MRP biasa disebut sebagai penumpukan beban kapasitas tak terbatas dan memeriksa apakah pesanan dapat masuk dalam rentang kapasitas produksi, tetapi dengan penjadwalan produksi yang menggunakan pendekatan pemecahan beban kapasitas terbatas, dapat diperiksa apakah jadwal yang realistis dan tidak menyebabkan keterlambatan pengiriman dapat dibuat. Production Scheduler di Indonesia Di dalam pekerjaan manajemen produksi di pabrik-pabrik massal berbasis perakitan yang banyak ditemukan dalam industri roda dua dan roda empat di Indonesia, rencana produksi dan rencana beban memiliki hubungan yang saling terkait erat. Karena rencana produksi disusun berdasarkan jumlah, maka ada permintaan kuat untuk melihat rencana beban juga berdasarkan jumlah per mesin. Secara umum, rencana produksi dan rencana beban diharapkan disusun dalam satuan hari atau shift. Di dalam pikiran perencana Indonesia, ada pola pikir seperti: “Hari ini (atau dalam shift ini), berapa unit yang akan diproduksi oleh mesin ini? Jika ada kelebihan kapasitas sebanyak sekian unit, kapan unit tersebut akan ... 続きを見る
Perbedaan Pemikiran antara Penjadwalan Produksi Berbasis Kuantitas dan Berbasis Waktu yang Sering Menjadi Tantangan di Indonesia
Berdasarkan pengalaman saya, di sebagian besar lokasi manufaktur di Indonesia, rencana produksi dibuat dengan pemikiran berbasis kuantitas, yaitu berapa banyak unit yang dapat ditumpuk terhadap kapasitas shift mesin atau lini, atau kapasitas harian.
Jika selama bertahun-tahun rencana produksi dibuat dengan menganggap sel Excel sebagai satu shift atau satu hari, maka wajar saja jika pemikiran ini menjadi hal yang biasa.
Di sisi lain, penjadwal produksi menggunakan pemikiran berbasis waktu, yaitu mengalokasikan tugas ke slot waktu kosong seperti pukul 08:00 hingga 17:00.
Jika diungkapkan dengan gaya IT, perbedaan keduanya adalah apakah objek dibuat per shift atau per hari, atau dibuat per unit perintah produksi. Meskipun keduanya memiliki tujuan yang sama yaitu membuat rencana produksi, saya merasa perbedaan pemikiran ini tidak mudah disatukan.
Oleh karena itu, saat memperkenalkan penjadwal produksi di Indonesia (dan mungkin di seluruh Asia), tugas yang dialokasikan berdasarkan waktu yang melintasi shift atau hari perlu dihitung ulang berdasarkan waktu pemisahan shift atau hari.
Tidak jelas apakah alat seperti Excel sesuai dengan logika dalam pikiran manusia, atau apakah pikiran manusia terlalu dipengaruhi oleh karakteristik Excel, tetapi yang pasti, jika sistem tidak berupaya menyesuaikan diri dengan situasi saat ini, tampaknya sulit diterima oleh pekerja di lokasi manufaktur.
Pekerjaan Departemen Manajemen Produksi
Hubungan antara Rencana Produksi dan Rencana Beban
Sama seperti di Jepang, di Indonesia pun, departemen manajemen produksi di industri manufaktur (PPIC = Production Planning Inventory Control) membuat rencana produksi dasar (MPS = Master Production Schedule) yang disesuaikan per hari berdasarkan informasi pesanan pasti dari pelanggan atau informasi awal, dengan mempertimbangkan stok produk dan jadwal kerja.
MPS ini kemudian diuraikan ke dalam daftar kebutuhan material (BOM = Bill of Material) dengan mempertimbangkan waktu tunggu untuk membuat perintah produksi. Namun, di Indonesia, sangat jarang ada kasus di mana perintah produksi dibuat dengan memanfaatkan MRP (Material Requirement and Planning) dari sistem manajemen produksi; biasanya ini dilakukan dengan Excel.
