If a production management system can manage receipt and disbursement results according to the account linkage chart, a cost management system can calculate the total average unit price of direct materials. Furthermore, by accumulating processing costs (direct labor costs and manufacturing overhead) for each process using the cumulative method, the material costs incurred this month, manufacturing costs this month, and cost of goods sold this month—necessary for P/L preparation—can be calculated. Cost Management in Indonesia Mass production factories, such as two- and four-wheeler parts manufacturers common in Indonesia, have multiple manufacturing processes. In such cases, processing costs are calculated for each process, and the method of aggregating these costs into the product is called process costing. In this approach, labor costs and manufacturing overheads are recorded at the end of the month by the accounting department, transferred to inventory assets, and then allocated accordingly. On the other hand, in factories producing custom-made items under individual order production, job order costing is used, where costs are aggregated by order number or project number. In this case, ... 続きを見る
Purpose of Implementing a Cost Management System
In financial accounting’s P/L (Profit and Loss Statement), profit is calculated in the following order: gross profit by subtracting cost of goods sold from sales, operating profit by subtracting selling, general, and administrative expenses (SG&A), ordinary profit by subtracting non-operating expenses, and net profit for the period by subtracting extraordinary losses. However, the expenses related to cost accounting are the inner components starting from the cost of goods sold.
To display gross profit on the P/L, the cost of goods sold must be calculated. To calculate the cost of goods sold, manufacturing costs must be calculated, and to calculate manufacturing costs, the material costs incurred this month must be determined.
- Gross Profit = Sales - Cost of Goods Sold
- Cost of Goods Sold = Beginning Product Inventory + Manufacturing Costs - Ending Product Inventory
- Manufacturing Costs = Beginning Work-in-Process Inventory + Material Costs Incurred This Month - Ending Work-in-Process Inventory
- Material Costs Incurred This Month = Beginning Material Inventory + Material Purchase Costs This Month - Ending Material Inventory
To meet these financial accounting requirements, it is necessary to calculate the valuation unit prices for the ending inventory quantities of materials, work-in-process, and products. If doing this in Excel is deemed too cumbersome, the introduction of a cost management system becomes a consideration.
Variable Costs and Fixed Costs
The cost of goods sold is the cost of products shipped (sold) from the product warehouse this month. Manufacturing costs are the costs of products with production results recorded this month, which can be rephrased as the costs of products received into the product warehouse this month.
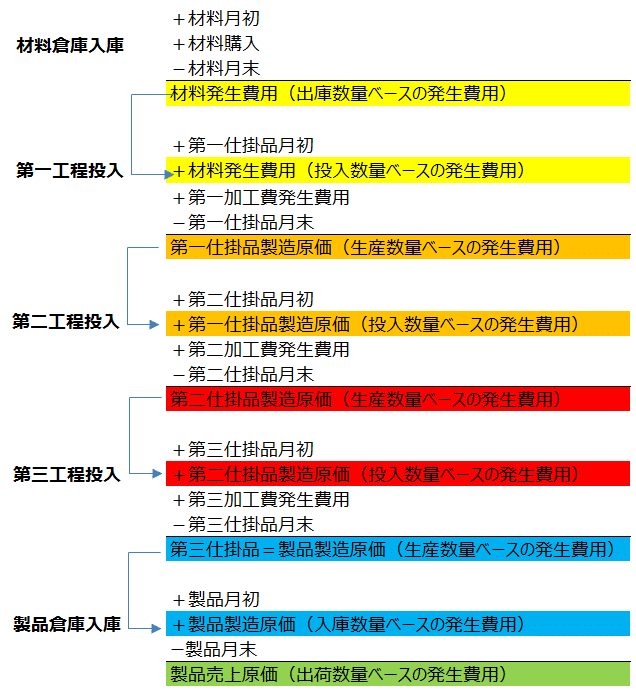
Once materials are input into the manufacturing process and processing costs are accumulated, they are collectively referred to as work-in-process (first work-in-process + second work-in-process + third work-in-process), being “greater than materials but less than products.”
The manufacturing cost of work-in-process in the current process is the cost of work-in-process with production results recorded in the current process this month. It is then input into the next process, becoming the work-in-process cost based on input quantity, with further processing costs accumulated.
Manufacturing costs consist of variable costs and fixed costs (processing costs). The production management system can only calculate variable costs such as direct material costs and outsourcing processing fees.
