Konsep Smart Factory adalah perwujudan Industri 4.0 melalui transformasi digital (DX) industri manufaktur. Secara spesifik, MES (Manufacturing Execution System) digunakan untuk mengumpulkan dan mengelola informasi tingkat lapangan guna meningkatkan efisiensi produksi dan mengurangi biaya produksi, sementara MOM (Manufacturing Operations Management) mendorong otomatisasi lebih lanjut.
Transisi dari ERP ke MES dan kemudian ke MOM
Pada tanggal 4 hingga 7 Desember 2019, kami berpartisipasi dalam pameran manufaktur terbesar di Indonesia, "Manufacturing Indonesia 2019", yang diadakan setiap tahun di JIExpo Kemayoran, dengan membuka stan untuk memperkenalkan penjadwal produksi Asprova. Namun, karena industri roda dua dan roda empat di Indonesia sedang mengalami penurunan, jumlah pengunjung terasa lebih sedikit dibandingkan tahun-tahun sebelumnya. Sebaliknya, banyak orang dari negara-negara Asia seperti Singapura dan Korea mengunjungi stan kami untuk keperluan penjualan sistem terkait IoT dan otomatisasi pabrik.
Dari pembicaraan dengan mereka, ada satu hal yang menjadi kesamaan: sistem manufaktur telah bergeser dari Enterprise Resource Planning (ERP), yang dibagi berdasarkan fungsi bisnis seperti manajemen produksi, perencanaan produksi, manajemen penjualan dan pembelian, serta manajemen stok, menuju Manufacturing Execution System (MES) yang berfokus pada manajemen tingkat lapangan seperti manusia dan mesin. Ke depannya, sistem ini akan beralih ke Manufacturing Operations Management (MOM), yang mengintegrasikan dan mengotomatisasi serangkaian proses produksi seperti perencanaan, penjadwalan, manajemen produksi, manajemen tenaga kerja, dan manajemen kualitas, menuju otomatisasi dan operasi tanpa awak.
Di Indonesia, istilah MES sering diartikan sebagai terminal lapangan seperti PC atau tablet untuk memasukkan data produksi aktual atau tenaga kerja. Oleh karena itu, ketika ditanya, "Apakah penjadwal produksi merupakan salah satu fungsi MES?" saya awalnya menjawab "TIDAK". Namun, di tengah perjalanan, saya menyadari bahwa MES saat ini merujuk pada reorganisasi fungsi sistem ERP tradisional dari perspektif lapangan, sehingga saya mengubah jawaban menjadi "YA".
Seorang vendor IT manufaktur dari Singapura mengusulkan solusi terbaru untuk mewujudkan Smart Factory yang mengimplementasikan Industri 4.0. Mereka menyebutkan bahwa, selain teknologi IoT yang mengumpulkan informasi lapangan secara real-time dari PLC (Programmable Logic Controller) yang terhubung ke peralatan produksi dan inspeksi untuk kontrol dan manajemen, hanya dengan mengatur rencana produksi, semua proses mulai dari produksi hingga penggantian mesin saat terjadi NG (produk cacat) dapat diotomatisasi dan dijalankan tanpa awak. Hal ini membuat saya merasakan bahwa kita sedang berada dalam masa transisi tren sistem manufaktur.
Jika tujuan sistematisasi adalah penghematan tenaga, efisiensi, dan pencegahan kesalahan, maka DX, yang menjadi kata kunci akhir-akhir ini, bukan sekadar penggantian sistem yang ada, melainkan reformasi operasional dengan pendekatan "dengan IT, kita bisa melakukan hal-hal yang lebih nyaman".
Untuk melakukan reformasi operasional, reformasi operasi lapangan menjadi sangat penting. Dengan menciptakan konsep yang mewujudkan reformasi operasi lapangan melalui IT, peningkatan operasional dan pendapatan dapat tercapai, yang merupakan inti dari makna DX.