Dengan menyusun perintah produksi yang telah dibuat secara kronologis, jadwal produksi per item (rencana produksi bulanan) dibuat, dan ini disebut sebagai rencana produksi (Production Planning).
Dalam merumuskan rencana produksi dan mengeluarkan perintah produksi ke lapangan, alokasi ke lini diperlukan. Beban kerja yang diterapkan pada lini saat ini disebut beban (Loading). Untuk menangani beban ini, prediksi dibuat untuk menentukan apakah sumber daya yang ada cukup, dan pada tahap persiapan produksi, beban didistribusikan, lembur ditambahkan, atau lini baru ditambahkan—ini disebut rencana kapasitas (Capacity Planning).
Dengan kata lain, rencana produksi dan rencana beban saling terkait erat, dan kesalahan dalam rencana beban langsung mengarah pada kesalahan dalam rencana produksi (keterlambatan pengiriman).
Tugas Pembuatan Rencana oleh Departemen Manajemen Produksi
MRP dalam sistem manajemen produksi adalah rencana produksi sementara yang menggunakan pendekatan kapasitas tak terbatas ke belakang tanpa mempertimbangkan rencana beban. Perintah produksi ditumpuk per lini, dan sementara memastikan ada sumber daya produksi dan waktu operasional yang cukup untuk menyelesaikan perintah produksi, alokasi penyeimbangan ke sumber daya alternatif atau jadwal alternatif dilakukan secara manual.
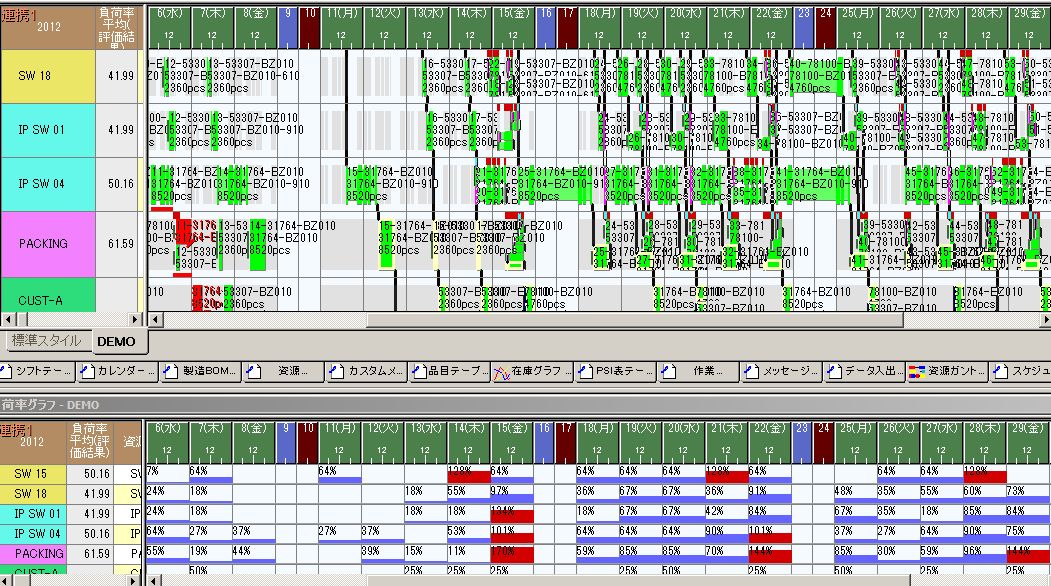
Dalam MRP, tugas antar proses dihubungkan secara vertikal
Sebaliknya, dalam rencana produksi dengan pendekatan pemecahan kapasitas terbatas yang mempertimbangkan rencana kapasitas, dapat diperiksa seberapa banyak kelebihan yang terjadi dalam batasan jumlah sumber daya saat ini dan waktu operasional.
