The concept of a smart factory embodies the realization of Industry 4.0 through the digital transformation (DX) of manufacturing. Specifically, it involves collecting and managing shop-floor-level data with MES (Manufacturing Execution System) to improve production efficiency and reduce manufacturing costs, while further advancing automation through MOM (Manufacturing Operations Management). Production Control System in Indonesia It’s not limited to Indonesia, but it’s often said that the ultimate goals of the manufacturing industry are twofold: "cost reduction through productivity improvement" and "delivering products on time without delays." From a management perspective, business plans are crafted to maximize growth based on market supply and demand adjustments. However, even if sales increase due to low pricing, it only reduces gross profit, leading to losses from selling and administrative expenses or non-operating costs. On the other hand, raising unit prices isn’t straightforward due to market price considerations. Therefore, process management based on production plans aimed at reducing costs through ... 続きを見る
Transition from ERP to MES and then to MOM
At "Manufacturing Indonesia 2019," Indonesia’s largest annual manufacturing exhibition held from December 4 to 7, 2019, at JIExpo Kemayoran, we exhibited a booth introducing the production scheduler Asprova. However, with the two- and four-wheeler industries in Indonesia experiencing a downturn, foot traffic seemed lower than in previous years. On the other hand, many visitors from Asian countries like Singapore and South Korea came to our booth for system sales related to IoT and factory automation.
A common theme in their discussions was the shift in manufacturing systems: from Enterprise Resource Planning (ERP), which divides business functions into production management, production planning, sales and procurement management, and inventory management, to Manufacturing Execution Systems (MES), which focus on managing people and machines at the shop-floor level. Going forward, the trend is moving toward Manufacturing Operations Management (MOM), which integrates and automates the entire production process—planning, scheduling, manufacturing management, labor management, and quality control—for unmanned operations.
In Indonesia, the term MES often carries the connotation of shop-floor terminals like PCs or tablets used to input production and labor performance data. When asked, “Is a production scheduler one of MES’s functions?” I initially answered “NO.” However, midway through, I realized that the modern definition of MES refers to a reorganization of traditional ERP system functions from a shop-floor perspective, so I switched my answer to “YES.”
A Singapore-based manufacturing IT vendor proposed a cutting-edge solution to realize a smart factory embodying Industry 4.0. They explained that, beyond IoT technology collecting real-time shop-floor data from PLCs (Programmable Logic Controllers) connected to manufacturing and inspection equipment for control management, simply setting a production plan could fully automate everything—from manufacturing to machine replacement in case of defects—ushering in unmanned operations. This made me keenly aware that we are in a transitional phase for manufacturing system trends.
If the purpose of systemization is labor savings, efficiency, and error prevention, then the recent buzzword DX (digital transformation) is not just about replacing existing systems but about operational reform—demonstrating “how much more convenient things can become with IT.”
Operational reform requires shop-floor operation reform, and creating a concept that leverages IT to achieve this is key to realizing business and profitability improvements—making it the profound significance of DX.
The smart factory concept, realized through manufacturing DX, is defined by reorganizing the terminology of traditional production management and execution systems, which makes its overview somewhat difficult to grasp.
As an aside, while “Smart Factory” is a term frequently seen on Japanese websites, I noticed that reactions to it were often lukewarm or puzzled. Later, I learned that it seems to be a Japan-specific term that doesn’t resonate with people outside Japan.
The New Definition of MES
According to MESA, the U.S.-based MES advocacy group, MES sits between the upper ERP layer and the lower PLC layer. It issues work instructions to operators (people) based on production schedules, monitors the real-time movement of raw materials and work-in-progress (things), and connects directly to production equipment (machines) to track operational status and anomalies.
- ERP: Management by process or department ⇒ Accurate information management (movement of things)
- MES: Management by machine or task ⇒ Improved production efficiency and reduced manufacturing costs (labor hours, machine status)
- MOM: Automation of MES
In simple terms, the difference between ERP and MES lies in the unit of management. MES collects and manages shop-floor-level data to achieve manufacturing’s ultimate goals—improved production efficiency and cost reduction—while MOM advances digitalization and automation to create a smart factory.
MES is defined as having 11 functions, as outlined below. Among these, task scheduling, production resource allocation and monitoring, and dispatching production units are areas where traditional production schedulers excel. The remaining items represent a reorganization of ERP-managed information at a more operational, shop-floor level.
- Operations/Detail Sequencing
- Resource allocation and status
- Dispatching production unit
- Performance analysis
- Maintenance management
- Process management
- Quality management
- Data collection/acquisition
- Production tracking and genealogy
- Labor management
- Document control
The evolution of MES and MOM is ultimately about advancing information management techniques, and it must connect to manufacturing’s core mission: “delivering quality products on time.”
The smart factory transformation through DX is positioned as a key national strategy to increase national wealth by boosting export competitiveness. Indeed, emerging countries worldwide are redefining Industry 4.0 to suit their contexts, aiming to enhance manufacturing’s value-add and international competitiveness.
