Using the Kanban method and the scheduler together
The Kanban system, which is the core of the Toyota Production System, is a system of operation at the manufacturing site to produce the orders received. Since only the "number of Kanban" (number of Kanban x number of units) required by the back-end process is produced by the own process, the flow rate of the Kanban can be fine-tuned to prevent overproduction in case of order cancellation.
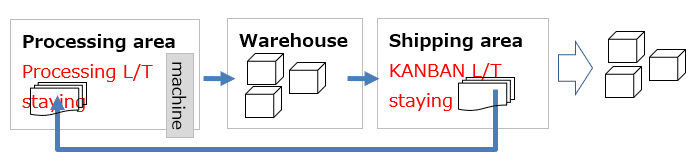
(1)Stuck in the shipping area due to misalignment ⇒ (2)Returned to the processing area and held in the processing area ⇒ (3)When the processing point is reached, processing begins and the box is inserted. ⇒ (4)Back to 2.
The Kanban system is based on the premise that the production capacity is sufficient to meet the order, so it is difficult for parts manufacturers who deliver to automobile manufacturers to operate the system because the demand fluctuates rapidly as the subcontractor hierarchy goes down to "Tier 2" and "Tier 3" rather than "Tier 1".
-
-
The Difference Between Planned Production Manufacturing Instructions and Kanban in Indonesian Manufacturing Industry
In production management systems implemented in Japanese manufacturing industries in Indonesia, manufacturing orders are generated from forecast information and confirmed orders using the MRP requirement planning function. However, at Toyota-affiliated auto parts manufacturers, they calculate the number of kanban cards and adjust the excess or shortage relative to the number of kanban cards circulating at the production site.
続きを見る
The Kanban method is an operation method in which a problem is stopped each time it occurs and kaizen activities are carried out through the "Five Whys" (repeating the "Why" five times reveals the cause of a problem that was not initially visible), and then corrected repeatedly in the next month.
The Kanban system is not a system to solve the overload of production resources in response to fluctuations in orders, so it is necessary to determine whether production is actually possible with a different system.
This is done by the production scheduler and the main bottleneck in the production process is the adjustment of the production process and to a certain extent the leveling of the production process to the facility unit and confirming that a feasible plan can be created the number of kanban sheets needed for the order quantity is calculated and the operation on site is handed over to the kanban.
System operation to be aware of MAX in-process inventory and raw material procurement
In Indonesia, the PSBB (Large-Scale Social Restriction) was enforced to prevent the spread of the new coronavirus, and both the purchase and production of automobiles have stagnated, resulting in a 79.6% decrease in Indonesian production in April 2020 compared to the same month last year (104,847 units to 21,434 units) and a 90.6% decrease in domestic sales (84,059 units to 7,871 units).
What we should be aware of in the economic stagnation phase is "prevention of overproduction" rather than "how much more we can produce", and one of the methods is to make a plan not to exceed the maximum inventory at the production planning stage and reliably digest the planned quantity on a daily basis.
It is difficult to systemize the work of making a production plan that does not exceed the maximum inventory, and even a slight delay in the plan can have a big impact on the subsequent process.
Because production delays can be caused not only by upstream factors such as additional orders and machine breakdowns, but also by downstream factors such as missing items due to delays in the arrival of raw materials, it is necessary to create a system to prevent shipping delays by allocating raw materials in the warehouse to high-priority orders that are confirmed or have already been delivered.