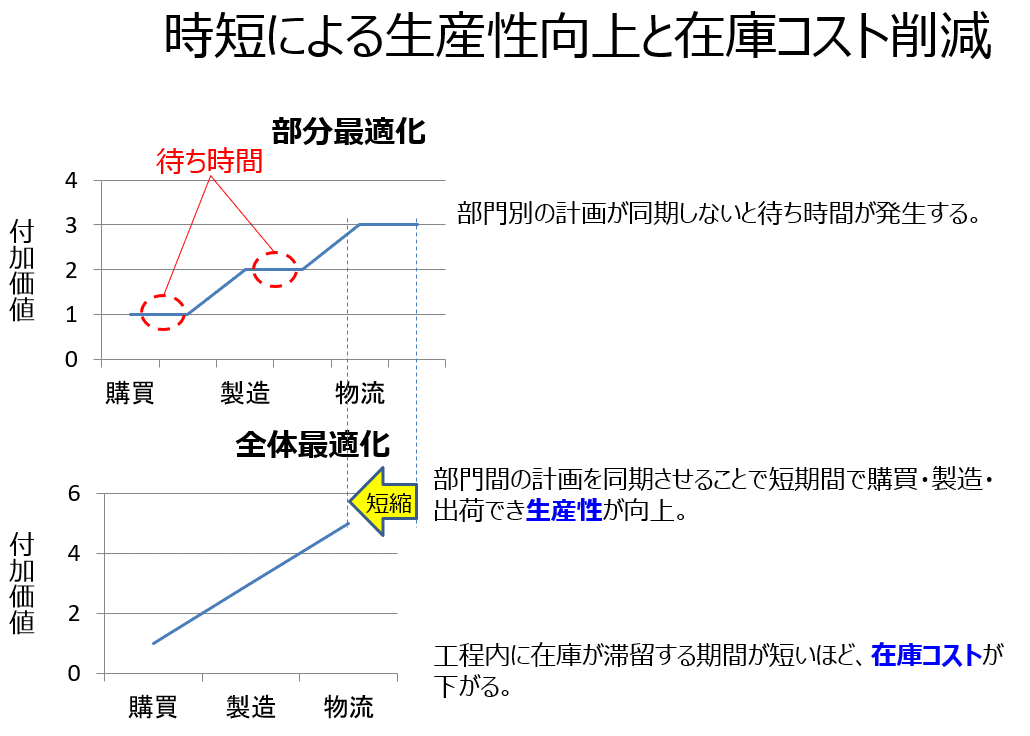 |
部門間での待ち時間のためにリードタイムが長くなると、倉庫に製品が滞留するしますので、出荷されて売上に変わるまで時間がかかることになり、その分だけ在庫コストがかかるということになります。
部門間で同期した計画に沿って業務が流れれば、社内に滞留する時間が短くなり、在庫コストが下がることになります。 |
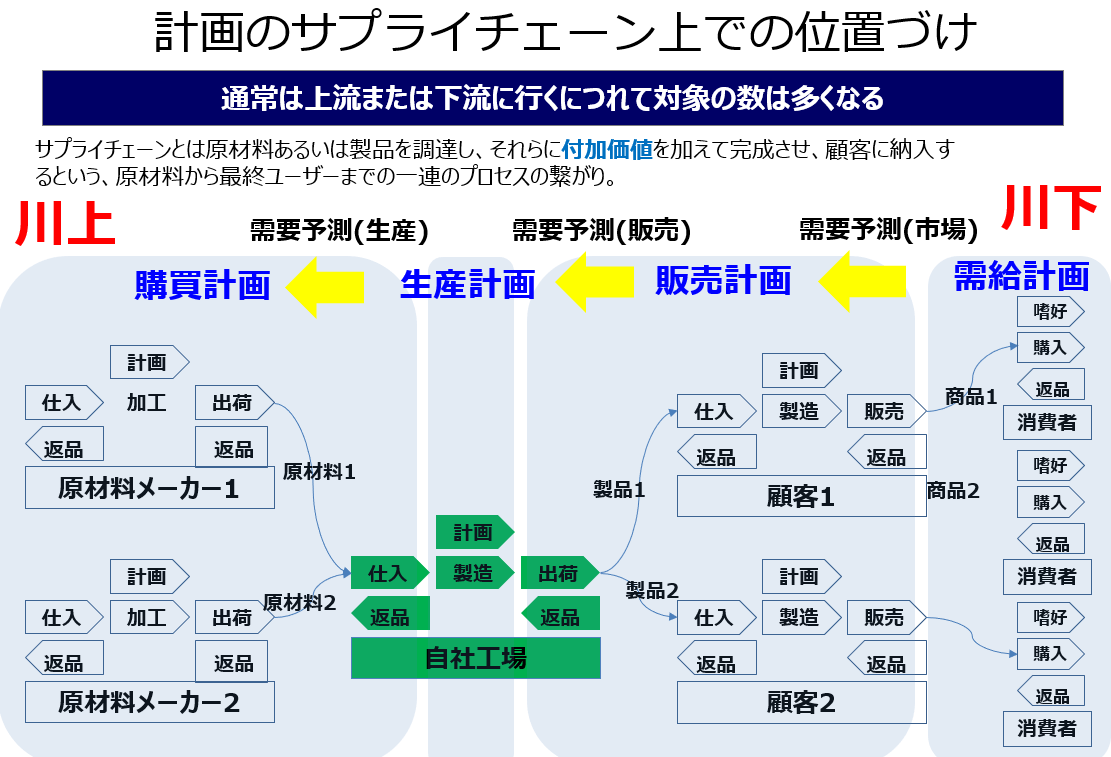 |
さきほどの計画は、サプライチェーンの中で自社工場を中心として、川上にある原材料メーカーから川下の最終消費者までが、どのように付加価値を付けながら商品や情報を流して経済活動を行うかの計画です。 |
在庫コストと機会損失リスク
このように全体最適のためには部門単位の計画が一気通貫で立たられる必要がありますが、これは在庫コストと機会損失リスクが下がり適正在庫を実現しようという考え方です。
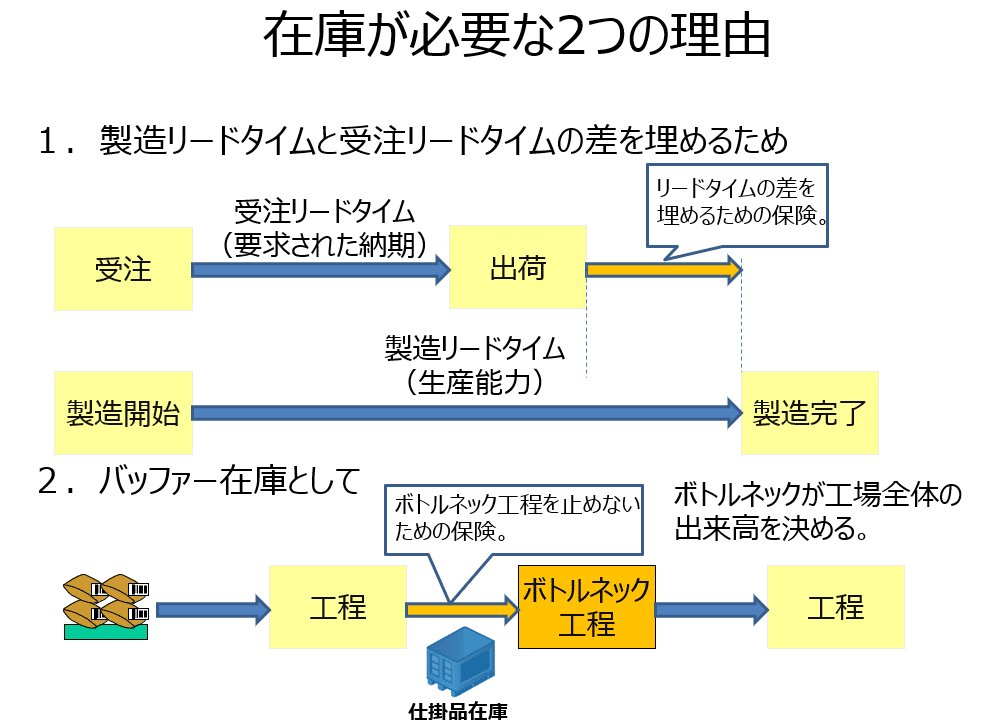 |
