Purpose of cost management system implementation
In the P/L (profit and loss statement) of financial accounting, profit is calculated in the order of gross profit (sales minus cost of sales), operating profit (selling, general and administrative expenses), ordinary profit (non-operating expenses), and net income (extraordinary losses).
In order to show gross profit on P/L, it is necessary to calculate cost of sales, and in order to calculate cost of sales, it is necessary to calculate cost of production, and in order to calculate cost of production, it is necessary to calculate material costs incurred in the current month.
- Gross profit = Sales - Cost of sales
- Cost of sales = product inventory at the beginning of the month + manufacturing cost - product inventory at the end of the month
- Manufacturing cost = Inventory of work-in-progress at the beginning of the month + Material cost of the month - Inventory of work-in-progress at the end of the month
- Current month's material cost = the amount of material in stock at the beginning of the month + current month's material purchase cost - the amount of material in stock at the end of the month
In order to realize this demand of financial accounting, it is necessary to calculate the evaluation unit price of material, work in process, and product inventory quantity at the end of the month, but if it is difficult to calculate with Excel, you should consider introducing a cost control system.
Variable and fixed costs
Cost of sales is the cost of the product shipped (sold) from the product warehouse in the current month.
The manufacturing cost is the cost of the products produced in the current month and can be rephrased as the cost of the products that entered the warehouse in the current month.
The cost of material incurred is the cost of materials delivered from the material warehouse in the current month and can be rephrased as the cost of materials put into the production process in the current month.
Once the material is put into the manufacturing process and the processing cost is accumulated, it is collectively called a work in progress (first work in progress + second work in progress + third work in progress) because it is "larger than the material and less than the product".
The production cost of in-process goods in progress is the cost of goods in progress that have been produced in the current month's own process, and are put into the next process and become the cost of goods in progress on an input quantity basis, which further adds up to processing costs.
Manufacturing costs consist of variable costs and fixed costs (processing costs), and the only variable costs that can be calculated from the production management system are direct material costs and subcontract processing costs.
Inventories at the beginning of the month, purchase performance, input performance, and production performance are required for the calculation of variable costs based on the gross average unit price, while processing costs (direct labor and manufacturing overhead) are obtained from the accounting system.
The unit of aggregation changes from an account to an item on the boundary of primary allocation.
The primary allocation approach is easy to understand for the depreciation of shared machinery, such as boilers and coolers.
In the case of manufacturing overhead, the total working hours of each product group, which is a cost center, are allocated proportionally as the primary allocation ratio, and the wage rate (how much per minute) divided by the working hours of each product group is calculated and multiplied by the number of man-hours (efficiency).
- Calculate the primary allocation ratio from quantity and time.
- The number of scheduled production or actual production results obtained as a result of developing the required quantity based on the production plan is aggregated by product group or line, incorporated under the allocation ratio code, and used as the primary allocation ratio on a quantity basis.
- Scheduled direct work hours or actual direct work hours multiplied by standard manpower (efficiency) to the number of scheduled production are aggregated by product group or line, incorporated under the allocation ratio code, and used as the primary allocation ratio on a time basis.
- The actual or budgeted fixed costs are prorated by the primary allocation ratio to aggregate the fixed costs by product group or line.
- Calculate the allocation ratio (how much per minute) by item (direct labor, depreciation, expenses, etc.) by dividing the fixed costs by item or line by the actual or scheduled time. In the case of production volume allocation, the allocation rate is the unit price per unit by cost category, so there is no need to add man-hours.
- The actual unit price (standard unit price) for each item by expense category is calculated by multiplying the actual work time or standard man-hour (efficiency) per item by the allocation ratio, and the actual unit price (standard unit price) per item is calculated by accumulation calculation.
The difference between the allocation rate and the concept of man-hours in standard cost and actual cost
The basic idea of the allocation rate is to aggregate the costs into units (processes, lines, product groups) that summarize items that do not bias the "value of work time and production volume", and then divide them by the total work time to calculate the wage rate (how much per minute) or the total production volume to calculate the allocation rate (how much per item).
In the case of the labor rate, the unit manufacturing cost for each item is calculated by multiplying the number of man-hours (efficiency) per piece of each item.