Smart Factory (Pabrik Cerdas) adalah konsep yang diwujudkan melalui DX industri manufaktur. Namun, karena istilah sistem manajemen produksi dan eksekusi tradisional telah direorganisasi dan didefinisikan ulang, gambaran umumnya menjadi sangat sulit dipahami.
Sebagai catatan tambahan, meskipun istilah "Smart Factory" sering terlihat di situs web Jepang, respons dari lawan bicara sering kali kurang antusias dan mereka tampak bingung. Belakangan saya mengetahui bahwa ini tampaknya merupakan istilah buatan Jepang (wasei-eigo) yang tidak dikenal di luar Jepang.
Definisi Baru MES
Menurut MESA, organisasi yang mempromosikan MES di Amerika Serikat, MES berada di antara lapisan ERP di atasnya dan lapisan PLC di bawahnya. MES memberikan instruksi kerja kepada pekerja (manusia) berdasarkan jadwal produksi, memantau pergerakan bahan baku dan barang setengah jadi (benda) secara real-time, serta terhubung langsung dengan peralatan produksi (mesin) untuk memahami status operasional dan mendeteksi anomali.
- ERP: Manajemen per proses dan departemen ⇒ Manajemen informasi yang akurat (pergerakan benda)
- MES: Manajemen per mesin dan tugas ⇒ Peningkatan efisiensi produksi dan pengurangan biaya produksi (tenaga kerja manusia, status operasional mesin)
- MOM: Otomatisasi MES
Secara sederhana, perbedaan antara ERP dan MES terletak pada unit manajemen. MES mengumpulkan dan mengelola informasi tingkat lapangan untuk meningkatkan efisiensi produksi dan mengurangi biaya produksi—misi utama industri manufaktur—sementara MOM mendorong otomatisasi melalui digitalisasi untuk menciptakan Smart Factory.
MES didefinisikan memiliki 11 fungsi berikut, di mana penjadwalan kerja, alokasi dan pemantauan sumber daya produksi, serta pengaturan kerja dan instruksi produksi adalah bidang yang menjadi keunggulan penjadwal produksi tradisional. Fungsi lainnya merupakan reorganisasi informasi yang dikelola ERP ke tingkat operasional lapangan.
- Penjadwalan kerja (Operations/Detail Sequencing)
- Alokasi dan pemantauan sumber daya produksi (Resource allocation and status)
- Pengaturan kerja dan instruksi produksi (Dispatching production unit)
- Analisis kinerja (Performance analysis)
- Manajemen pemeliharaan (Maintenance management)
- Manajemen proses (Process management)
- Manajemen kualitas (Quality management)
- Pengumpulan data (Data collection/acquisition)
- Pelacakan produk dan manajemen silsilah produksi (Production tracking and genealogy)
- Manajemen tenaga kerja (Labor management)
- Manajemen dokumen (Document control)
Perkembangan MES dan MOM pada dasarnya adalah peningkatan metode manajemen informasi, yang akhirnya harus terkait dengan misi industri manufaktur, yaitu "mengirimkan produk berkualitas tanpa keterlambatan".
Transformasi Smart Factory melalui DX di industri manufaktur diposisikan sebagai salah satu strategi nasional penting untuk meningkatkan kekayaan negara dengan memperkuat daya saing ekspor. Faktanya, negara-negara berkembang di seluruh dunia secara serentak mendefinisikan ulang Industri 4.0 sesuai kondisi lokal mereka untuk meningkatkan nilai tambah dan daya saing internasional industri manufaktur.