在庫には受注リードタイムと製造リードタイムの差を埋めるための保険、つまり製造に10日かかる製品を5日後に出荷できないので、そのための在庫という意味があります。
またボトルネック工程の稼働率を最大にするためのバッファという保険、つまり工場全体の生産性はボトルネックで決まりますので、ここを最大化するとための在庫という意味があります。 |
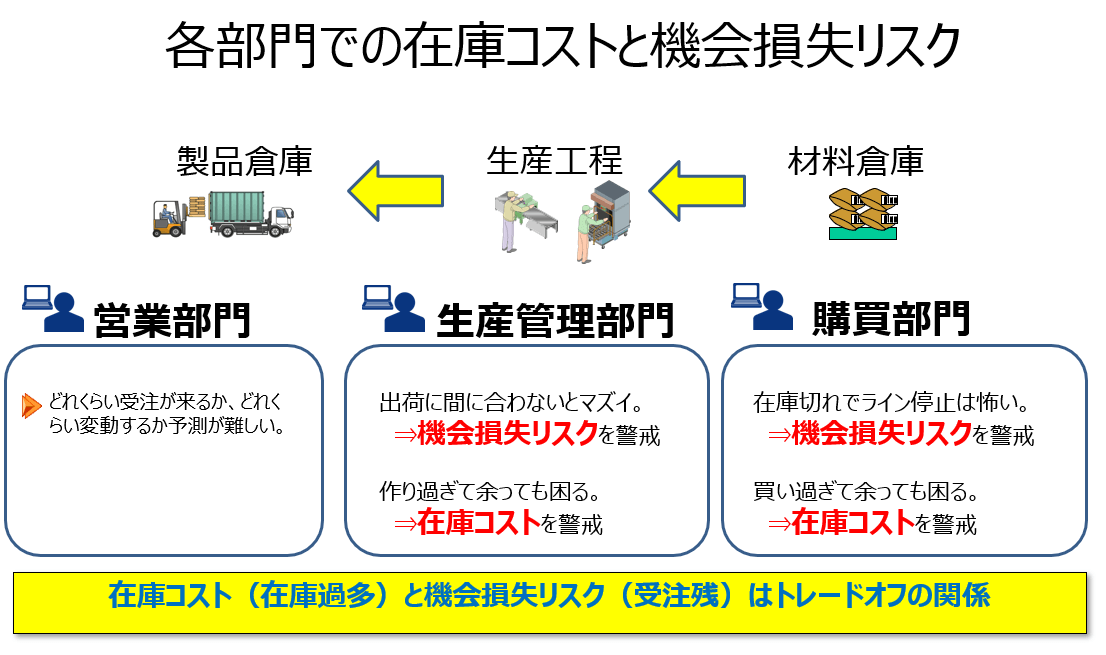 |
各部門担当者は在庫コストと機会損失リスクの考え方ながら業務を行っています。
在庫コストと機会損失リスク「あちらを立てればこちらが立たず」というトレードオフの関係がありまる。 |
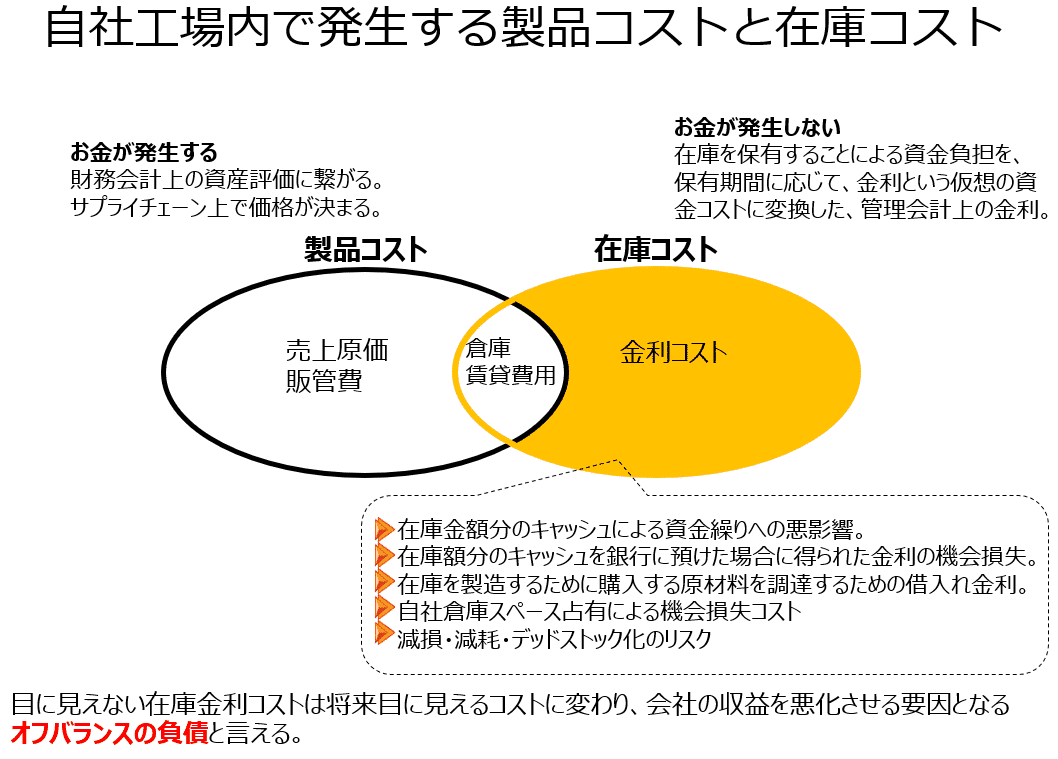 |
サプライチェーンの中で付けられる付加価値分のコストは会計上計上される製品コストですが、それ以外に社内に滞留する在庫のせいで発生する金利がオフバランスで発生します。
