Even if materials are received, if they are not used, the current month’s incurred costs are 0. In this sense, the current month’s incurred costs can be expressed as “the cost of materials used in the current month = incurred costs based on input.” If there is no manufacturing, the manufacturing cost is also 0, meaning the manufacturing cost can be expressed as “the cost of items completed in the current month = incurred costs based on production results.” If there are no sales, the cost of goods sold is also 0, meaning the cost of goods sold can be expressed as “the cost of items sold in the current month = incurred costs based on shipment results.” Cost Management in Indonesia Mass production factories, such as two- and four-wheeler parts manufacturers common in Indonesia, have multiple manufacturing processes. In such cases, processing costs are calculated for each process, and the method of aggregating these costs into the product is called process costing. In this approach, labor costs and manufacturing overheads are recorded at the end of the month by the accounting department, transferred to inventory assets, and then allocated accordingly. On the other hand, in factories producing custom-made items under individual order production, job order costing is used, where costs are aggregated by order number or project number. In this case, ... 続きを見る
Work-in-Process Appears as an End-of-Month Balance on the B/S, Not the P/L
When I first started studying costing, it took me quite a while to understand that manufacturing costs are the costs of producing products.
After finally grasping that manufacturing costs are “the costs of producing products,” what puzzled me next was, “Why is it that material costs, manufacturing costs, and cost of goods sold are calculated using the three-way method, but the manufacturing costs of work-in-process, which lies in between, are not calculated?”
- Beginning Material Inventory + Material Purchases This Month - Ending Material Inventory = Material Costs Incurred This Month
- Beginning Work-in-Process Inventory + (Material Costs Incurred This Month + Processing Costs This Month) - Ending Work-in-Process Inventory = Product Manufacturing Costs This Month
- Beginning Product Inventory + Product Manufacturing Costs This Month - Ending Product Inventory = Cost of Goods Sold This Month
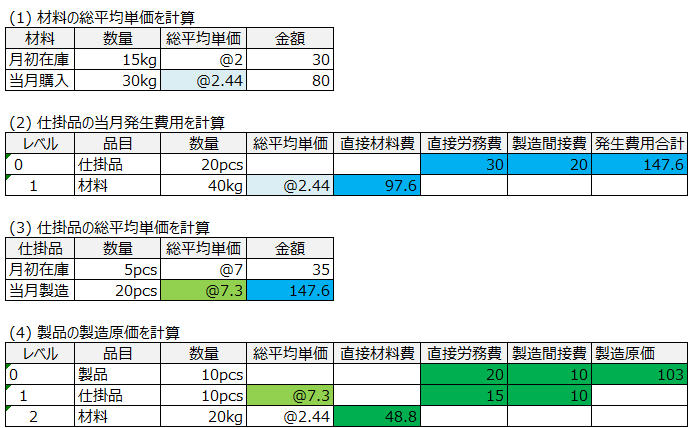
The aggregated costs of work-in-process at level 0 correspond to incurred costs.
Since the purpose of financial accounting is to prepare the P/L (Profit and Loss Statement) and B/S (Balance Sheet), calculating material costs incurred, manufacturing costs, and cost of goods sold is sufficient. Processing costs need only be allocated to products for the P/L to be complete. However, the ending balance of work-in-process that appears on the B/S includes only the material cost portion.
In Accounting, Costs Incurred This Month Correspond to Work-in-Process Manufacturing Costs
From an asset perspective, work-in-process is the state between materials and finished products.
- Materials ⇒ In Process (Material Cost Recognition + Processing Costs Incurred) ⇒ Products
In other words, once materials are used and their costs are recognized, they become work-in-process, and processing costs are added on top of that.
“What becomes work-in-process this month” is synonymous with “what is recognized as an expense this month,” and this corresponds to work-in-process manufacturing costs.
The costs incurred this month, namely “material costs incurred this month + processing costs incurred this month,” are exactly the work-in-process manufacturing costs for the month.
The manufacturing costs calculated as “total average unit price of work-in-process × quantity + direct labor costs + manufacturing overhead” are, after adjusting for ending inventory, the same as the result of “beginning work-in-process inventory + costs incurred this month - ending work-in-process inventory.”
- Beginning Material Inventory + Material Purchases This Month - Ending Material Inventory = Material Costs Incurred This Month
- Beginning Work-in-Process Inventory + Work-in-Process Manufacturing Costs This Month - Ending Work-in-Process Inventory = Product Manufacturing Costs This Month
- Beginning Product Inventory + Product Manufacturing Costs This Month - Ending Product Inventory = Cost of Goods Sold This Month
Calculating the Ending Balance of Work-in-Process
Now, if there arises a need to allocate processing costs, which are currently allocated only to products, to work-in-process as well, the costs incurred must be apportioned between what becomes products and what remains as work-in-process.