Beginning inventory, purchase results, input results, and production results are necessary for calculating variable costs using the total average unit price, while processing costs (direct labor costs and manufacturing overhead) are obtained from the accounting system.
The Unit of Aggregation Changes from Accounts to Items After Primary Allocation
A clear example of primary allocation is the depreciation cost of shared machinery like boilers or coolers. The total operating hours of each line, which serves as a cost center, are apportioned as the primary allocation ratio, and the allocation rate (cost per unit) is calculated by dividing by the manufacturing quantity for each line.
For manufacturing overhead, the total working hours of each product group, which serves as a cost center, are apportioned as the primary allocation ratio. The wage rate (cost per minute) is calculated by dividing by the working hours for each product group and multiplied by labor hours (efficiency).
- Calculate the primary allocation ratio from quantity and time:
- Aggregate the planned manufacturing quantity derived from material requirements planning based on the production plan, or the actual manufacturing quantity, by product group or line, and incorporate it under the allocation ratio code as the quantity-based primary allocation ratio.
- Aggregate the planned direct working hours (planned manufacturing quantity × standard labor hours [efficiency]) or actual direct working hours by product group or line, and incorporate it under the allocation ratio code as the time-based primary allocation ratio.
- Apportion actual fixed costs or budgeted fixed costs using the primary allocation ratio to aggregate fixed costs by product group or line.
- Divide the fixed costs by product group or line by actual time or planned time to calculate the allocation ratio (cost per minute) by cost category (direct labor costs, depreciation costs, expenses, etc.). For manufacturing quantity allocation, the allocation rate equals the unit price per cost category, so multiplication by labor hours is unnecessary.
- Multiply the allocation ratio by the actual working hours per unit or standard labor hours (efficiency) per item to calculate the actual unit price (standard unit price) per cost category per item. Cumulative calculation yields the actual unit price (standard unit price) per item.
Differences in Allocation Rate and Labor Hours Concepts Between Standard Costing and Actual Costing
The basic concept of allocation rates is to aggregate costs into a unit (process, line, product group) that groups items without bias in the “value of working hours or production quantity,” then recalculate the wage rate (cost per minute) by dividing by the total working hours or the allocation rate (cost per unit) by dividing by the total manufacturing quantity.
For wage rates, the manufacturing cost unit price per item is calculated by multiplying by the labor hours per unit (efficiency) for each item.
Based on the allocation rate, the processing cost per unit per item can be calculated as follows:
- Direct Labor Costs (Time Allocation): Wage Rate (Cost per Minute) × Labor Hours (Minutes per Unit)
- Depreciation Costs (Time Allocation): Allocation Rate (Cost per Minute) × Operating Time (Minutes per Unit)
- Manufacturing Overhead (Quantity Allocation): Allocation Rate (Cost per Unit)
- SG&A Expenses (Quantity Allocation): Allocation Rate (Cost per Unit)
In standard costing, the allocation rate is pre-calculated and multiplied by pre-prepared standard labor hours to compute the standard unit price per cost category. In actual costing, the amount aggregated to the primary allocation destination is divided by direct working hours to compute the actual unit price per cost category, so the allocation rate (cost per minute) and labor hours (minutes per item) are determined post-facto based on actual results.
Actual Allocation Rate and Planned Allocation Rate (Standard Allocation Rate) for Manufacturing Overhead
There are various types of cost accounting, but they can broadly be grouped into actual costing and standard costing, with realized costs or budgeted costs considered a subset of standard costing.
Fixed costs are broadly divided into direct labor costs and manufacturing overhead. Direct labor cost calculation starts with determining the wage rate, while manufacturing overhead cost calculation begins with determining the allocation rate.
Direct labor costs are appropriately apportioned in proportion to time (labor hours = efficiency), such as “cost per hour.” Since standard labor hours vary by item, apportioning by production quantity is not suitable.
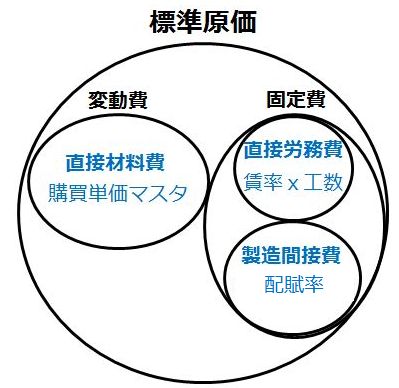
Thus, even among fixed costs, the criteria for apportionment to items differ between direct labor costs and manufacturing overhead.
