月初在庫があっても当月投入実績がない品目は、B/S上資産として計上されたままで、当月製造原価として費用化しません。投入済み未出来高(工程内在庫)は存在しない前提で言えば、実際原価計算の本質は総平均単価の費目別積上げによる投入品目の製造原価の計算と、自工程加工費の品目配賦です。 インドネシアの原価管理システム インドネシアの日系製造業を取り巻く市場環境は、頻繁に起こる需要変動や世界的物流網の停滞による資材の調達難、多品種少量化に伴う小ロット化などへ対応するための生産効率改善努力をすると同時に、迅速かつ戦略的な経営判断のためのより細かく多角的な原価管理が求められています。 続きを見る
総平均法による製造原価算出
製造原価は三分法により「月初仕掛品+当月製造費用-月末仕掛品」で算出され、前工程の製造原価を自工程の当月製造費用に振替えて三分法でマルチレベルに製品原価を算出することをころがし法(Rolling costing)といいます。
一方で総平均法では製造原価を「投入品目の月次総平均評価額+自工程発生費用」で算出し、材料から製品に向かって順番に総平均単価を算出し、「(総平均単価x投入実績数量)+自工程発生加工費」で各工程の原価を積み上げていくことを積上法といいます。
ころがし法も積上法も結果的には同じになるので、両者は同義で用いられることが一般的ではないかと思います。
- 総平均単価=(月初在庫金額+当月製造原価)/(月初在庫数量+当月製造数量)
総平均法の特徴としては、月初在庫情報を加味して総平均単価で払出原価の計算が可能であることであり、自工程の生産品目の総平均単価が次工程への投入実績の単価に適用されます。
- 投入実績数量x総平均単価
- 直接労務費(自工程発生原価)
- 製造間接費(自工程発生原価)
この合計が当月製造原価となり、これに月初在庫を加味して総平均単価を求め、さらに次工程への投入実績の単価として適用し、最終工程において製品製造原価となります。
累加法(積上法)の考え方
生産管理システムにて勘定連絡図に沿って受払数量が管理され、原価管理システムにて製造原価(当月製造した品目原価)を計算しますが、まず初工程に投入された直接材料費を総平均法にて計算します。
- 直接材料費=投入材料の総平均単価x投入数量
この直接材料費に加工費を足した仕掛品製造原価を、次工程の投入品目の発生費用と考えて、同じように次工程の仕掛品製造原価を総平均法にて計算します。
- 投入した仕掛品の費用=投入仕掛品の総平均単価x投入数量
この投入した仕掛品の費用に加工費を足した仕掛品製造原価を、それ以降の工程でも投入品目として、繰り返していく方法を累加法(Cumulative Method=Rolling Costing)といいます。
出庫された材料の一部である出庫数量ベースの材料費が、仕掛品への投入数量ベースの発生費用となり、生産された仕掛品の一部である生産数量ベースの仕掛品費用が製品への投入数量ベースの発生費用となり、出荷された製品の一部である出荷数量ベースの売上原価となります。
通常は材料や仕掛品は、在庫となったり、共通材として複数の製品に使われたりするため、自工程生産数量ベースの発生費用は次工程投入数量ベースの発生費用よりも大きくなります。
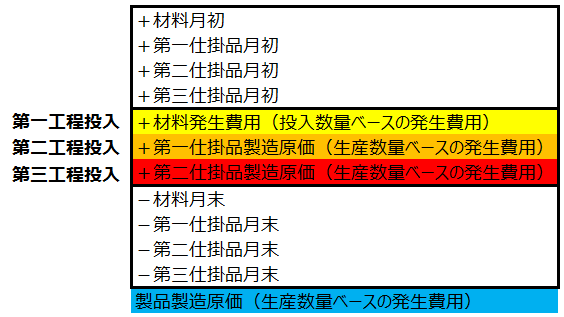
非累加法
材料や仕掛品が共通材でない場合には、当月発生材料費用または自工程生産数量ベースの発生費用は、その100%が次工程投入数量ベースの発生費用となり、製品の場合は生産数量ベースの発生費用(製造原価)の100%が、製品の入庫数量ベースの発生費用になります。
勘定連絡図に従って自工程発生費用が次工程投入費用として積み上げられていく累加法に対して、第一工程から第三工程までを一つの工程とみなして一気に製品製造原価を計算する方法が非累加法(Non-Cumulative Method)です。
つまり累加法は製品を工程別の原価費目コードの積み上げと考え、非累加法は製品自体の原価費目コードに各工程でかかった原価を集計してしまう方法です。
製造原価と総平均単価の関係
大手自動車メーカーの認証不正問題が話題になっていますが、出荷停止が何日も続けばその月の生産量がガタ落ちするわけで、生産数量が落ちれば製品1個当たりの減価償却費や労務費などの固定費の比率が上がってしまい、結果として製品1個当たりの製造原価も大きくなってしまいます。
そもそも市場の変化に合わせて調整していく生産数量に対して、毎月の固定費は一定であるため、実際の生産数量をベースに製造原価を計算していては近視眼的な原価管理しか出来なくなるため、年間を通して平準化した標準原価を来期の予算作成前に決定して、販売計画や調達計画を立てるわけです。
この年間通して変わらない標準原価に対して、各月の製造原価がどれだけ上振れ下振れしたかを表すのが原価差異であり、材料の購入価格・購入数量・操業時間など要因ごとに差異を細分化するのが原価差異分析です。