Based on the allocation rate, the processing cost per item can be calculated as follows.
- Direct labor costs (time allocation): Rate of pay (how much per minute) x man-hours (how many minutes per piece)
- Depreciation (Time Allocation): Allocation rate (how much per minute) x operating hours (how many minutes per unit)
- Manufacturing overhead (quantity allocation): Allocation rate (how much per piece)
- S.G. & A. expenses (volume allocation): Allocation rate (how much per piece)
In the standard cost, the allocation rate is calculated in advance and multiplied by the standard man-hours prepared in advance to calculate the standard unit price for each cost item. In the actual cost, the actual unit price for each cost item is calculated by directly dividing the total amount of money allocated to the primary allocation destination by the work hours, so the allocation rate (how much per minute) and man-hours (how many minutes per item) are determined afterwards according to actual results.
The idea of the progressive system
First of all, the direct material cost input to the first process is calculated using the gross average method.
- Direct material cost = Total average unit price of input material x input quantity
In the same way, the work in progress manufacturing cost of the next process is calculated using the gross average method, considering the work in progress manufacturing cost, which is the direct material cost plus processing cost, as the cost of input items in the next process.
- Cost of input work in progress = Total average unit price of input work in progress x quantity of input work in progress
The Cumulative Method (Rolling Costing) refers to the method of repeating the production cost of the work in progress, which is the cost of the input work in progress plus the processing cost, as an input item in the subsequent processes.
The cost of materials on an outbound volume basis, which is part of the material delivered, becomes the cost of materials incurred on an in-process input volume basis; the cost of materials in-process on a production volume basis, which is part of the material in-process produced, becomes the cost of materials incurred on a product input volume basis; and the cost of sales on an outbound volume basis, which is part of the product shipped.
Normally, materials and work-in-progress are stocked or used for multiple products as common materials, so costs incurred on a self-process production quantity basis are larger than costs incurred on a next process input quantity basis.
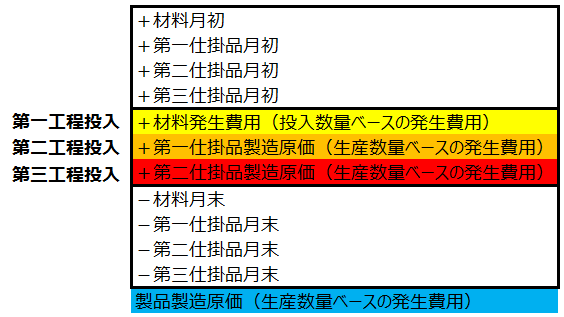
非累加法
When materials and work-in-progress are not common, 100% of the material cost incurred in the current month or the cost incurred on the basis of production quantity in the own process is the cost incurred on the basis of next process input quantity, and in the case of products, 100% of the cost incurred on the basis of production quantity (manufacturing cost) is the cost incurred on the basis of the quantity of products received.
On the other hand, the non-cumulative method is a method to calculate product manufacturing costs at once by treating processes 1 to 3 as one process.
In other words, the progressive method considers the product as an accumulation of cost expense codes for each process, while the non-progressive method aggregates the costs spent in each process into the cost expense code of the product itself.
Actual and planned allocations of manufacturing overhead (standard allocations)
There are various types of costing, but they are broadly divided into two types, actual cost and standard cost, and Hybrid cost and budgeted cost can be considered as a type of standard cost.
Fixed costs can be broadly divided into direct labor costs and manufacturing overhead costs, but direct labor costs are based on the labor rate, while manufacturing overhead costs start by calculating the allocation rate.
It is appropriate to allocate direct labor costs in proportion to time (man-hours = efficiency), such as "how much per hour", and since standard man-hours differ for each item, it is not appropriate to allocate production volume proportionally.
On the other hand, the depreciation of buildings, which is a manufacturing overhead cost, can only be prorated according to production volume, such as "how much per piece", and it cannot be prorated according to man-hours like labor costs.
In this way, the criteria for allocating items are different between direct labor costs and manufacturing overhead costs, even for the same fixed costs.