Perbedaan antara Memaksa Alokasi atau Mengabaikan Tugas yang Melimpah
Perbedaan antara Memaksa Alokasi dan Mengabaikan
Jika ada perintah penyesuaian dalam parameter rencana, cara alokasi saat terjadi kelebihan (saat melanggar batasan waktu atau melebihi rentang rencana) dapat dikontrol. Jika tidak ada perintah penyesuaian dalam parameter rencana, parameter ini akan diabaikan.
Memaksa alokasi berarti memasukkan secara paksa dalam periode tertentu dengan kapasitas tak terbatas, sedangkan mengabaikan berarti, sesuai namanya, tidak memikirkan apa pun dan mengalokasikan dengan kapasitas terbatas dalam periode tertentu dan kapasitas tak terbatas di luar periode tersebut.
Cara Alokasi saat Backward
Dalam pendekatan backward, jika tidak ada pengaturan saat "melebihi waktu mulai alokasi", maka perilakunya sama dengan memaksa alokasi (kapasitas tak terbatas), dan penumpukan akan terjadi di sisi kanan tanggal dasar rencana (dalam periode rencana), karena membuat rencana untuk masa lalu tidaklah bermakna.
Jika Anda ingin tugas yang melimpah dalam pendekatan backward ditumpuk di sisi kiri tanggal dasar rencana (di luar periode rencana), atur "saat melebihi waktu mulai alokasi" ke "abaikan" (menembus dan mengalokasikan dengan kapasitas tak terbatas).
Cara Alokasi saat Forward
Dalam pendekatan forward, jika tidak ada pengaturan saat "melebihi waktu selesai alokasi", maka perilakunya sama dengan mengabaikan (menembus dan mengalokasikan dengan kapasitas tak terbatas), dan penumpukan akan terjadi di sisi kanan waktu selesai alokasi (di luar periode rencana).
Jika Anda ingin penumpukan terjadi dalam periode rencana waktu selesai alokasi dalam pendekatan forward, atur "saat melebihi waktu selesai alokasi" ke "memaksa alokasi" (kapasitas tak terbatas).
Memeriksa Status Beban Rencana Produksi agar Tidak Terlambat Pengiriman
Tentu saja, staf yang bertanggung jawab atas rencana produksi berusaha membuat rencana produksi yang tidak menyebabkan keterlambatan pengiriman, tetapi karena kapasitas peralatan tidak selalu cukup, mereka perlu memeriksa setiap hari berapa banyak beban yang ada dan di mana beban berlebih terjadi, serta mengambil tindakan pencegahan sebelumnya.
Dengan mengalokasikan secara forward dan hanya memaksa alokasi (kapasitas tak terbatas) saat terjadi pelanggaran batasan waktu (saat melebihi waktu selesai terakhir atau waktu mulai paling awal), sumber daya dan periode yang mengalami kelebihan beban (kekurangan kapasitas) dapat diperiksa.
Sebagai catatan, alokasi backward awalnya didasarkan pada tanggal pengiriman, sehingga keterlambatan pengiriman tidak terjadi, hanya kelebihan beban yang muncul.
Waktu mulai paling awal dan waktu selesai terakhir adalah kriteria untuk pelanggaran batasan waktu. Dalam pendekatan forward, melebihi waktu selesai terakhir (melebihi waktu mulai paling awal dari proses berikutnya) berarti "proses sebelumnya terlalu lambat sehingga proses berikutnya tidak dapat selesai tepat waktu".
Berdasarkan hasil ini, keputusan seperti "kapan dan berapa persen kelebihan beban terjadi sehingga rencana produksi perlu diubah atau lembur ditambahkan" dapat dibuat.