Banyaknya Orang Indonesia yang Berbicara Bahasa Jepang
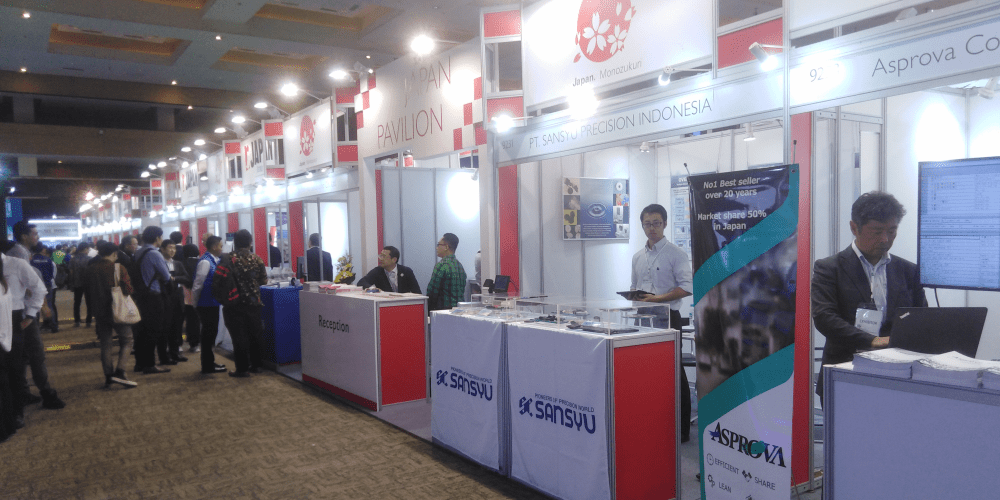
Meskipun globalisasi telah mengubah banyak hal akhir-akhir ini, banyak perusahaan Jepang di Indonesia masih bersifat "Galapagos" dalam arti tertentu, seperti mengutamakan hubungan kepercayaan berdasarkan kinerja masa lalu dan hanya menggunakan bahasa Jepang. Bagi orang Indonesia, kemampuan berbahasa Jepang menjadi peluang besar untuk mendapatkan keuntungan di pasar khusus ini.
Orang Indonesia yang fasih berbahasa Jepang yang mengunjungi stan kami dengan senang hati menceritakan pengalaman seperti "Saya tinggal di Osaka selama 3 tahun" atau "Saya pernah jadi pekerja magang di Hamamatsu". Namun, karena sisi gelap sistem pemagangan seperti kondisi kerja yang berat dan upah yang tidak dibayar sering disorot akhir-akhir ini, saya cukup ragu untuk bertanya, "Apakah hidup di Jepang menyenangkan?"
Beruntung, semua orang Indonesia yang saya ajak bicara dalam bahasa Jepang kali ini hanya menceritakan kenangan menyenangkan di Jepang. Namun, tampaknya ada masalah baru: para pekerja magang yang mengasah kemampuan bahasa Jepang mereka dan tetap tinggal di Jepang untuk menjadi pemandu wisata kota atau penerjemah telah menyebabkan penurunan drastis dalam tarif bisnis inbound.
Making Indonesia 4.0 sebagai Upaya Konkret terhadap Industri 4.0
Industri 4.0 adalah gerakan global untuk memicu revolusi industri keempat menggunakan teknologi IT. Ini melibatkan perpindahan teknologi IT yang awalnya berpusat pada perangkat lunak ke perangkat keras, menghubungkan perangkat keras dengan jaringan untuk pengumpulan dan analisis data yang lebih cepat dan akurat, guna meningkatkan produktivitas dan kualitas.