本来その在庫がキャッシュとして社内にあった場合にはどれだけの使い道があったか、どれだけの収益をもたらしたかという仮想の価値であり機会損失とも言えます。 |
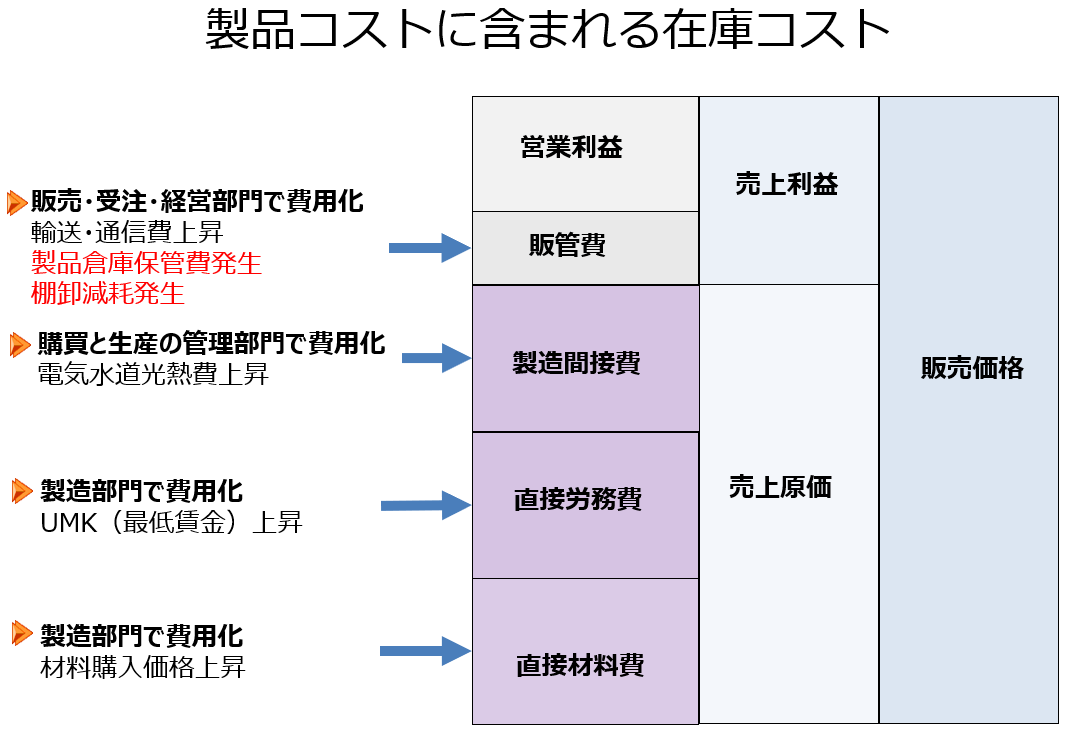 |
製品コストと言えるものは、製品自体の価値である製造原価(製造単価)分の価値をもつ製品が何個出荷されたかで決まる売上原価と、売るためにかかった費用である販売管理費が該当し、この2つを売上から差し引いたものが会計上の営業利益として計上されます。
会計上計上される販売管理費の一部である棚卸減耗や倉庫賃貸費用などは製品コストであると同時に、在庫があるせいで発生した金利とも言えます。 |
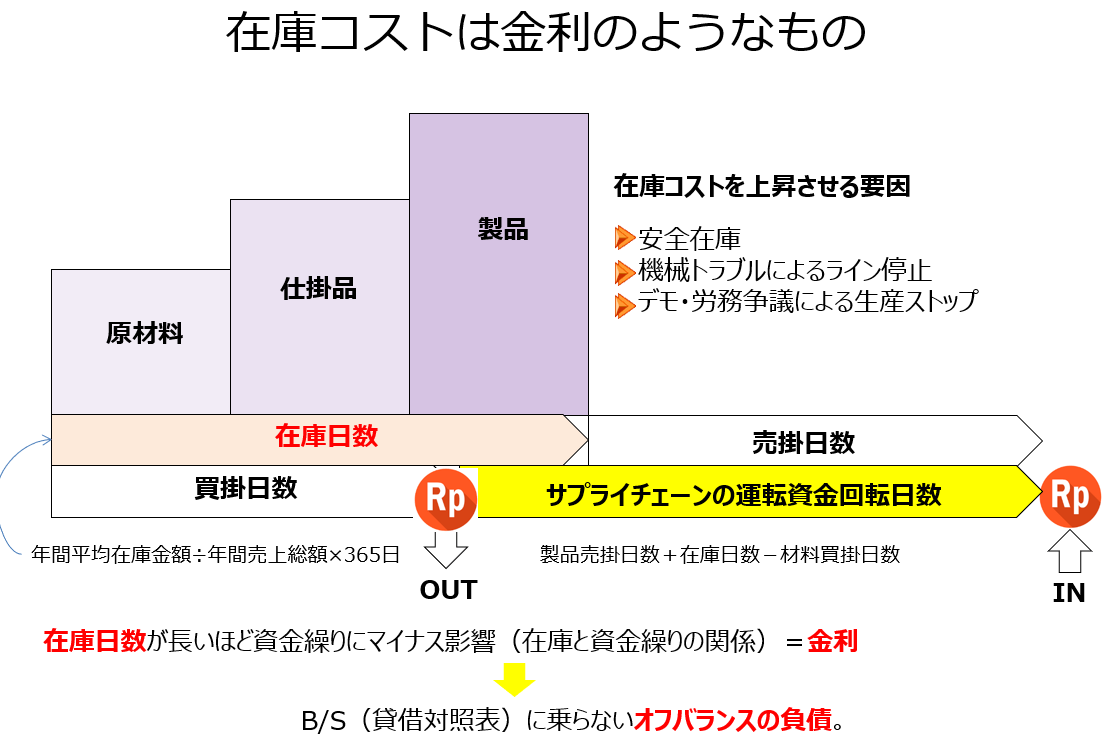 |
在庫があるせいで発生した金利を見積もるには、原材料、仕掛品、製品が社内に滞留している期間に、売掛金の回収までの期間を足したものから、原材料の買掛金の支払い猶予期間を差し引いたキャッシュフローベースの考え方をします。
この在庫コストはB/Sには反映されないオフバランスの負債と言えます。 |
