Be aware of pre- and post-reschedule factors that adversely affect the production schedule
Of all the functions of a production control system, I think that the planning functions such as MRP and the scheduler are highly difficult to implement on the shop floor, but on the other hand, even in Indonesia, where systemization is lagging behind, there are actually factories that operate schedulers properly.
The more lines (machines) there are, the harder it is to manage the cycle time for each item line, so I think there are many cases where the load calculation is based on the standard load for each line.
Rather than developing a line-by-line cycle time for each item that is not currently properly maintained, we can start by setting a standard load for each line in the scheduler master and obtaining rescheduled results that will not overflow the load.
Factors that adversely affect the production schedule are pre- and post-reschedule.
- Incorrect master or balance information (a pre-reschedule factor).
- Unforeseen events (line stoppages, production failures, material shortages) occur on site (post-reschedule factors).
In other words, even if we can overcome the factors before the rescheduling and create a theoretically correct schedule based on 100% accurate data, there will be errors after the rescheduling because there will be adverse factors after the rescheduling.
The important thing is to take in the shipping schedule (order received) correctly so that there are no product manufacturing omissions, to take in the MPS (standard production plan) correctly when the shipping lot and the manufacturing lot are different, and to be aware of the connection between the end-parent order and the manufacturing order of the child items. If these are followed, mistakes in the master can be corrected while operating.
Be aware of the link between orders and production lots
If the lots between processes are different, it will be difficult to match the lots on the system to the movement of the actual product when the scheduler is first installed, and when the entire experience is seen on the Gantt chart, it will deviate from the movement on site.
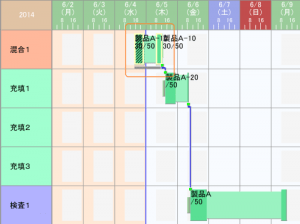
Only the actual quantity has been entered.
Furthermore, if the scheduler automatically replenishes the difference between the plan and the actual results (supply and demand adjustment 1:1) then tracing will become almost impossible and it will be difficult to match the movement of the site with the ties between the lots on the system.
If only the actual quantity is entered and rescheduled when the actual quantity is recorded, the time line required to produce the difference from the planned quantity within the plan period will be occupied.
Therefore, if the production is completed with less than the planned quantity, the line occupied within the planned period will be released by entering not only the actual quantity but also the date of acquisition of the actual quantity and completing the status.
- When actual results are posted ⇒ Actual quantity is updated.
- Completion of Production ⇒ Enter the date of acquisition of results and complete the status.
Or complete only the status and leave it unallocated.
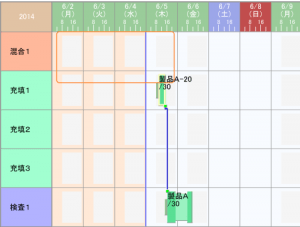
Only the status is completed with no achievement date.
If only the status is completed without an actual acquisition date, then the scheduler cannot determine when to assign it and it will be unassigned, but as long as it has been manufactured, there is no problem in the sense that it does not affect the planning period.
Assigning the manufacturing orders to the order received in a 1:1 fashion makes it easy to map the actual product to the system but if that is difficult then create an MPS from the order received and assign it from the MPS in a 1:1 fashion. In either case it is necessary to enter the scheduler lot number (work code) on the item sheet and match the system to the actual product.
Be aware of the difference between production instructions by order and the purpose of the production schedule and the difference between the difference between the production instructions by order and the difference table by line
If "the scheduler is operated" means "the production schedule is output from the system", then the production schedule becomes a table of difference when it is pasted on the whiteboard at the manufacturing site for each line, and if the input items are described for each manufacturing item, it becomes a manufacturing instruction.
There are only two ways of outputting a production schedule, vertically and horizontally, and if it is in the form of a vertical table (the vertical axis is the date), it is easy to create a form, but if it is in the form of a horizontal timetable (the horizontal axis is the date), it is more difficult to create a form, and it is necessary to display the planned daily quantity according to whether the unit of performance collection at the site is an hourly unit or a shift unit, and to display it proportionally according to the production capacity.
The reason why the format of the output differs in this way is because there is a difference in the purpose of the production control system, which emphasizes quantity management for each process, and the production scheduler, which emphasizes time management for each line.