In actual costing, the actual allocation rate is calculated based on the actual manufacturing overhead incurred and actual quantities for the month, whereas in standard costing, the planned allocation rate (standard allocation rate) is calculated based on the manufacturing overhead budget and planned quantities.
If the basis for calculating the actual or planned allocation rate is time allocation, it becomes “allocation rate × labor hours = unit price per cost category.” If it is quantity allocation, it becomes “allocation rate = unit price per cost category.”
- Actual Cost Unit Price
- Direct Material Costs (Time Allocation): Total Average Unit Price
- Direct Labor Costs (Time Allocation): Actual Wage Rate Calculated from Actual Amount × Direct Labor Hours
- Depreciation Costs (Time Allocation): Depreciation Wage Rate Calculated from Actual Amount × Direct Operating Time
- Manufacturing Overhead (Quantity Allocation): Allocation Rate Calculated from Actual Amount
- Standard Cost Unit Price
- Direct Material Costs (Time Allocation): Standard Unit Price (From Purchasing Unit Price Master)
- Direct Labor Costs (Time Allocation): Standard Wage Rate × Standard Labor Hours (Efficiency)
- Depreciation Costs (Time Allocation): Standard Depreciation Wage Rate × Standard Operating Time (Efficiency)
- Manufacturing Overhead (Quantity Allocation): Standard Allocation Rate
In actual costing within a cost management system, fixed costs are apportioned by primary allocation, calculated by dividing the costs aggregated to cost centers by working hours or manufacturing quantities. Within the cost management system, the labor cost unit price for time allocation is “wage rate × labor hours,” while the manufacturing overhead unit price for quantity allocation is the “allocation rate” itself.
Standard costing can be calculated without waiting for the completion of actual input for the month and is used to compute quarterly or semi-annual budgets.
Steps in Standard Costing
In standard costing, the purchase unit price of purchased items managed in the production management master is used as the standard purchase unit price for direct material costs. The actual allocation rate calculated from the previous month’s actual cost accounting, or the planned allocation rate derived from the planned production quantity of products or standard efficiency (labor hours), is used as the standard allocation rate for fixed costs.
- Explode calculations based on BOM from the planned production quantity of products:
- Planned production quantity of work-in-process
Time explosion calculation based on planned production quantity and standard efficiency:- Planned direct working hours for products and work-in-process
- Planned purchase quantity of purchased items
- Planned production quantity of work-in-process
- Automatically calculate the primary allocation ratio based on planned production quantity or planned direct working hours
- Perform primary allocation based on the primary allocation ratio and aggregate fixed costs by cost center (product group or line)
- Set the allocation rate calculation result as the standard cost allocation rate
- Calculate standard costs based on the standard unit price of direct material costs and the standard cost allocation rate
How to Calculate Allocation Rates
The wage rate (allocation rate) is calculated by aggregating costs into a unit (process, line, product group) that groups items without bias in the “value of working hours or production quantity,” then recalculating the wage rate (cost per minute) by dividing by the total working hours or the allocation rate (cost per unit) by dividing by the total manufacturing quantity.
- Allocation Rate Calculation
- Labor Cost Amount (Actual Amount or Budget) ÷ Working Hours = Wage Rate
⇒ Wage Rate × Efficiency (Labor Hours) = Labor Costs - Manufacturing Overhead Amount (Actual Amount or Budget) ÷ Quantity = Allocation Rate
⇒ Allocation Rate Itself = Manufacturing Overhead
- Labor Cost Amount (Actual Amount or Budget) ÷ Working Hours = Wage Rate
In other words, if the cost per cost category per item is based on a budget, it is standard costing; if based on actual amounts incurred, it is actual costing.
Direct material costs are calculated based on the total average unit price in actual costing and the standard unit price in standard costing. Fixed costs (direct labor costs and manufacturing overhead), whether actual or planned amounts, are aggregated to cost centers through primary allocation (inter-departmental or inter-product group allocation) and then apportioned to items by working hours or manufacturing quantity.
In standard costing, the standard unit price of direct material costs is the unit price from the purchasing unit price master, direct labor costs are wage rate × efficiency (labor hours), and the allocation rate for manufacturing overhead (quantity allocation) is the standard cost allocation rate.
Thus, in standard costing, the standard unit price of products is calculated by accumulating the standard fixed costs—apportioned to items based on the wage rate and allocation rate pre-calculated from prior period results—onto the standard unit price of direct material costs for the current period’s budget.