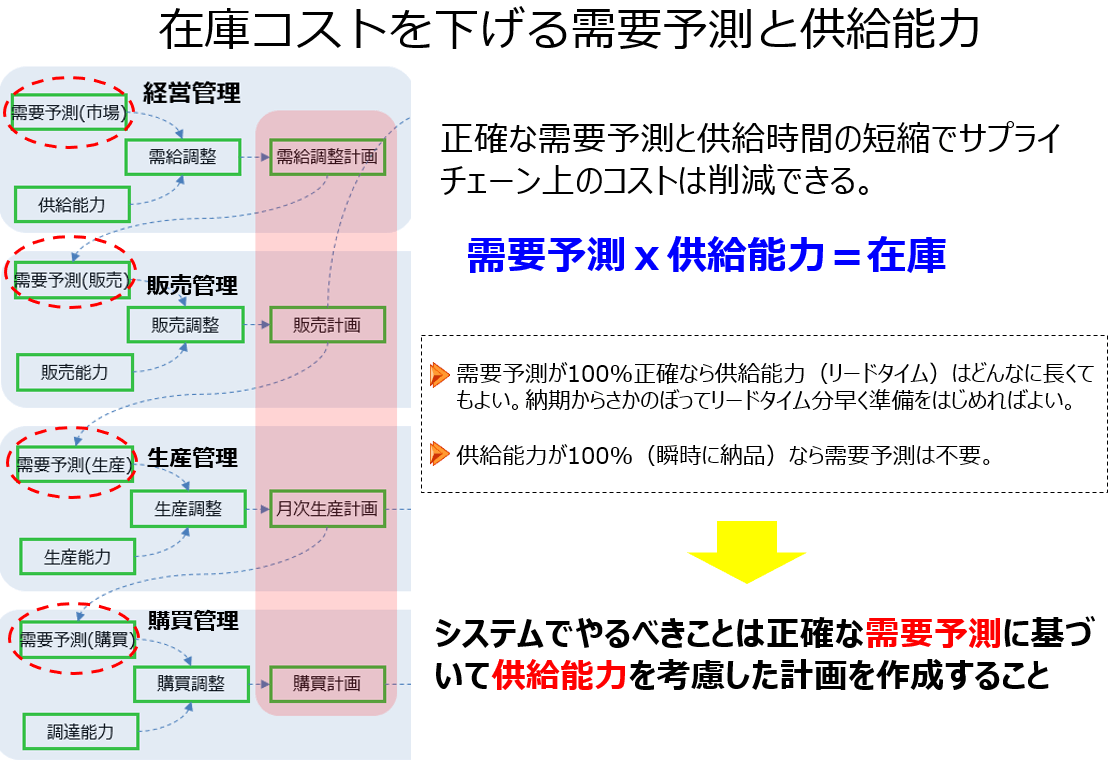 |
仮に在庫がゼロでも問題ないケースがあるとすれば、需要予測が100%正しく十分なリードタイムをもって生産できる場合か、または需要に対して瞬時に供給できる100%の供給能力がある場合のどちらかですから、在庫は需要予測の正確性と供給能力の高さで決定されます。
システムでやるべきことは正確な需要予測に基づいて供給能力を考慮した計画を作成することです。 |
全体最適化された計画を作成するシステム
それでは「見える化による全体最適化」を実現するシステム化の手順について説明させていただきます。
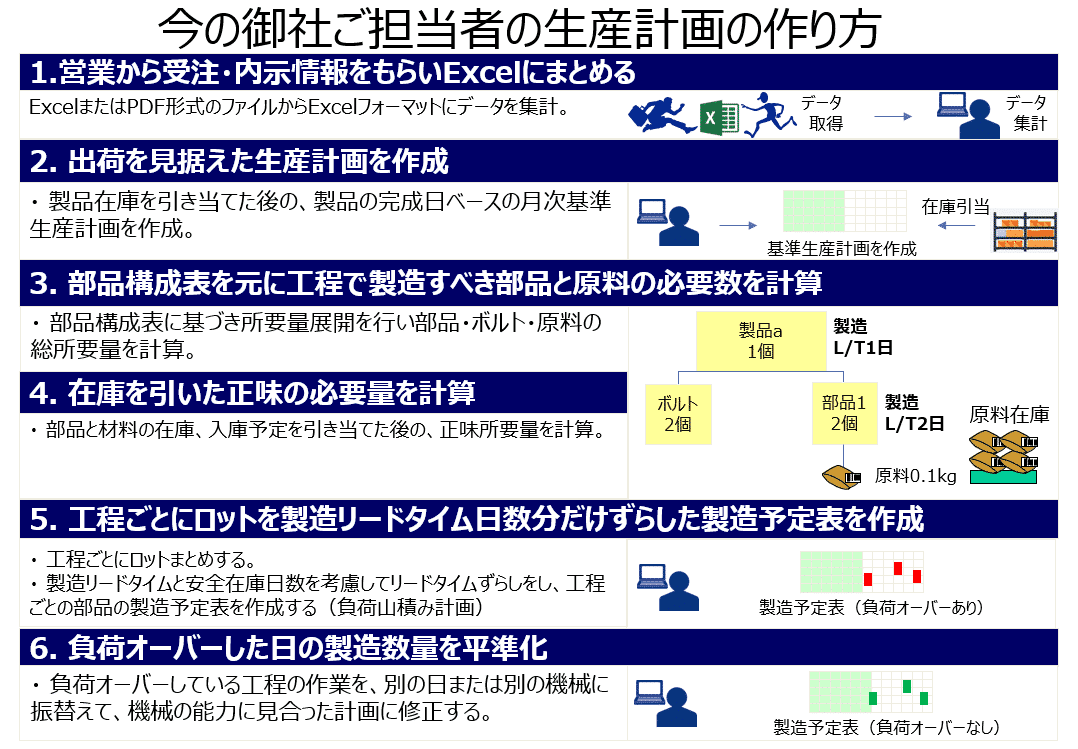 |
それでは生産性を最大化して価格コストを下げ、製造リードタイムを短縮して在庫コストを下げるためのシステムとはどういうものかについてご説明させていただきます。