Rencana Waktu Siklus dan Rencana Kapasitas
Memecahkan tugas yang ditumpuk berdasarkan waktu siklus bertujuan untuk menentukan urutan tugas, menyeimbangkan beban, dan membuat rencana yang secara teoritis dapat dilaksanakan tanpa melanggar batasan waktu. Ini adalah metode yang menekankan pada kalender rencana jadwal kerja (sumbu horizontal).
Namun, meskipun urutan tugas telah ditentukan dan instruksi diberikan ke lapangan, dalam kenyataannya, sulit untuk melaksanakan tugas sesuai urutan karena berbagai keadaan di lapangan. Merefleksikan elemen yang dapat memengaruhi rencana yang muncul di lapangan ke dalam sistem dan menjadwal ulang mungkin tidak realistis.
Jika demikian, dengan syarat tidak ada keterlambatan pengiriman, lebih realistis untuk menumpuk lot tugas dalam rentang kapasitas harian (kuantitas produksi atau waktu operasional) dan mengeluarkan instruksi seperti "hari ini, selesaikan lot tugas ini di masing-masing lini". Ini adalah metode yang menekankan pada kapasitas sumber daya (sumbu vertikal).
- Flag "Jumlah Sumber Daya yang Dialokasikan" pada tabel sumber daya diatur ke "Proporsional dengan Kuantitas Produksi"
- Kapasitas produksi pada BOM produksi diatur tetap per hari ( ember waktu 1 hari)
Untuk kasus "1 lot per hari: kapasitas harian 8.000 unit, 5 mesin, jumlah sumber daya 40.000 unit":
- Ukuran lot produksi maksimum pada tabel item diatur ke kapasitas harian (kuantitas) (1 hari 1 kotak)
- Jumlah sumber daya pada tabel kalender diatur ke ukuran lot produksi x jumlah sumber daya (penumpukan untuk jumlah sumber daya selama 1 hari)
Untuk kasus "1 lot per jam: kapasitas harian 8.000 unit, 1 lot 1.000 unit, 1 mesin, jumlah sumber daya 8.000 unit":
- Ukuran lot produksi maksimum pada tabel item diatur ke kapasitas per jam (kuantitas) (1 jam 1 kotak)
- Jumlah sumber daya pada tabel kalender diatur ke ukuran lot produksi x jumlah sumber daya (8 penumpukan selama 1 jam)
Memeriksa Beban dengan "Penumpukan" dan Memastikan Jadwal yang Realistis dengan "Pemecahan"
Fungsi perhitungan beban MRP mengatur beban standar per item per lini (waktu siklus), menghitung berapa menit beban yang diterapkan ke lini berdasarkan jumlah pesanan, dan "menumpuk" pada hari yang digeser berdasarkan waktu tunggu (hari). Dengan membandingkannya dengan kapasitas lini harian, kemenangan atau kekalahan harian dapat diperiksa.
Untuk mengetahui apakah kelebihan kapasitas lini yang terdeteksi dari hasil "penumpukan" harian dapat memenuhi tenggat waktu jika dialokasikan lebih awal, "pemecahan" dilakukan, dan ini dilakukan secara otomatis oleh penjadwal produksi.
"Memecahkan" berarti menentukan urutan tugas agar tidak melanggar batasan waktu dan membuat jadwal yang "secara teoritis dapat dilaksanakan". Ini adalah metode yang menekankan pada kalender rencana jadwal kerja (sumbu horizontal).
Namun, untuk membuat jadwal yang dioptimalkan, tidak mungkin bagi manusia untuk mengatur semua kondisi pembatas di lokasi produksi ke dalam penjadwal secara 100% tanpa kebocoran. Jika demikian, daripada teori ideal yang mencerminkan hasil "pemecahan" langsung sebagai jadwal di lapangan, cukup memastikan bahwa "pemecahan" menunjukkan tidak ada keterlambatan pengiriman secara kasar. Setelah itu, menetapkan stok pengaman untuk beberapa hari sebagai cadangan untuk berjaga-jaga menjadi metode pengoperasian sistem yang lebih realistis.
