Waktu Tunggu Perencanaan Produksi Dipersingkat dari 3 Hari Menjadi 1 Hari
PT. SMT Indonesia (selanjutnya disebut SMT) adalah perusahaan yang memproduksi komponen elektronik. Berdiri pada tahun 1996 di Pulau Batam seiring ekspansi produsen elektronik besar ke Indonesia (pindah ke lokasi saat ini pada tahun 1999).
![]() |
PT. SMT Indonesia ■ Alamat: EIJP Industrial Park, Plot 5C-2, Cikarang, Bekasi, Indonesia ■ Didirikan: Agustus 1996 ■ Modal: US$3.750.000 ■ Produk Utama: Pengolahan komponen elektronik secara kontrak |
Pada awalnya, perusahaan menghadapi berbagai kesulitan seperti perbedaan budaya dan kendala bahasa, namun dengan menerapkan sistem pelatihan, SMT berhasil membangun mekanisme untuk memastikan kualitas tinggi, sehingga produksi komponen elektronik di Indonesia semakin berkembang.
Selain transaksi dengan produsen elektronik besar yang menjadi pemicu ekspansi, bisnis SMT juga berkembang dengan meningkatnya transaksi untuk komponen kendaraan roda empat dan roda dua. Namun, seiring bertambahnya mitra bisnis, produksi menjadi semakin bervariasi, ditambah dengan permintaan besar khas negara berkembang yang membutuhkan produksi massal. Penyesuaian produksi yang dilakukan dengan taktik kuantitas tenaga kerja mulai mencapai batasnya, sehingga pada tahun 2007, SMT memutuskan untuk mengadopsi software Production Scheduler Asprova.
Kali ini, kami berkesempatan berbincang dengan Bapak Homma, Senior Manager yang ditugaskan ke Indonesia pada tahun 2008 dan memimpin implementasi Asprova.
Medan Pertempuran di Luar Negeri dengan Masalah Harian, Mengejar Sistem yang Sederhana untuk Digunakan
Ketika Bapak Homma tiba di Indonesia pada tahun 2008, Asprova belum dioperasikan dengan baik. Untuk mengatasinya, beliau mulai dengan mengevaluasi ulang sistem dan kondisi di lapangan. Dalam hal sistem, beliau mempelajari Asprova dan berpendapat, “Sistem ini sangat mempertimbangkan kebutuhan lapangan, memiliki banyak fungsi, dan sangat mendalam. Namun, jika salah langkah, sistem ini bisa menjadi sangat rumit.”
Saat itu, semua tahapan proses manufaktur—[Surface Mounting]–[Backside Mounting]–[Manual Insertion]–[Solder Bath]–[Testing]—didaftarkan ke Asprova untuk production scheduling. Karena produksi massal multi-variasi, jumlah data master sangat banyak, dan ketika parameter terkait urutan produksi ditambahkan, mengelola informasi dalam jumlah besar tersebut untuk menghasilkan schedule yang diharapkan menjadi sangat sulit. Ini persis seperti kekhawatiran Bapak Homma tentang sistem yang menjadi terlalu rumit.
Di sisi lapangan, untuk mengakomodasi produksi multi-variasi, lini produksi telah dipecah menjadi bagian-bagian kecil, membuat proses manufaktur semakin kompleks. Ditambah dengan masalah eksternal seperti keterlambatan pengiriman bahan, pesanan mendesak yang mengganggu schedule, dan kondisi khas luar negeri, proses manufaktur menjadi semakin rumit.
Akibatnya, waktu tunggu produksi menjadi lebih lama, dan stok barang dalam proses (WIP) meningkat.
Untuk mempersingkat waktu tunggu produksi dan menyederhanakan rencana produksi, lini produksi diubah menjadi lini produksi terintegrasi untuk membuat proses lebih mudah dipahami.
Peran Asprova difokuskan untuk memilih lini dan menentukan urutan input. Dengan mengejar kesederhanaan, waktu tunggu produksi berhasil dipersingkat dari 2 hari menjadi 2 jam, dan waktu perencanaan produksi dari 3 hari menjadi 1 hari.
“Tanpa Asprova, Operasional Tidak Akan Berjalan”
Indonesia, dengan populasi 240 juta jiwa yang menjadikannya negara keempat terpadat di dunia, memiliki prospek ekonomi yang sangat cerah, dengan permintaan domestik yang melonjak. Volume produksi SMT pun sangat besar, dengan banyak pekerja di lapangan, yang sebagian besar adalah wanita.
Hal ini karena proses produksi komponen elektronik, seperti penyolderan manual dan inspeksi visual, dianggap lebih cocok dilakukan oleh wanita karena sifatnya yang membutuhkan ketelitian. Kata kunci “Kaizen” seperti “Poka-Yoke” (pencegahan kesalahan) dan “visualisasi” terlihat di mana-mana, dengan perspektif khas wanita yang menambah keunikan dibandingkan dengan standar Jepang. Sistem pelatihan juga disediakan untuk memastikan kualitas yang konsisten.
Asprova digunakan untuk production scheduling otomatis dalam memilih lini dan urutan input. Prioritas per lini didaftarkan dalam data master untuk mengontrol pemilihan lini. Data performa harian juga dimasukkan ke Asprova untuk menyusun rencana pemulihan keterlambatan.
Alur kerjanya adalah sebagai berikut: pada hari Senin, pesanan dari pelanggan diterima; pada hari Selasa, rencana disusun menggunakan Asprova; pada hari Rabu, departemen manajemen produksi dan manufaktur berkumpul untuk mendiskusikan rencana yang dibuat pada hari Selasa. Dalam diskusi, mereka membahas, misalnya, pesanan yang berisiko terlambat, dampak perubahan lini, dll., sambil melihat layar Asprova untuk simulasi dan pengambilan keputusan produksi minggu berikutnya.
Pendekatan sederhana yang diterapkan Bapak Homma menghasilkan keuntungan: karena sederhana, semua orang dapat berpartisipasi dalam diskusi, dan pengambilan keputusan menjadi lebih cepat. Dalam hal transfer teknologi, pendekatan ini juga unggul.
Awalnya, Bapak Homma sendiri yang menyusun rencana di Asprova, tetapi setelah enam bulan, tugas tersebut berhasil dialihkan ke dua staf lokal, yang hingga kini masih mengoperasikan sistem. Mereka sepakat mengatakan, “Tanpa Asprova, operasional tidak akan berjalan.”
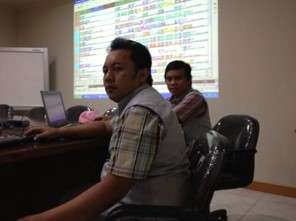
Pelanggan yang Mengadopsi Asprova