The Abundance of Japanese-Speaking Indonesians
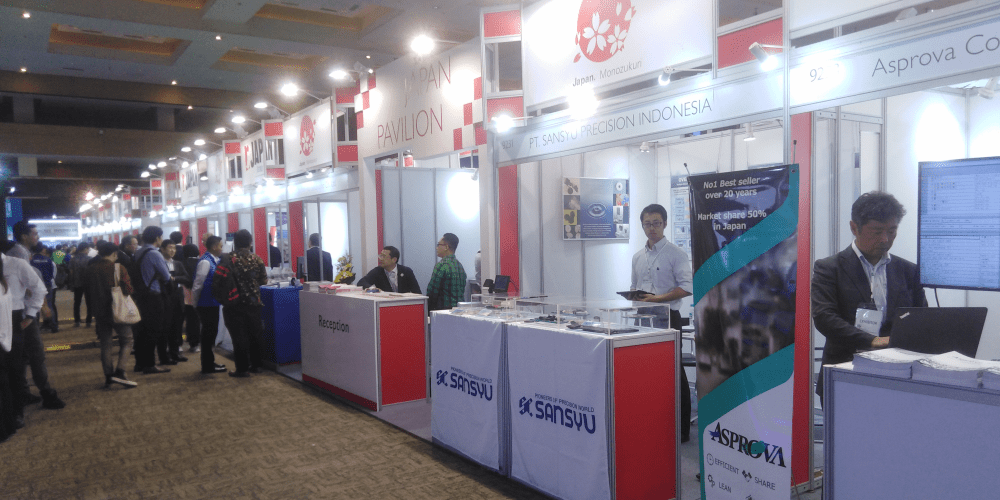
While globalization has brought changes, many Japanese companies in Indonesia still adhere to business practices rooted in trust-based past performance or operate in a “Japanese-only” environment—somewhat of a Galápagos phenomenon. For Indonesians, this creates a unique market where speaking Japanese offers a chance to seize opportunities.
Indonesians who visited our booth and spoke fluent Japanese cheerfully shared stories like “I lived in Osaka for three years” or “I was in Hamamatsu as a technical intern.” However, with recent attention on the dark side of Japan’s Technical Intern Training Program—such as harsh working conditions and unpaid wages—I hesitated to ask, “Did you enjoy life in Japan?”
Fortunately, all the Indonesians I spoke with in Japanese shared only fond memories of Japan. Still, a new issue has emerged: resilient Indonesians who honed their Japanese skills as interns and stayed in Japan to work as city tour guides or interpreters have caused a price crash in the inbound tourism business.
Making Indonesia 4.0: A Concrete Initiative for Industry 4.0
Industry 4.0 is a global movement to spark the Fourth Industrial Revolution using IT. It involves transferring software-centric IT implementations to hardware, connecting hardware to networks for faster, more accurate data collection and analysis, and linking this to productivity and quality improvements.
In Indonesia’s case, with a goal of joining the world’s top 10 economies by 2030, the Ministry of Industry announced Making Indonesia 4.0 in April 2018, outlining 10 national priority initiatives for Industry 4.0.
- Improving raw material flows:
- Creating added value through domestic processing
- Increasing local procurement rates for raw materials by domestic companies
- Redesigning industrial parks:
- Northern Java automotive industry belt plan along the extended highway to East Java
- Developing Patimban Port in Subang, West Java (scheduled for 2023) to decongest Tanjung Priok Port
- Establishing sustainability standards:
- Revitalizing SMEs:
- Developing and strengthening national digital infrastructure:
- Attracting foreign investment:
- Enhancing industrial workforce skills:
- Ecosystem support:
- R&D (research and development) by government, private sector, and universities
- Applying incentives for technology development investment:
- Easing policies, regulations, and systems:
In the 2000s, Indonesia’s manufacturing sector struggled to shift to technology-intensive industries, and its GDP contribution dropped from 20% under the Suharto regime to 16%. Through Making Indonesia 4.0, the goal is to revitalize manufacturing, raising its share to 25% by 2030 and boosting economic growth from the current 5% to 6–7%.
How Paperless and IoT Adoption Changes Business System Implementation
The first step is paperless adoption—converting 3D information into 2D without physical intermediaries. This includes EDI (Electronic Data Interchange) for POs and invoices, and collecting production performance data via tablet input or automatic recording from sequencers.
Two types of errors can occur before information is digitized onto a network:
- Transcription errors when entering paper-based information into a system ⇒ Paperless adoption
- Input errors into the system ⇒ IoT adoption
The first, paperless adoption, is a fully achievable challenge as part of operational improvement with sufficient investment, completely eliminating transcription errors. However, eliminating the second—system input errors—requires advancing IoT in manufacturing lines to remove human data entry entirely.
From a business system perspective, the most impactful concrete improvements under Industry 4.0 are paperless and IoT adoption, which will also transform the nature of business system implementation work.
- How to access and integrate information:
With IoT, information needed for operational improvements is collected quickly and accurately, requiring development of system interfaces to gather and centralize this data. - Shifting from "how to collect information quickly and accurately" to "how to analyze and present it":
When production performance is collected automatically in real time and inventory is tracked instantly and accurately with RFID tags (Radio Frequency Identifiers), timely and accurate data becomes a given on the system. This necessitates systems for visualizing, sharing, and structuring data to effectively drive operational improvements.
To achieve higher value-add and international competitiveness in Indonesia’s manufacturing sector through Making Indonesia 4.0, performance improvements in reliability, flexibility, and responsiveness are needed not just within a company’s factory but across the entire supply chain.
This demands system integration among companies conducting economic activities along the supply chain. As a result, internal business systems will increasingly be designed and implemented with upstream suppliers and downstream customers in mind.