Dengan syarat tidak ada keterlambatan pengiriman, lebih realistis untuk membuat daftar lot tugas dalam rentang kapasitas harian dan mengeluarkan instruksi seperti "hari ini, selesaikan lot tugas ini di masing-masing lini". Ini adalah metode yang menekankan pada kapasitas sumber daya (sumbu vertikal).
Hubungan antara Cara Tumpang Tindih Antar Proses, Stok Pengaman, dan Ukuran Lot
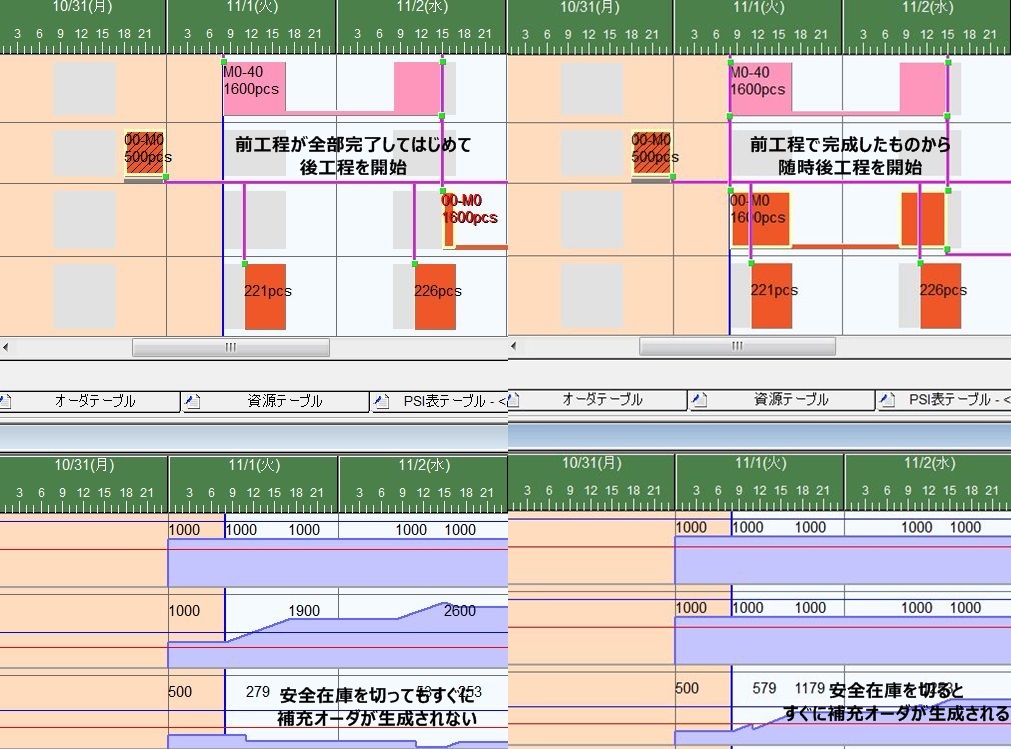
Kiri adalah SE, kanan adalah hasil alokasi SSEE
Stok pengaman yang disebutkan di atas dipertimbangkan saat pembuatan pesanan pengisian ulang selama ekspansi pesanan, tetapi waktu pembuatan pesanan pengisian ulang bervariasi tergantung pada cara tumpang tindih antar proses.
Dalam ekspansi pesanan, dengan fungsi pengisian ulang otomatis, pesanan produksi untuk kekurangan instruksi masukan tugas dari pesanan diterima dihasilkan sebagai pesanan pengisian ulang (anak) sambil merujuk pada BOM produksi untuk memenuhi daftar pesanan. Pesanan produksi untuk kekurangan instruksi masukan tugas dari pesanan pengisian ulang (anak) dihasilkan sebagai pesanan pengisian ulang (cucu).