工場のプランナーの方の生産計画の作り方はどこも同じで、営業から受注・内示情報をもらいExcelにまとめ、出荷を見据えた生産計画を作成し、部品構成表を元に工程で製造すべき部品と原料の必要数を計算し、在庫を引いた正味の必要量を計算し、工程ごとにロットを製造リードタイム日数分だけずらした製造予定表を作成し、負荷オーバーした日の製造数量を平準化するという流れです。 |
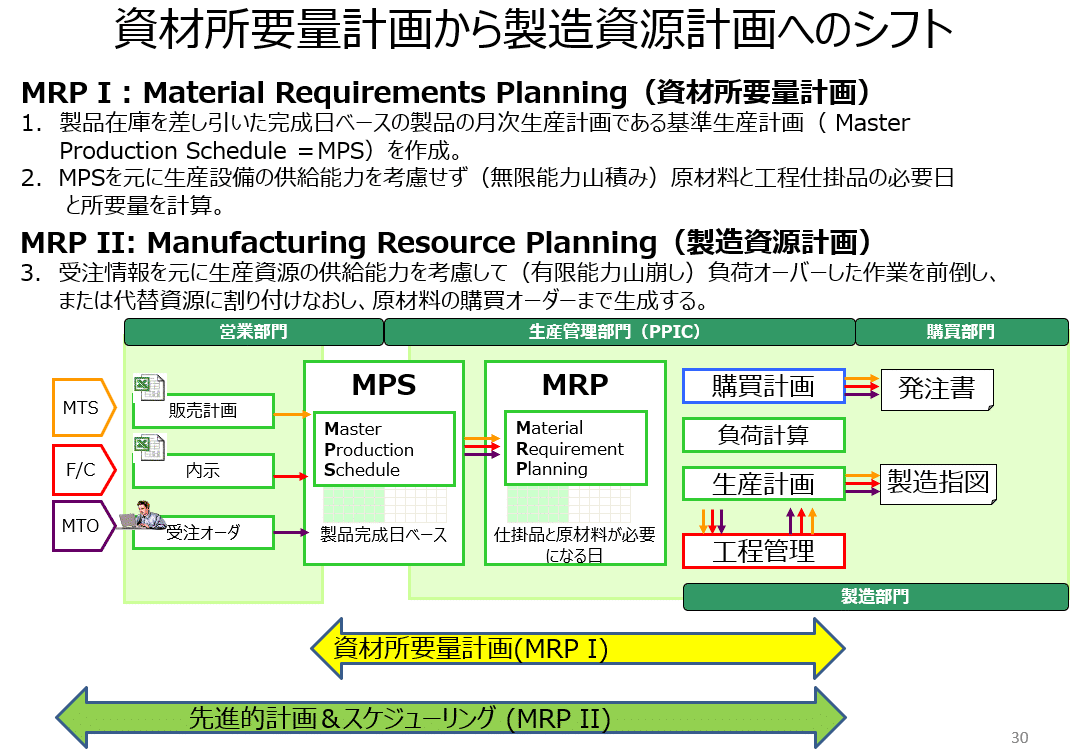 |
ここは少し生産管理の概念の話になるのですが、一般的な生産管理パッケージシステムでは、受注情報を元に資材所要量計画(MRP)という機能で所要量展開を行い、工程ごとの製造オーダーを作成し、原材料の発注量を計算します。
この場合、工程ごとの設備能力は考慮しない製造オーダーができるため、工程の能力を超えた部分を空いている日に振り分ける必要がありますが、製品点数や設備数が多くなると、マニュアルでできる作業ではありません。
工程の設備能力を考慮して、負荷オーバーの作業を空いている日や他の設備にシステムで自動的に割り付け、購買オーダーまで生成する機能を製造資源計画(MRPII)といいます。 |