In the case of actual cost, the actual allocation rate is calculated based on the actual amount of manufacturing overhead costs incurred and the actual volume of the current month, whereas in the case of standard cost, the planned allocation rate (standard allocation rate) is calculated based on the budget and planned volume of manufacturing overhead costs.
If the basis for calculating the actual or scheduled allocation rate is work time allocation, then the allocation rate x man-hours = unit price by cost, and if the production volume is allocated, then the allocation rate = unit price by cost category.
- actual cost unit price
- Direct material costs (time allocation): Total average unit price
- Direct labor costs (time allocation): Actual wage rate calculated from the amount actually incurred x direct labor hours
- Depreciation (time allocation): Depreciation cost rate calculated from the amount actually incurred x direct operating hours
- Manufacturing overhead (volume allocation): Allocation rate calculated from the amount actually incurred
- standard cost unit price
- Direct material cost (time allocation): Standard unit price (from purchasing unit price master)
- Direct labour cost (time allowance): standard lease rate x standard work (capacity rate)
- Depreciation charge (time allocation): standard depreciation charge lease rate x standard operating time (capacity)
- Manufacturing overheads (quantity credits): standard credits rate
In the actual cost of the cost management system, the fixed cost is calculated by allocating the incurred cost after the cost center aggregation by the working time and the manufacturing quantity by the primary allocation, but in the cost management system, the labor cost unit price to allocate the working time is "labor rate x man-hour", and the manufacturing overhead cost unit price to allocate the manufacturing quantity is "allocation rate" itself.
The standard cost can be calculated without waiting for the actual input of the relevant month to be completed and is used to calculate quarterly and semi-annual budgets.
Standard costing procedure
The standard cost is calculated by using the purchasing unit price of purchased products managed in the production control master as the standard purchasing unit price of direct material costs, and the actual allocation rate calculated in the previous month's actual cost calculation or the planned allocation rate calculated from the results of the expansion calculation of the planned number of products to be produced or the standard efficiency (man-hours) as the standard allocation rate for fixed costs.
- Development calculation based on the BOM from the number of products to be produced
- Scheduled production of work in progress
Time development calculation based on scheduled production numbers and standard efficiency- Scheduled direct working hours for products and work-in-progress
- Expected Number of Purchased Items to be Purchased
- Scheduled production of work in progress
- Automatic calculation of the primary allocation ratio based on scheduled production or scheduled direct working hours
- Primary allocation calculation based on the primary allocation ratio and aggregation of fixed costs by cost center (product group or line)
- Set the calculation result of the allocation rate as the standard cost allocation rate
- Standard costing based on the standard unit price and standard cost allocation rate for direct material costs.
How to calculate the allocation rate
The wage rate (distribution rate) is a unit (process, line, product group) that combines items that do not bias the "value of work time and production quantity", and then divides it by the total work time to calculate the wage rate (how much per minute) or by the total production quantity to calculate the distribution rate (how much per item).
- Allocation rate calculation
- Amount of labor costs (actual or budgeted) ÷ hours worked = wage rate
⇒Wage rate x efficiency (man-hours) = labour costs - Manufacturing overhead (actual or budgeted) ÷ Quantity = Allocation rate
⇒Allocation rate itself = manufacturing overhead costs
- Amount of labor costs (actual or budgeted) ÷ hours worked = wage rate
In other words, if the cost per item is based on the budget, it is standard cost, and if it is based on the actual incurred amount, it is actual cost.
Direct material costs are calculated based on the gross average unit price for actual costs and the standard unit price for standard costs, while fixed costs (direct labor and manufacturing overhead), whether they are actually incurred or planned, are aggregated at the cost center in the primary allocation (interdepartmental or inter-product group allocation) and then allocated to each item based on working hours and production volume.
In standard costing, the standard unit price for direct material costs is the unit price of the purchasing unit master, direct labor costs are the labor rate x efficiency (man-hours), and the allocation rate for manufacturing overhead costs (quantity allocation) is the standard cost allocation rate.
In this way, in the standard costing, the standard unit price of the product is calculated by accumulating the standard fixed costs, which are allocated to the items in the budget for the current fiscal year based on the wage rate and allocation rate calculated in advance based on the actual results up to the previous fiscal year, into the standard unit price of the direct material cost.