Jika cara tumpang tindih antar proses adalah ES (End-Start), tugas proses saat ini hanya dapat dimulai setelah tugas proses sebelumnya selesai. Oleh karena itu, waktu tercepat pembuatan pesanan pengisian ulang adalah saat tugas proses saat ini dimulai. Jika pengiriman atau masukan terjadi selama periode tugas proses sebelumnya, ada kemungkinan stok pengaman habis.
Sebaliknya, jika cara tumpang tindih adalah SSEE (Start-Start End-End), proses sebelumnya dan proses saat ini dapat tumpang tindih dengan syarat proses sebelumnya tidak selesai lebih dulu daripada proses saat ini. Dengan demikian, pesanan pengisian ulang dihasilkan secara bertahap selama tugas proses sebelumnya, sehingga kemungkinan kehabisan stok pengaman dapat diminimalkan.
Namun, SSEE didasarkan pada gagasan bahwa ukuran lot produksi adalah 1 unit dan barang mengalir per unit. Dalam kenyataannya, unit di mana barang mengalir di lapangan adalah unit lot produksi atau unit palet, sehingga tumpang tindih antar proses seperti SSEE tidak selalu dapat dicapai.
Apa yang Dapat Dilakukan dengan Fungsi "Pemecahan"
Seperti disebutkan di atas, karena tidak mungkin mencerminkan 100% kondisi pembatas yang sempurna ke dalam penjadwal, akurasi jadwal yang dihasilkan tidak akan 100%.
Namun, dengan melakukan "pemecahan", jadwal yang "secara teoritis dapat dilaksanakan tanpa keterlambatan pengiriman" dapat dibuat, yang tidak dapat ditangani oleh fungsi "penumpukan" MRP sistem manajemen produksi. Dengan mengatur cara tumpang tindih antar proses ke SSEE, jadwal yang secara teoritis mematuhi stok pengaman sebanyak mungkin dapat dibuat tanpa harus menghasilkan banyak pesanan produksi dengan ukuran lot 1 unit seperti dalam produksi aliran satu unit.
Perbedaan antara Agenda Seminar (Pemakaian Sumbu Waktu) dan Daftar Keinginan Akhir Pekan (Penumpukan Harian)
Misalnya, saat membuat agenda untuk mengadakan seminar, biasanya acara dialokasikan ke sumbu waktu dari waktu mulai hingga waktu selesai.
- Mulai dari waktu penerimaan (14:30), sambutan tuan rumah 10 menit (15:00-15:10), pembicara pertama 60 menit (15:10-16:10), istirahat 10 menit (16:10-16:20), pembicara kedua 40 menit (16:20-17:00), pembicara ketiga 50 menit (17:00-17:50), tanya jawab 10 menit (17:50-18:00)...
Ini dilakukan agar peserta dapat mengetahui dengan jelas waktu penampilan pembicara yang ingin mereka dengarkan sehingga bisa datang sesuai waktu, atau karena pembicara harus kembali ke kota asal dengan pesawat malam hari itu sehingga ditempatkan di sesi awal. Dengan kata lain, penugasan tugas ke sumbu waktu seperti "acara apa yang ada pada jam berapa" menjadi prioritas.
Secara umum, saat membuat jadwal, seperti WBS (Work Breakdown Structure) yang dibuat dalam proyek pengembangan sistem, tugas ditempatkan pada sumbu vertikal dan sumbu waktu pada sumbu horizontal untuk menentukan kapan tugas harus dimulai dan selesai.
Sebaliknya, saat membayangkan "daftar keinginan" untuk menyelesaikan tugas tertunda di akhir pekan, yang terpenting adalah berapa banyak tugas yang dapat ditumpuk dalam waktu yang tersedia untuk aktivitas di akhir pekan. Urutan pelaksanaan tugas mana yang didahulukan cukup dipikirkan saat hari Sabtu tiba dan bukanlah masalah penting pada tahap perencanaan.