このように原価差異とは、基準値である標準原価に対して当月の製造原価がどれくらい乖離したかを表すものであり、当然ながら月初に積みあがっていた在庫にはこの原価差異の責任はないわけですが、出荷時には在庫分も当月製造分も一緒くたにまとめられて総平均で評価されることで、最終的には売上原価単価として連帯責任を負わされる言えます。
製造原価単価とは当月製造分の単価であり、総平均単価とは月初在庫と当月製造分をまとめた全体の単価であり、製品の総平均単価が売上原価単価ということになります。
これはよく混乱するのですが「製造原価を総平均単価を使って計算する」と言われるのは「製品の総平均単価x製造数」ではありません。
製品の総平均単価は「月初製品在庫+当月製品製造原価」を元に計算されるものであり、製造原価の後に算出されるものだからです。
つまり製造原価算出時に存在する総平均単価は、川下から川上に向かって総平均単価が計算される以上、投入品目の総平均単価だけになります。
総平均単価は費目別に算出され、次工程の投入品目の当期製造原価に費目別に反映されます。
- 直材総平均単価=(月初直材+当月直材)/(月初数量+当月数量)
- 直労総平均単価=(月初直労+当月直労)/(月初数量+当月数量)
- 製間総平均単価=(当月製間+当月製間)/(月初数量+当月数量)
これらの費目別総平均単価も川上に行くにつれ累加されていきますが、自工程で費用が発生していない費目は、前工程の累加原価と同額であるため、費目別発生原価には計上されません。当月製造原価とは各工程の投入品目の発生原価を費目別総平均単価で評価するものです。
総平均単価の費目別積上げ計算
総平均単価の費目別積上げ計算ができれば、使用数量を掛けることにより、自動的に費目別の当月製造原価が算出できます。
当月製造原価と月初在庫金額があってはじめて総平均単価が算出され、総平均単価は次工程の投入実績評価額の基本となります。総平均単価による投入実績評価額と自工程加工費(配賦による)とあわせたものが当月製造原価となり、これを川上(材料)から川下(製品)まで繰り返していくと最終製品の製造原価ならびに総平均単価が求められます。
総平均単価は費目別に川上から川下に積み上げられ、前工程までの累加額との差額が自工程発生分の総平均単価になります。
総合原価計算は見込み生産(大量連続生産=マスプロダクション向き)
三分法で「月初仕掛品+当月製造費用-月末仕掛品」で算出される製造原価は、総平均法では「投入品目の総平均評価額+自工程発生費用」で算出するので、材料から製品に向かって順番に総平均単価を算出する必要があります。
総合原価計算を採用する工場には、通常は製造工程が複数あり各工程ごとに工程費を求めますが、製品に集計する方法には累加法と非累加法があります。
累加法(Cumulative method)は前工程の製造原価(期首+当月費用-期末)を自工程投入費用として振替えて三分法でマルチレベルに製品原価を算出するころがし法(Rolling costing)で、勘定連絡図のイメージに近いです。
- 第1工程:月初仕掛1+当月材料+当月加工1-月末仕掛1=当月仕掛1製造原価
- 第2工程:月初仕掛2+当月仕掛1製造原価+当月加工2-月末仕掛2=当月製品製造原価
「Rolling Costing」は「積み上げ計算」であり「ころがし法」でもあり、材料費から順番に、勘定連絡図に従って各工程の加工費を順番に積み上げていく「累加法(Cumulative method)」です。
非累加法(Non-cumulative method)は前工程費を含めずにシングルレベルで各工程費を計算し、それらを直接合計して製品原価を求める方法です。
- (製品に占める第1工程費用)
月初仕掛1+月初仕掛(第2の第1部分)+当月加工1-月末仕掛1-月末仕掛(第2の第1部分)
- (製品に占める第2工程費用)
月初仕掛(第2の第2部分)+当月加工2-月末仕掛(第2の第2部分)
- 第1工程費用+第2工程費用=当月製品製造原価
総平均法のための受払実績データ
材料を購入し、加工済仕掛品を外注に無償支給し、外注加工済み製品を出荷するプロセスで発生する生産管理システム上の実績データは下図のようになります。
- 出庫実績 ⇒ 他勘定振替のため
仕損による廃棄や棚卸減耗を売上原価から控除します。仕掛品単価は当月の「総平均単価+加工費」の積み上げで評価されます。 - 投入実績⇒直接材料費計算のため
投入ベースの発生費用であり、親に対して子が何個投入されたか。 - 生産実績⇒直接材料費計算のため
生産ベースの発生費用であり、親が何個生産されたか。 - 支給実績⇒直接材料費計算のため
外注先に何個支給されたか。 - 購入・外注実績⇒直接材料費・外注加工費計算のため
材料に対して購入費用がいくらかかったか。また製品に対して外注加工費がいくらかかったか。 - 売上実績⇒売上原価計算のため
売上総利益を計算します。