Dalam kasus Indonesia, dengan tujuan menjadi salah satu dari 10 ekonomi terbesar dunia pada tahun 2030, Kementerian Perindustrian mengumumkan Making Indonesia 4.0 pada April 2018 sebagai upaya terhadap Industri 4.0, dengan 10 prioritas nasional berikut:
- Peningkatan aliran bahan baku:
- Penciptaan nilai tambah melalui pengolahan domestik
- Peningkatan tingkat pengadaan lokal bahan baku oleh perusahaan domestik
- Redesain kawasan industri:
- Rencana sabuk industri otomotif Jawa Utara di sepanjang jalan tol yang diperpanjang hingga Jawa Timur
- Pengembangan pelabuhan baru Patimban di Subang, Jawa Barat (dijadwalkan 2023) untuk mengurangi konsentrasi pada Pelabuhan Tanjung Priok
- Penyusunan standar untuk keberlanjutan:
- Pemberdayaan usaha kecil dan menengah:
- Pengembangan dan penguatan infrastruktur digital nasional:
- Penarikan investasi dari luar negeri:
- Peningkatan kemampuan tenaga kerja industri:
- Bantuan ekosistem:
- R&D (penelitian dan pengembangan) oleh pemerintah, swasta, dan universitas
- Penerapan insentif untuk investasi pengembangan teknologi:
- Pelaksanaan relaksasi kebijakan, regulasi, dan sistem:
Pada tahun 2000-an, industri manufaktur Indonesia gagal beralih ke industri berbasis teknologi tinggi, dan kontribusi manufaktur terhadap PDB turun dari 20% di era Soeharto menjadi 16%. Melalui Making Indonesia 4.0, targetnya adalah meningkatkan kembali kontribusi manufaktur menjadi 25% pada tahun 2030 untuk merevitalisasi sektor ini, sehingga meningkatkan pertumbuhan ekonomi dari 5% saat ini menjadi 6-7%.
Bagaimana Pekerjaan Pengenalan Sistem Operasional Berubah melalui Pengurangan Kertas dan IoT
Langkah pertama yang harus dilakukan adalah mengubah informasi dari tiga dimensi menjadi dua dimensi melalui pengurangan kertas, seperti EDI (Electronic Data Interchange) untuk P/O dan faktur, serta pengumpulan data produksi aktual melalui input tablet atau penghitungan otomatis dari sequencer.
Ada dua jenis kesalahan yang mungkin terjadi sebelum informasi masuk ke jaringan digital:
- Kesalahan transkripsi saat memasukkan informasi dari kertas ke sistem ⇒ Pengurangan kertas
- Kesalahan input ke sistem ⇒ IoT
Pengurangan kertas sebagai bagian dari peningkatan operasional adalah tantangan yang cukup dapat dicapai dengan biaya tertentu, yang akan sepenuhnya menghilangkan kemungkinan kesalahan transkripsi. Namun, untuk menghilangkan kesalahan input ke sistem, diperlukan penerapan IoT di lini produksi untuk sepenuhnya menghapus tugas input informasi oleh manusia.
Dari perspektif cara kerja sistem operasional, dampak terbesar dari langkah-langkah perbaikan konkret yang dilakukan industri manufaktur melalui Industri 4.0 adalah pengurangan kertas dan IoT. Hal ini juga akan mengubah isi pekerjaan pengenalan sistem operasional.
- Bagaimana mengakses dan mengintegrasikan informasi
Dengan IoT, informasi yang diperlukan untuk peningkatan operasional dapat dikumpulkan dengan cepat dan akurat. Pertanyaannya menjadi bagaimana mengumpulkan dan menyentralisasi informasi ini, yang memerlukan pengembangan antarmuka antar sistem. - Dari sekadar mengumpulkan informasi dengan cepat dan akurat menjadi bagaimana menganalisis dan menampilkannya
Ketika data produksi aktual dikumpulkan secara real-time dan inventarisasi dilakukan secara akurat dalam sekejap melalui tag RFID (Radio Frequency Identifier), informasi yang tepat waktu dan akurat dianggap sudah ada di sistem. Sistem yang memungkinkan visualisasi, berbagi, dan sistematisasi data untuk dimanfaatkan secara efektif dalam peningkatan operasional menjadi diperlukan.
Untuk mewujudkan peningkatan nilai tambah dan daya saing internasional industri manufaktur Indonesia melalui Making Indonesia 4.0, diperlukan peningkatan kinerja seperti keandalan, fleksibilitas, dan responsivitas tidak hanya di dalam pabrik sendiri, tetapi juga di seluruh rantai pasok.
Dalam hal ini, diperlukan integrasi sistem antar perusahaan yang melakukan aktivitas ekonomi dalam rantai pasok. Oleh karena itu, sistem operasional internal perusahaan akan semakin dirancang dan diimplementasikan dengan mempertimbangkan hubungan dengan pemasok di hulu dan pelanggan di hilir rantai pasok.