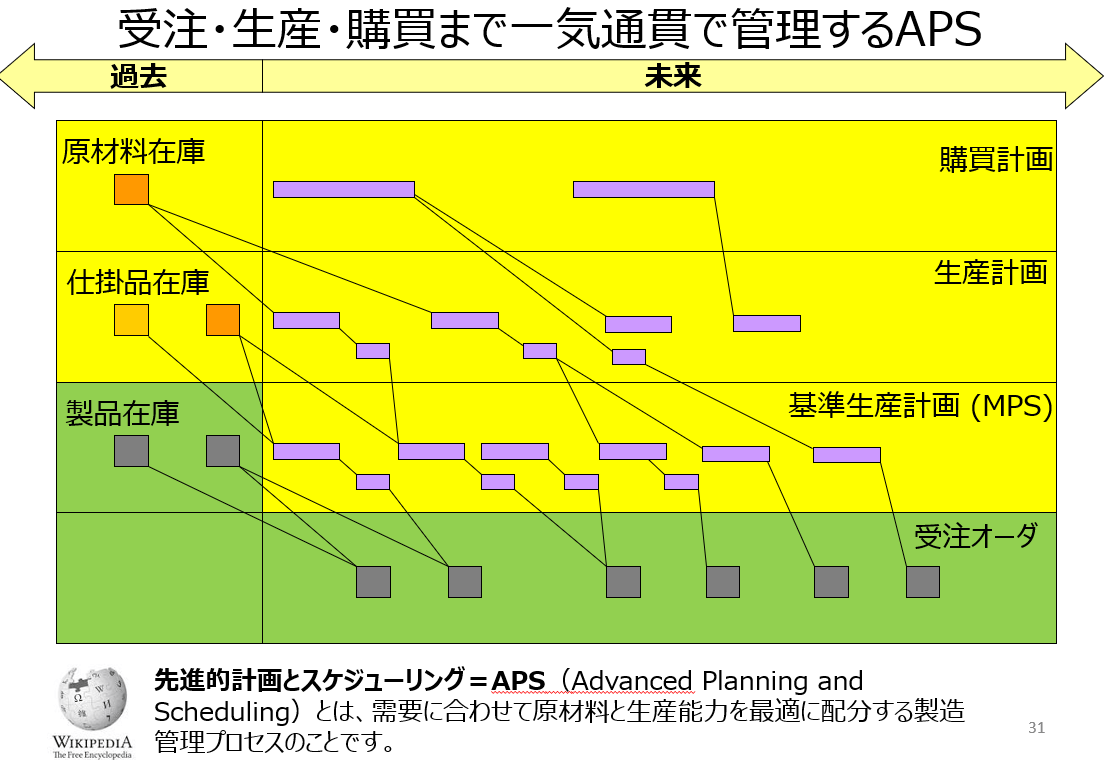 |
これが製造資源計画(MRPII)で受注から生産、購買まで一気通貫で管理されるイメージであり、リードタイム短縮による単位時間あたり生産性向上と在庫削減による在庫コストが削減されます。
全体最適化を図りながら生産計画を自動生成する機能はAPSと呼ばれています。
日本語だと「先進的計画とスケジューリング」になりますが、APSによって全体最適化された生産スケジュールが工程のの繋がりの中で見える化されます。 |
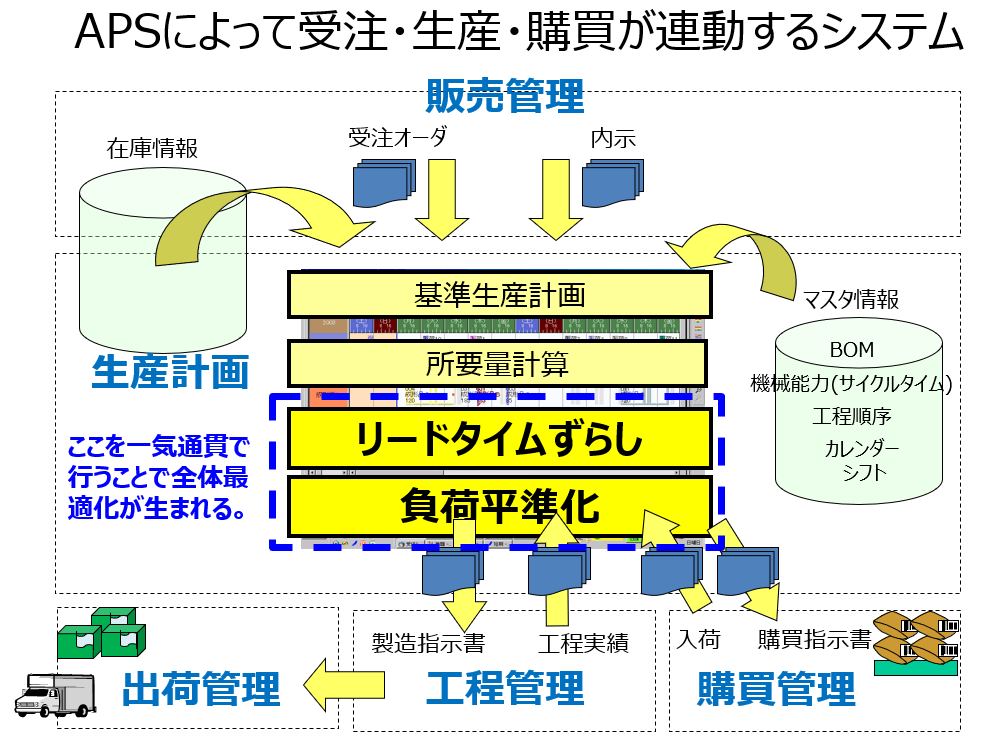 |
APSによって受注から生産・購買まで一気通貫で管理システムの動きですが、受注情報を取り込み、製品在庫を差し引いた製品正味所要量を元に所要量展開を行います。
同時に設備能力を超えないように負荷平準化しながら製造オーダーを設備に割り付け、製造開始日に間に合うタイミングで購買オーダーを発行します。
APSではこの一連の動作を一気に行います。 |
