In Indonesian manufacturing, a picking list is created by grouping the item lot detail lines from a list of registered shipping instructions into shipping units at the time of shipment. It is used to verify whether the physical goods match the item lots registered at the time of order entry. Comprising shipping instruction numbers (header) and item lot numbers (details), shipping performance is recorded accordingly. Production Control System in Indonesia It’s not limited to Indonesia, but it’s often said that the ultimate goals of the manufacturing industry are twofold: "cost reduction through productivity improvement" and "delivering products on time without delays." From a management perspective, business plans are crafted to maximize growth based on market supply and demand adjustments. However, even if sales increase due to low pricing, it only reduces gross profit, leading to losses from selling and administrative expenses or non-operating costs. On the other hand, raising unit prices isn’t straightforward due to market price considerations. Therefore, process management based on production plans aimed at reducing costs through ... 続きを見る
Issuance Request Slips Issued at Material Release in Indonesian Factories
When a manufacturing client once requested “We only want to introduce an inventory management system,” I found that simply providing receipt and issuance functions wasn’t much different from their current Excel management. Therefore, we enabled the system to input issuance requests and issue slips.
In Indonesia, steel plates or bars are easily resold, and if manufacturing staff can freely take materials, the risk of theft increases. Clearly separating the responsibilities of the user and the issuer through slips helps reduce month-end inventory discrepancies.
Since warehouse staff aren’t present during night shifts, manufacturing staff submit issuance request slips by evening to have materials for the night shift released. This rule aims to prevent unauthorized material removal by manufacturing staff.
Moreover, by requiring the system to register the reason for issuance during input, it can be made versatile for various purposes, such as issuance instructions for manufacturing release, subcontractor release, shipping instructions, inter-warehouse transfer instructions, and disposal instructions.
Picking Lists for Physical Item Checks by Shipping Unit in Indonesian Factories
Among issuance tasks, releasing items for shipping is somewhat unique. Typically, items to be shipped that day are retrieved from the warehouse in bulk and stacked in the shipping area. A list consolidated by shipping work unit is checked against the physical items for verification.
In this case, within the sales management shipping function, shipping instructions linked to order information are entered, and the details of these instructions are grouped into sorting units to create a picking list.
For example, for multiple shipping instruction details destined for export to Japan today, a picking list number is assigned to products loaded into a single 40-foot container, creating a picking list. Products placed in the shipping area are scanned and verified, and if the verification is OK, shipping completion is registered.
The detail lines of a picking list for shipping include information from the issued shipping instruction list that remains unshipped, with key information as follows:
- Shipping Instruction NO ← Obtained from the system
- Item Code ← Obtained from the system
- Lot NO ← Obtained from the system
- Picking List NO ← Newly assigned to shipping instruction details for which shipping performance (completion) is to be recorded
Shipping instruction info statuses include unshipped, partially shipped, and fully shipped. Since shipping instruction NOs are scattered across details, they need to be regrouped under a picking list NO, requiring the picking list NO in the shipping instruction detail info.
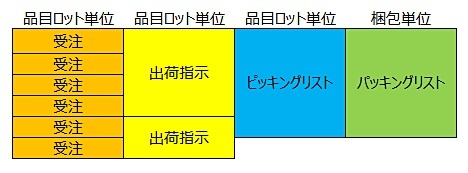
Picking List
If item lot info on physical labels is barcoded, importing the picking list into a handheld terminal and scanning the barcode on the physical label allows accurate sorting by verifying item lots. A Bill of Lading (B/L) issued by the shipping company to certify the acceptance of cargo based on the Invoice and Packing List The Bill of Lading (B/L) is issued by an Indonesian shipping company based on the Invoice, Packing List, and Certificate of Origin (COO) to certify the acceptance of cargo. In the case of exports, the B/L date becomes the sales recording date. 続きを見る
Detail lines from order registration to shipping instructions and picking-based shipping performance are recorded by item (lot) unit. However, when loading onto trucks or containers, multiple items are grouped into packaging units for damage prevention, and a packing list is submitted to the shipping company.
When sending a container from Indonesia to Japan, the shipping company issues a Bill of Lading upon receiving the Invoice, packing list, and Certificate of Origin (COO) from the shipper. The Japanese consignee, upon receiving the Bill of Lading from the Indonesian shipper, can retrieve the cargo after the Arrival Notice arrives.
When developing an issuance system with a handheld terminal, it’s crucial to note that while the picking list is used solely for accurate sorting, the shipping performance itself is recorded in the system by shipping instruction unit.