- Di hari Sabtu sore, adik ipar akan berkunjung, jadi waktu kerja dari pagi hingga pukul 17:00 adalah 8 jam. Sisa tugas proyek 1 (2 jam), pembaruan blog (2 jam), tidur siang untuk mengatasi kurang tidur (2 jam), mencuci mobil (1 jam), belanja dan urusan di percetakan (2 jam). Waktu tampaknya tidak cukup (kapasitas berlebih), jadi mencuci mobil ditunda ke besok...
Pemikiran tentang Mengonsumsi Jumlah Sumber Daya Maksimum dengan Jumlah Sumber Daya yang Diperlukan
Saat membayangkan "daftar keinginan akhir pekan" seperti ini, secara tidak sadar terjadi perubahan pemikiran dari cara berpikir jadwal umum yaitu "mengalokasikan tugas ke sumbu waktu" menjadi "mengonsumsi waktu yang tersedia untuk aktivitas dengan waktu yang diperlukan untuk setiap tugas".
Jika ini diabstraksikan lebih jauh, "jumlah sumber daya maksimum" 8 jam per hari dikonsumsi dengan "jumlah sumber daya yang diperlukan" 2 jam untuk menyelesaikan proyek 1, "jumlah sumber daya yang diperlukan" 2 jam untuk pembaruan blog, "jumlah sumber daya yang diperlukan" 2 jam untuk tidur siang, "jumlah sumber daya yang diperlukan" 1 jam untuk pergi dan pulang dari tempat cuci mobil, dan "jumlah sumber daya yang diperlukan" 2 jam untuk menyelesaikan berbagai urusan.
Sebagai contoh lain, dalam proses perlakuan panas dengan tungku terowongan, jumlah troli yang dapat dipasang pada ban berjalan per hari adalah 1.000 unit, dan ini dikonsumsi dengan "jumlah pesanan x jumlah sumber daya yang diperlukan 1 unit".
- Jumlah troli yang dapat dipasang pada ban berjalan per hari 1.000 unit ⇒ jumlah sumber daya maksimum sumber daya utama (tungku terowongan)
- Jumlah pesanan x jumlah sumber daya yang diperlukan 1 unit ⇒ jumlah sumber daya yang diperlukan per item
- Jika flag jumlah sumber daya yang dialokasikan adalah "normal"
Jumlah sumber daya yang ditentukan dalam BOM produksi untuk setiap tugas akan dikonsumsi. - Jika flag jumlah sumber daya yang dialokasikan adalah "proporsional dengan kuantitas produksi"
Jumlah sumber daya yang dikonsumsi adalah kuantitas produksi tugas dikalikan dengan jumlah yang ditentukan dalam BOM produksi.
- Jika flag jumlah sumber daya yang dialokasikan adalah "normal"
- Waktu perlakuan panas tungku terowongan ⇒ waktu tunggu tetap 1 hari
Ukuran item yang menjalani perlakuan panas di tungku terowongan bervariasi, dan jika jumlah stok troli terbatas, jumlah sumber daya maksimum troli diatur ke jumlah stok, dan waktu lintasan troli diatur ke waktu tunggu tetap 1 hari, sama seperti waktu perlakuan panas tungku terowongan (sumber daya utama).
- Jumlah stok troli yang sesuai dengan setiap item ⇒ jumlah sumber daya maksimum sumber daya sekunder (troli)
- Waktu lintasan troli ⇒ waktu tunggu tetap 1 hari
Semakin kecil item, semakin banyak yang dapat dimuat pada troli. Dengan mengatur jumlah yang dapat dimuat pada instruksi keluaran untuk setiap item, dalam proses perlakuan panas, keluaran sebanyak jumlah yang dapat dimuat diperoleh untuk satu pesanan. Dengan kata lain, waktu perlakuan panas per unit di tungku terowongan berbanding terbalik dengan jumlah yang dapat dimuat.