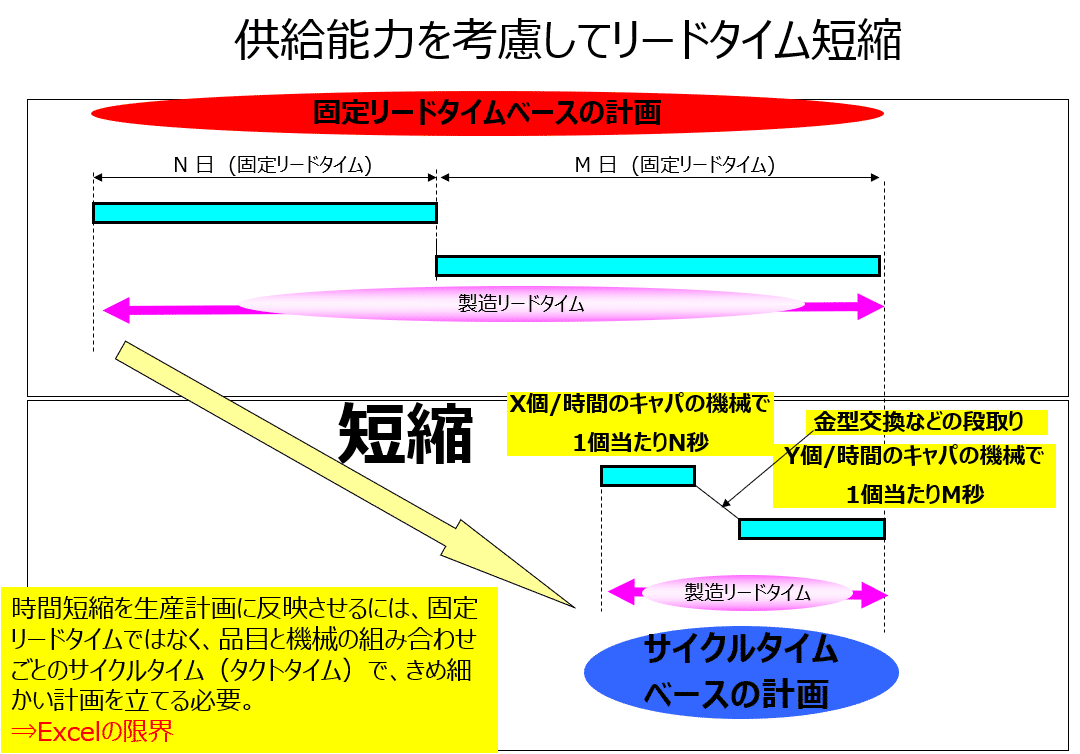 |
APSでは設備能力に対して生産管理システムのような固定リードタイムではなく、サイクルタイムを設定しますので、機械のキャパを考慮したサイクルタイムベースの生産計画が作成され、結果として製造リードタイムが短縮されます。
この場合、金型交換やタンクの洗浄などの段取り時間を設定し、同一品目を連続して製造することで段取替え回数を減らす計画を作ることもできます。
製造リードタイムが短縮されれば、単位時間あたりの生産性が上がりますので製品コストが削減されます。 |
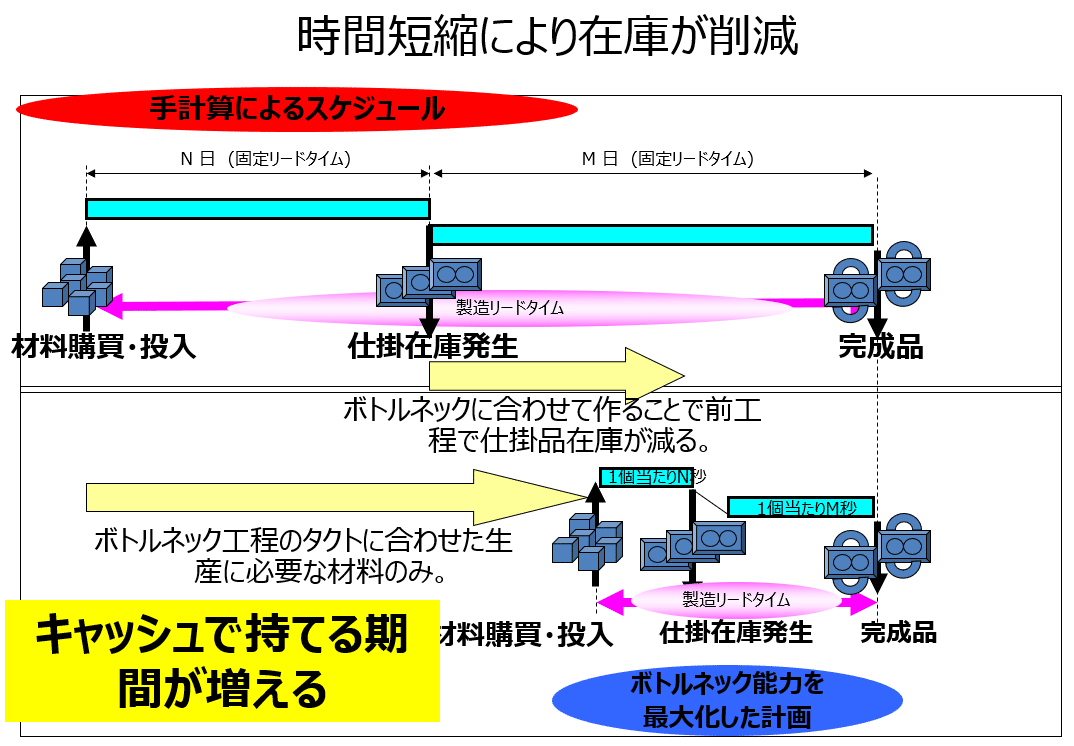 |
製造リードタイムが短縮されることにより自動的に工程内に滞留する在庫が削減され、在庫コストが削減されます。
結果的にキャッシュで持てる期間が長くなり、会社のキャッシュフローが改善されます。 |
生産スケジューラーの機能
最後に少し生産スケジューラーAsprovaのご紹介になります。