Material costs can be apportioned based on the input quantity as usual, but since processing costs are apportioned to different forms—products and work-in-process—it becomes necessary to convert work-in-process into product equivalents based on the degree of completion, which is quite a challenging task.
This is where a cost management system comes into play. One of the financial accounting purposes of implementing a cost management system is to calculate the ending balance of work-in-process with allocated processing costs—a task that is labor-intensive when done manually. To handle the apportionment of processing costs and the allocation of common materials that cannot be addressed by the three-way method, the total average method is used.
Costs Incurred for Common Materials That Cannot Be Calculated by the Three-Way Method
For common materials, the three-way method can calculate the costs incurred this month from beginning inventory, purchases this month, and ending inventory. However, since there is no amount based on input results, it is impossible to calculate the costs incurred per item.
With the total average method, not only can the costs incurred for common materials be calculated, but the manufacturing costs per product can also be derived from the parent-child relationship of input results.
- Costs Incurred for Common Materials
Common Material Input Result Quantity × Total Average Unit Price - Portion of Common Material Costs Included in Product A Manufacturing Costs
Common Material Usage Result Quantity × Total Average Unit Price
In Accounting Systems, Costs Incurred This Month Are “More Than Material Costs but Less Than Manufacturing Costs”
Since the ultimate goal of an accounting system is to prepare the P/L and B/S, it is not equipped with an item master.
- Beginning Material Inventory + Materials Purchased This Month - Material Costs Incurred (Portion That Became Work-in-Process) = Ending Material Inventory
- Beginning Work-in-Process Inventory + (Material Costs Incurred + Processing Costs Incurred) - Manufacturing Costs (Portion That Became Products) = Ending Work-in-Process Inventory
In accounting terms, material costs are incurred when materials are used. Of these, the portion that becomes products is recorded as manufacturing costs on the P/L, while the portion that does not become products is recorded as work-in-process in the ending work-in-process inventory on the B/S.
In other words, the costs incurred in an accounting system encompass everything “more than material costs but less than manufacturing costs,” all of which correspond to costs incurred to produce work-in-process.
Costs Incurred This Month Based on Production Results in a Cost Management System
However, in a cost management system, costs incurred are calculated for each work-in-process item as “total average unit price of input items × input quantity + processing costs of the current process.” As a result of cost accounting, the costs incurred per item and the total average unit price are maintained by cost category (direct material costs, direct labor costs, manufacturing overhead).
- Beginning Material Inventory + Materials Purchased This Month - Material Costs Incurred (Portion That Became Work-in-Process 1) = Ending Material Inventory
- Beginning Work-in-Process 1 Inventory + (Material Costs Incurred + Processing Costs Incurred) - Work-in-Process 2 Manufacturing Costs (Portion That Became Work-in-Process 2) = Ending Work-in-Process 1 Inventory
- Beginning Work-in-Process 2 Inventory + Work-in-Process 2 Manufacturing Costs - Manufacturing Costs (Portion That Became Products) = Ending Work-in-Process 2 Inventory
The costs incurred this month managed by item in a cost management system are work-in-process manufacturing costs. When the item happens to be a product, they become manufacturing costs, and these are cumulative amounts aggregated sequentially from the initial process.
Costs Incurred This Month Based on Input Results in a Cost Management System
The term “costs incurred” in accounting refers to costs incurred this month, with the ending balance that does not become products summarized as “work-in-process.” However, in a cost management system, it refers to the work-in-process manufacturing costs per item code.
In cases where there is a structure such as “Work-in-Process 1 ⇒ Work-in-Process 2 ⇒ Product,” the costs incurred at each process are managed by cost category.
- Initial Process: Material Costs and Processing Costs 1 Incurred ⇒ Work-in-Process 1
- Next Process: Processing Costs 2 Incurred ⇒ Added to Work-in-Process 1 to Become Work-in-Process 2
- Final Process: Processing Costs 3 Incurred ⇒ Added to Work-in-Process 2 to Become Products
To create a cost list per item by structure, it is necessary to manage the costs incurred at each process by cost category.
Tables Holding Calculation Results in a Cost Management System
Costs incurred based on production results are the manufacturing costs of work-in-process or products, while costs incurred based on input results become the costs incurred this month. Costs incurred this month do not necessarily become manufacturing costs and may remain as ending work-in-process inventory.
A table storing items with beginning inventory and purchase (production) quantities as level 0, along with a table storing their costs by category, generates a cost list by item (production result-based). A table storing the input quantities of levels 1 and below, including level 0, and a table storing their costs by category generate the detailed cost breakdown (input result-based).