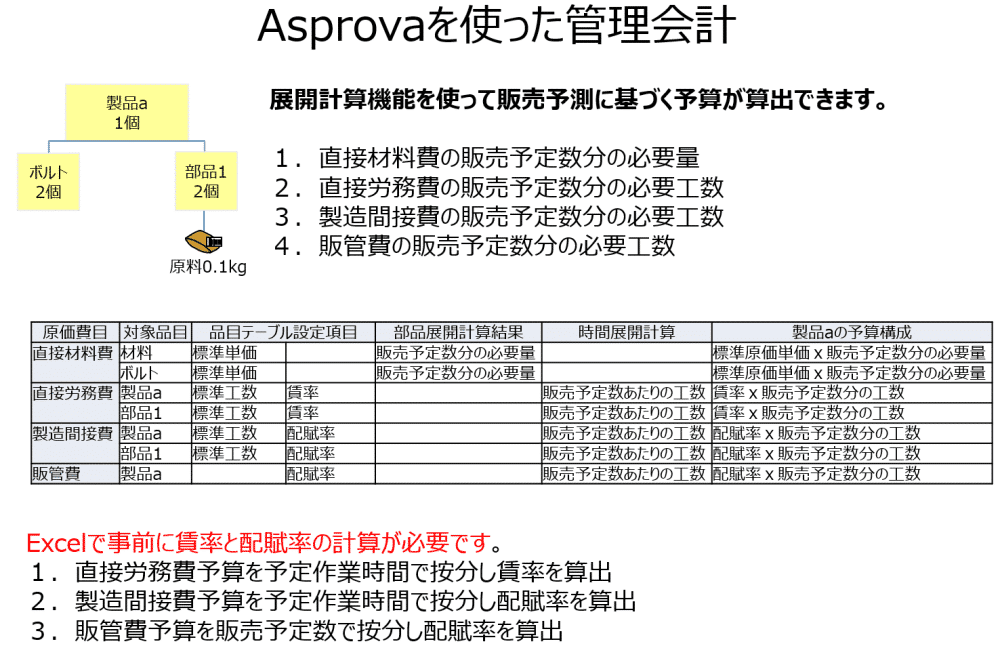 |
Asprovaでは展開計算ができますので、品目マスタに材料の標準単価、労務費の賃率と能率、製造間接費の配賦率を設定しておけば、製品の予定生産数量を元に来季の原価予算や売上予算が計算できます。 |
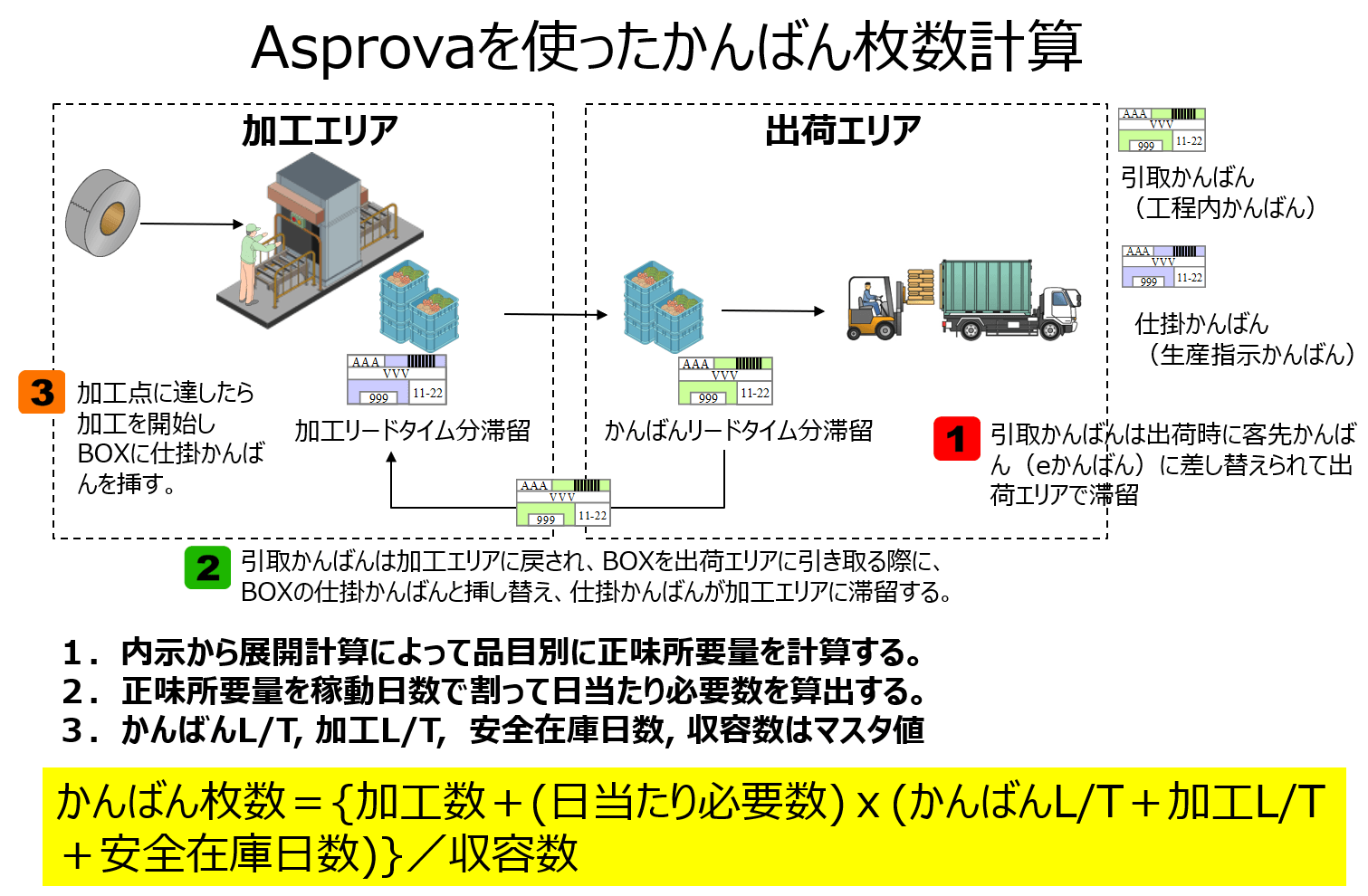 |
インドネシアでTIMMINさんやADMさんへ部品を納品されるところは、生産ラインもかんばんで流れることもあると思います。
内示を元にMRPで所要量計算するということは、内示をもとにかんばん枚数を計算するのと考え方は一緒ですので、Asprovaで毎月かんばん枚数を更新して、現場で流動するかんばんを増やしたり減らしたりするという運用も可能です。 |
本日は生産スケジューラーAsprovaに関わる話ですが、弊社の場合は「システム導入」というのをあまり大上段に構えず、Excelと同じように少しずつ改善しながら現場に浸透させていく、という方針で、基本はお客様のご予算に合わせて導入が可能です。